A high-frequency induction furnace operates on the principles of electromagnetic induction and the Joule effect, enabling non-contact heating of conductive materials. The furnace converts standard power frequency alternating current (50Hz) into medium-frequency current (300Hz to 1000Hz) using a power supply device. This medium-frequency current flows through an induction coil, generating a high-density magnetic field that induces eddy currents in the metal placed within the coil. These eddy currents generate heat due to the Joule effect, melting the metal. The process also involves electromagnetic stirring, where the interaction between the inductor and the molten metal causes movement, ensuring uniform heating and mixing. The system operates similarly to a transformer, with the induction coil acting as the primary winding and the metal as the secondary winding, transferring electrical energy into heat energy without direct contact.
Key Points Explained:
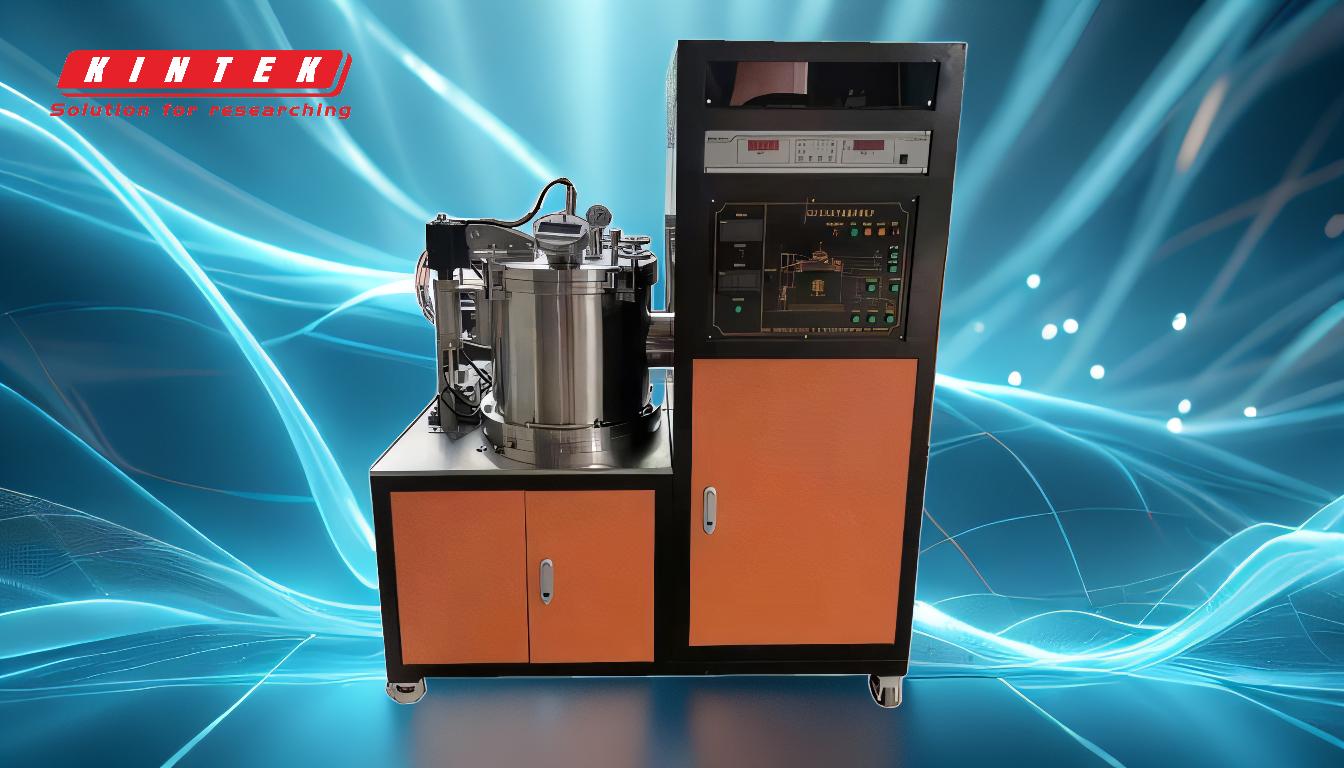
-
Electromagnetic Induction and Joule Effect:
- The core principle of a high-frequency induction furnace is electromagnetic induction, where a changing magnetic field induces electric currents (eddy currents) in conductive materials.
- The Joule effect refers to the heat generated when these eddy currents flow through the metal's resistance, leading to heating and eventual melting.
-
Power Conversion and Medium-Frequency Current:
- The furnace uses a power supply device to convert standard 50Hz alternating current into medium-frequency current (300Hz to 1000Hz).
- This conversion involves two stages: rectifying the AC to DC and then inverting the DC to adjustable medium-frequency AC.
- The medium-frequency current is crucial for generating a high-density magnetic field, which enhances the efficiency of the induction process.
-
Induction Coil and Magnetic Field Generation:
- The medium-frequency current flows through an induction coil, creating a high-density magnetic field.
- This magnetic field cuts through the metal placed inside the coil, inducing eddy currents within the metal.
- The induction coil is typically water-cooled to prevent overheating and maintain efficiency.
-
Eddy Currents and Heat Generation:
- The induced eddy currents flow through the metal, encountering resistance, which generates heat due to the Joule effect.
- The heat generated is proportional to the square of the current and the resistance of the metal, leading to rapid and efficient heating.
-
Electromagnetic Stirring:
- The interaction between the magnetic field generated by the induction coil and the molten metal creates electromagnetic forces.
- These forces cause the molten metal to move, a phenomenon known as electromagnetic stirring.
- Stirring ensures uniform temperature distribution and mixing, which is essential for consistent melting and alloying processes.
-
Transformer Analogy:
- The induction furnace operates similarly to a transformer, where the induction coil acts as the primary winding and the metal charge as the secondary winding.
- The primary coil (induction coil) is connected to the AC power supply, while the secondary coil (metal charge) heats up due to induced currents.
- This analogy helps in understanding the energy transfer mechanism, where electrical energy is converted into heat energy without direct contact.
-
Non-Contact Heating:
- One of the significant advantages of induction furnaces is non-contact heating, where the induction coil does not physically touch the metal.
- This feature minimizes contamination and allows for precise control over the heating process, making it suitable for high-purity applications.
-
High Efficiency and Control:
- High-frequency induction furnaces are highly efficient due to the direct transfer of energy to the metal.
- The process allows for precise control over temperature and heating rates, which is critical for applications requiring specific metallurgical properties.
-
Applications and Advantages:
- Induction furnaces are widely used in metal melting, casting, and alloying processes.
- The advantages include rapid heating, energy efficiency, clean operation, and the ability to handle a wide range of metals and alloys.
By understanding these key points, one can appreciate the sophisticated yet efficient working principle of high-frequency induction furnaces, making them indispensable in modern metallurgical processes.
Summary Table:
Key Aspect | Description |
---|---|
Core Principle | Electromagnetic induction and Joule effect generate heat in conductive materials. |
Power Conversion | Converts 50Hz AC to medium-frequency current (300Hz–1000Hz) for efficient heating. |
Induction Coil | Generates a high-density magnetic field to induce eddy currents in the metal. |
Heat Generation | Eddy currents flow through metal resistance, producing heat via the Joule effect. |
Electromagnetic Stirring | Ensures uniform heating and mixing of molten metal for consistent results. |
Non-Contact Heating | Induction coil heats metal without physical contact, minimizing contamination. |
Applications | Used in metal melting, casting, and alloying for rapid, energy-efficient results. |
Ready to enhance your metal processing with a high-frequency induction furnace? Contact us today to learn more!