Furnace linings are constructed using a variety of refractory materials, chosen based on the specific requirements of the furnace, such as temperature resistance, thermal insulation, and durability. Common materials include fire clay, high alumina, silica, magnesia, and advanced materials like alumina fiber, vacuum-formed fiber materials, and light hollow aluminum oxide plates. These materials ensure high service temperatures, rapid heat and cold resistance, and excellent thermal insulation. Additionally, muffle furnaces often use stainless steel or high-strength alumina for corrosion resistance and uniform heating. Rotary furnaces combine refractory materials with castables to maximize efficiency and reduce skin temperature. The choice of material depends on the furnace type and operational conditions.
Key Points Explained:
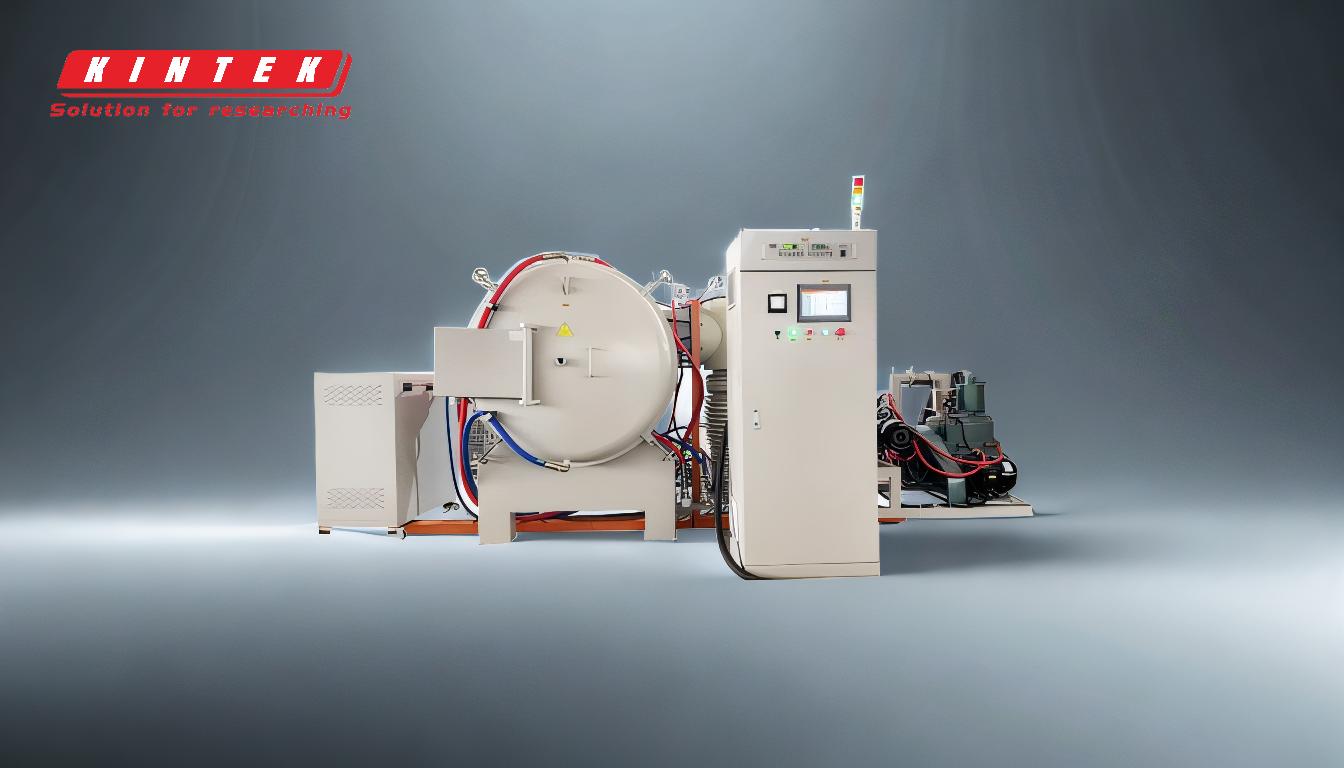
-
Common Refractory Materials for Furnace Linings:
- Fire Clay: Made from clay, used in lower-temperature furnaces due to its cost-effectiveness and adequate thermal resistance.
- High Alumina: Offers higher temperature resistance and durability, suitable for more demanding furnace environments.
- Silica: Known for its high thermal shock resistance, often used in furnaces with rapid temperature changes.
- Magnesia: Used in furnaces requiring resistance to basic slags and high temperatures, such as steelmaking furnaces.
-
Advanced Materials for High-Performance Linings:
- High-Purity Alumina Fiber: Provides excellent thermal insulation, rapid heat and cold resistance, and durability. Ideal for high-temperature applications.
- Vacuum-Formed Fiber Material: Lightweight and offers superior insulation properties, reducing heat loss and improving furnace efficiency.
- Light Hollow Aluminum Oxide Plate: Combines low heat storage with high thermal resistance, ensuring energy efficiency and durability.
-
Specialized Linings for Specific Furnace Types:
- Muffle Furnaces: Typically lined with stainless steel for corrosion resistance or high-strength alumina and silicon carbide (SiC) for uniform heating and durability.
- Rotary Furnaces: Use a combination of refractory materials and castables to ensure maximum efficiency, reduced skin temperature, and superior performance.
-
Key Properties of Furnace Lining Materials:
- High Service Temperature: Materials must withstand extreme heat without degrading.
- Thermal Insulation: Reduces heat loss and improves energy efficiency.
- Rapid Heat and Cold Resistance: Prevents cracking or damage during temperature fluctuations.
- Durability: Ensures long service life and minimal maintenance.
-
Material Selection Considerations:
- Furnace Type: Different furnaces (e.g., muffle, rotary) require specific materials tailored to their operational conditions.
- Operational Temperature: Materials must match the furnace's maximum operating temperature.
- Chemical Environment: Resistance to corrosion or chemical reactions with furnace contents is critical.
- Energy Efficiency: Materials with low heat storage and high insulation properties reduce energy consumption.
By carefully selecting the appropriate lining material, furnace operators can ensure optimal performance, longevity, and energy efficiency, tailored to their specific application.
Summary Table:
Material | Key Properties | Applications |
---|---|---|
Fire Clay | Cost-effective, adequate thermal resistance | Lower-temperature furnaces |
High Alumina | High temperature resistance, durability | Demanding furnace environments |
Silica | High thermal shock resistance | Furnaces with rapid temperature changes |
Magnesia | Resistant to basic slags, high temperatures | Steelmaking furnaces |
High-Purity Alumina Fiber | Excellent thermal insulation, rapid heat/cold resistance | High-temperature applications |
Vacuum-Formed Fiber | Lightweight, superior insulation, reduced heat loss | Energy-efficient furnaces |
Light Hollow Alumina Plate | Low heat storage, high thermal resistance | Energy-efficient and durable linings |
Stainless Steel | Corrosion resistance, uniform heating | Muffle furnaces |
Refractory + Castables | Maximum efficiency, reduced skin temperature | Rotary furnaces |
Need help selecting the right furnace lining material? Contact our experts today for tailored solutions!