Thermal evaporation is a widely used physical vapor deposition (PVD) technique for creating thin films on substrates. It involves heating a solid material in a high vacuum chamber until it evaporates, forming a vapor stream that travels through the vacuum and deposits onto a substrate, forming a thin film. This method is particularly effective for materials with relatively low melting points and is commonly used in applications like OLEDs and thin-film transistors. The process relies on resistive heating or electron beam heating to vaporize the target material, ensuring a high-purity deposition. Below, the key aspects of thermal evaporation are explained in detail.
Key Points Explained:
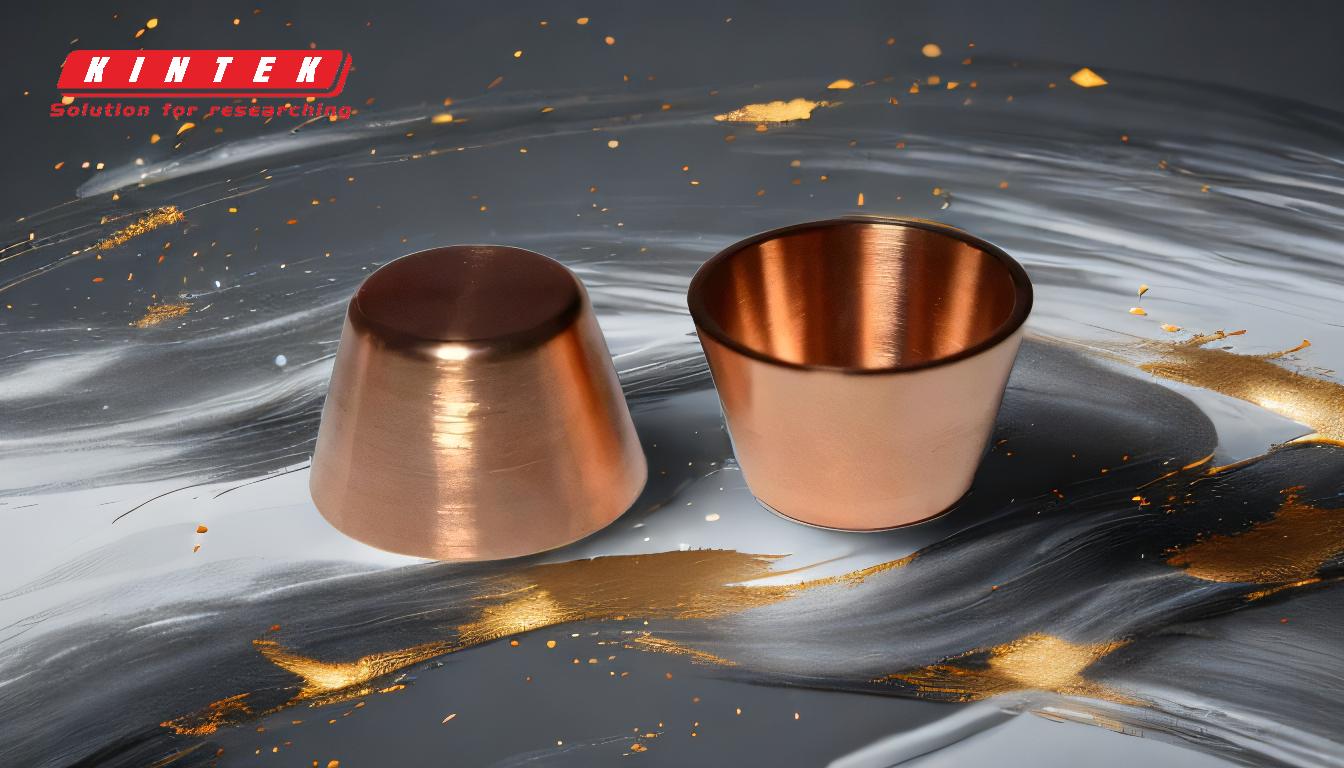
-
Basic Principle of Thermal Evaporation:
- Thermal evaporation operates on the principle of heating a solid material in a high vacuum environment until it vaporizes. The vaporized material forms a cloud that traverses the vacuum chamber and deposits onto a substrate, creating a thin film.
