The temperature used in hardening depends on the type of metal being treated and the desired properties. Generally, hardening involves heating the metal to a specific temperature (typically between 800°C and 950°C for steel), holding it at that temperature to allow the material to homogenize (soaking), and then rapidly cooling it (quenching) to lock in the hardened structure. This process alters the metal's microstructure, increasing its hardness and strength while reducing ductility. The exact temperature and soaking time vary based on the metal's composition and the intended application.
Key Points Explained:
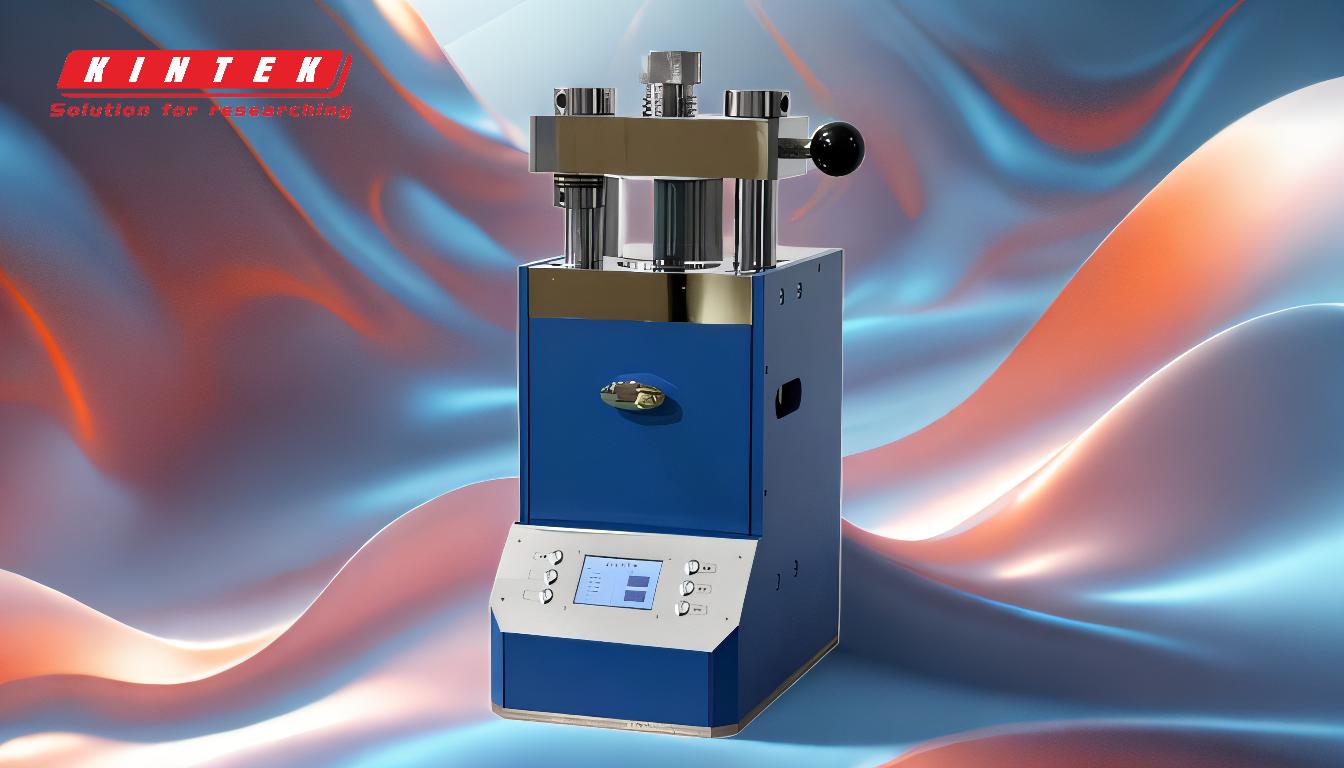
-
Purpose of Hardening:
- Hardening is a heat treatment process designed to increase the hardness and strength of metals, particularly steel. It achieves this by altering the metal's microstructure through controlled heating and cooling.
-
Heating Temperature:
- The heating temperature for hardening typically ranges between 800°C and 950°C for most steels. This range ensures the metal reaches its austenitizing temperature, where its crystal structure transforms into austenite, a phase that allows for the formation of a hardened structure upon cooling.
- For other metals, such as aluminum or titanium, the temperature range will differ based on their specific properties.
-
Soaking Time:
- After reaching the desired temperature, the metal is held at that temperature for a specific duration, known as soaking. This ensures the entire piece of metal reaches a uniform temperature and allows the microstructure to fully transform.
- Soaking time depends on the metal's thickness, composition, and the furnace's heating efficiency.
-
Quenching:
- Quenching is the rapid cooling of the metal, usually in water, oil, or air, to lock in the hardened structure. The cooling rate must be fast enough to prevent the formation of softer phases, such as pearlite, which would reduce hardness.
- The choice of quenching medium depends on the metal type and the desired hardness level.
-
Factors Influencing Hardening Temperature:
- Metal Composition: Alloying elements like carbon, chromium, and nickel affect the hardening temperature. For example, high-carbon steels require higher temperatures than low-carbon steels.
- Desired Properties: The intended use of the metal determines the optimal hardening temperature. For instance, tools requiring high wear resistance may need higher temperatures than structural components.
- Furnace Type: The type of furnace used, such as a muffle furnace, can influence temperature control and uniformity.
-
Common Applications:
- Hardening is widely used in manufacturing tools, automotive components, and industrial machinery where high strength and wear resistance are critical.
By carefully controlling the heating temperature, soaking time, and quenching process, manufacturers can achieve the desired hardness and mechanical properties in metals, ensuring they meet the requirements of their specific applications.
Summary Table:
Aspect | Details |
---|---|
Heating Temperature | 800°C–950°C for steel; varies for other metals. |
Soaking Time | Depends on metal thickness, composition, and furnace efficiency. |
Quenching Medium | Water, oil, or air, depending on metal type and desired hardness. |
Key Influencing Factors | Metal composition, desired properties, and furnace type. |
Common Applications | Tools, automotive components, and industrial machinery. |
Need help selecting the right hardening process for your metals? Contact our experts today!