Vacuum in thin film deposition refers to the controlled environment where the pressure is significantly reduced to create a low-density gas state. This environment is crucial for processes like Physical Vapor Deposition (PVD) and thermal evaporation, as it minimizes contamination, enhances the mean free path of atoms, and ensures the purity and quality of the deposited film. Vacuum conditions are essential for achieving high-quality thin films with strong adhesiveness and minimal defects, making them indispensable in applications such as microchip manufacturing, optical coatings, and protective layers on metal parts.
Key Points Explained:
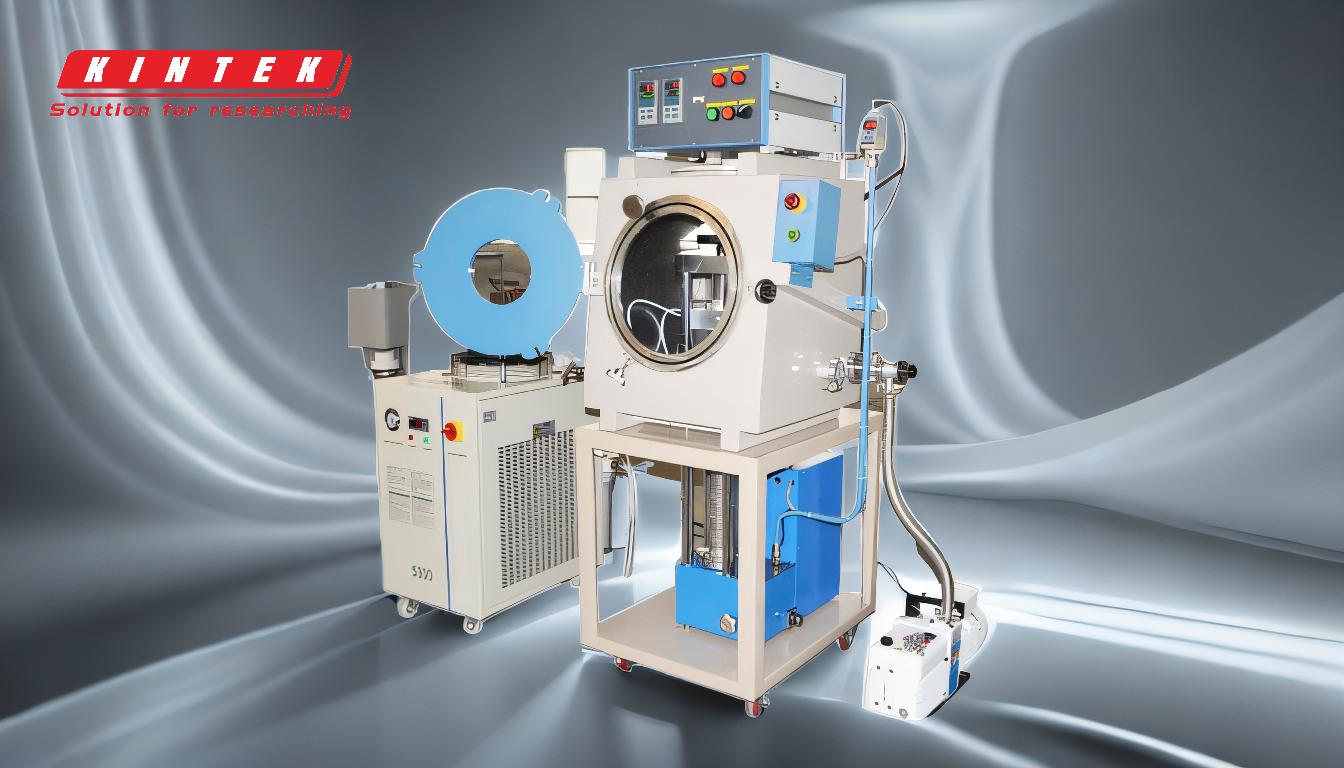
-
Definition and Purpose of Vacuum in Thin Film Deposition:
- A vacuum is a low-pressure environment where the density of gas molecules is significantly reduced.
- In thin film deposition, a vacuum is essential to minimize contamination from air or other gases, ensuring the purity and quality of the deposited film.
- It also facilitates processes like PVD and thermal evaporation by providing a clean and controlled environment.
-
Importance of Vacuum in PVD and Thermal Evaporation:
- Reduced Contamination: A vacuum environment minimizes the presence of unwanted substances like oxygen, nitrogen, and carbon dioxide, which can react with the film material or cause defects.
- Increased Mean Free Path: Lower gas density in a vacuum allows atoms or molecules to travel longer distances without collisions, ensuring directional deposition and uniform film formation.
- Enhanced Thermal Evaporation Rate: A vacuum enables higher evaporation rates by reducing the pressure, which is critical for efficient thin film deposition.
-
Vacuum Levels and Their Impact on Thin Film Quality:
- High Vacuum (10^-6 Torr): This level is necessary for processes like resistive evaporation, where maintaining film purity and directional deposition is critical.
- Ultra-High Vacuum (10^-9 Torr or lower): This level is required for advanced applications like microchip manufacturing, where even trace contaminants can cause significant defects.
- Maintaining specific vacuum levels ensures the absence of background gases that could compromise film quality.
-
Role of Vacuum in Reducing Defects and Enhancing Adhesiveness:
- A vacuum environment prevents unwanted substances from obstructing the movement of film particles, which can weaken the adhesiveness of the film.
- It also prevents the film material from bonding with other substances in the air, ensuring a pure and adherent thin film.
-
Applications of Vacuum in Thin Film Deposition:
- Microelectronics: High vacuum is critical for manufacturing microchips, where even small particles can cause defects.
- Optical Coatings: Vacuum deposition is used to create high-purity optical coatings for lenses, mirrors, and other optical components.
- Protective Layers: Vacuum coating processes are employed to form protective layers on metal parts, enhancing their durability and performance.
-
Challenges and Considerations in Maintaining Vacuum:
- Achieving and maintaining ultra-high vacuum levels requires specialized equipment and rigorous procedures.
- Contamination from residual gases or leaks can compromise the quality of the thin film, making regular monitoring and maintenance essential.
By understanding the role of vacuum in thin film deposition, manufacturers can optimize their processes to produce high-quality films with minimal defects and strong adhesiveness, meeting the demands of advanced applications in electronics, optics, and materials science.
Summary Table:
Key Aspect | Details |
---|---|
Definition of Vacuum | Low-pressure environment reducing gas density for minimal contamination. |
Importance in PVD & Evaporation | Reduces contamination, increases mean free path, and enhances evaporation. |
Vacuum Levels | High Vacuum (10^-6 Torr) and Ultra-High Vacuum (10^-9 Torr) for precision. |
Role in Reducing Defects | Prevents unwanted substances, ensuring pure and adherent thin films. |
Applications | Microelectronics, optical coatings, and protective layers on metal parts. |
Challenges | Requires specialized equipment and rigorous maintenance to prevent leaks. |
Optimize your thin film deposition process with expert guidance—contact us today!