- The vacuum environment is crucial as it prevents the vaporized material from reacting with other atoms or scattering, ensuring a clean and uniform deposition.
-
Heating Mechanisms:
- Resistive Heating: A common method where a tungsten filament or boat is used to heat the target material. The material is placed in or near the heating element, which is resistively heated to high temperatures, causing the material to evaporate.
- Electron Beam Heating: An alternative method where an electron beam is focused on the target material, providing localized heating. This is particularly useful for materials with high melting points or those that may react with resistive heating elements.
-
Vacuum Environment:
- The process occurs in a high vacuum chamber, typically at pressures of 10^-5 to 10^-7 Torr. This low-pressure environment minimizes contamination and ensures that the vaporized material travels directly to the substrate without interference.
- The vacuum also reduces the risk of oxidation or other chemical reactions, which is critical for maintaining the purity of the deposited film.
-
Material Considerations:
- Thermal evaporation is suitable for materials that can be vaporized at relatively low temperatures, such as metals (e.g., aluminum, gold, silver) and some organic compounds.
- Materials with high melting points or those that decompose at high temperatures may require alternative deposition methods like electron beam evaporation or sputtering.
-
Applications of Thermal Evaporation:
- OLEDs (Organic Light-Emitting Diodes): Thermal evaporation is widely used to deposit organic layers in OLED displays due to its ability to create uniform, high-purity films.
- Thin-Film Transistors: The method is also employed in the fabrication of thin-film transistors, where precise control over film thickness and uniformity is essential.
- Optical Coatings: Thermal evaporation is used to create anti-reflective coatings, mirrors, and other optical components.
-
Advantages of Thermal Evaporation:
- Simplicity: The process is straightforward and does not require complex equipment compared to other PVD techniques.
- High Purity: The vacuum environment and direct heating mechanism ensure minimal contamination.
- Uniform Deposition: The method allows for precise control over film thickness and uniformity, making it ideal for applications requiring high-quality coatings.
-
Limitations of Thermal Evaporation:
- Material Restrictions: Not all materials are suitable for thermal evaporation, particularly those with high melting points or poor thermal stability.
- Line-of-Sight Deposition: The process is line-of-sight, meaning only surfaces directly exposed to the vapor stream will be coated. This can limit its use for complex geometries or shadowed areas.
- Scalability: While effective for small-scale applications, scaling up thermal evaporation for large-area coatings can be challenging.
-
Comparison with Other Deposition Methods:
- Sputtering: Unlike thermal evaporation, sputtering uses energetic ions to dislodge atoms from a target material, making it suitable for a wider range of materials, including those with high melting points.
- Chemical Vapor Deposition (CVD): CVD involves chemical reactions to deposit thin films, offering better step coverage and conformality but often requiring higher temperatures and more complex equipment.
In summary, thermal evaporation is a versatile and effective method for depositing thin films, particularly for materials with low melting points and applications requiring high purity and uniformity. While it has some limitations, its simplicity and reliability make it a popular choice in industries ranging from electronics to optics.
Summary Table:
Aspect | Details |
---|---|
Principle | Heating a solid material in a vacuum to vaporize and deposit it on a substrate. |
Heating Mechanisms | Resistive heating (tungsten filament/boat) or electron beam heating. |
Vacuum Environment | Operates at 10^-5 to 10^-7 Torr to minimize contamination and oxidation. |
Suitable Materials | Metals (e.g., aluminum, gold) and low-melting-point organic compounds. |
Applications | OLEDs, thin-film transistors, optical coatings (mirrors, anti-reflective). |
Advantages | Simple, high-purity, uniform deposition. |
Limitations | Material restrictions, line-of-sight deposition, scalability challenges. |
Comparison | Sputtering: wider material range; CVD: better conformality but complex. |
Discover how thermal evaporation can enhance your thin-film applications—contact our experts today!