High-temperature furnaces are designed to withstand extreme heat and harsh conditions, making material selection critical. They are constructed using a combination of insulation materials, refractory materials, and specialized heating elements. Insulation materials like lightweight alumina ceramic fiber and high-quality insulation boards minimize heat loss and energy consumption. Refractory materials such as alumina ceramic or quartz glass form the furnace chamber, offering high temperature and corrosion resistance. Heating elements are made from exotic materials like silicon carbide, molybdenum disilicide, or platinum, ensuring durability and efficient heat generation. These materials work together to create a robust and energy-efficient furnace capable of operating at high temperatures.
Key Points Explained:
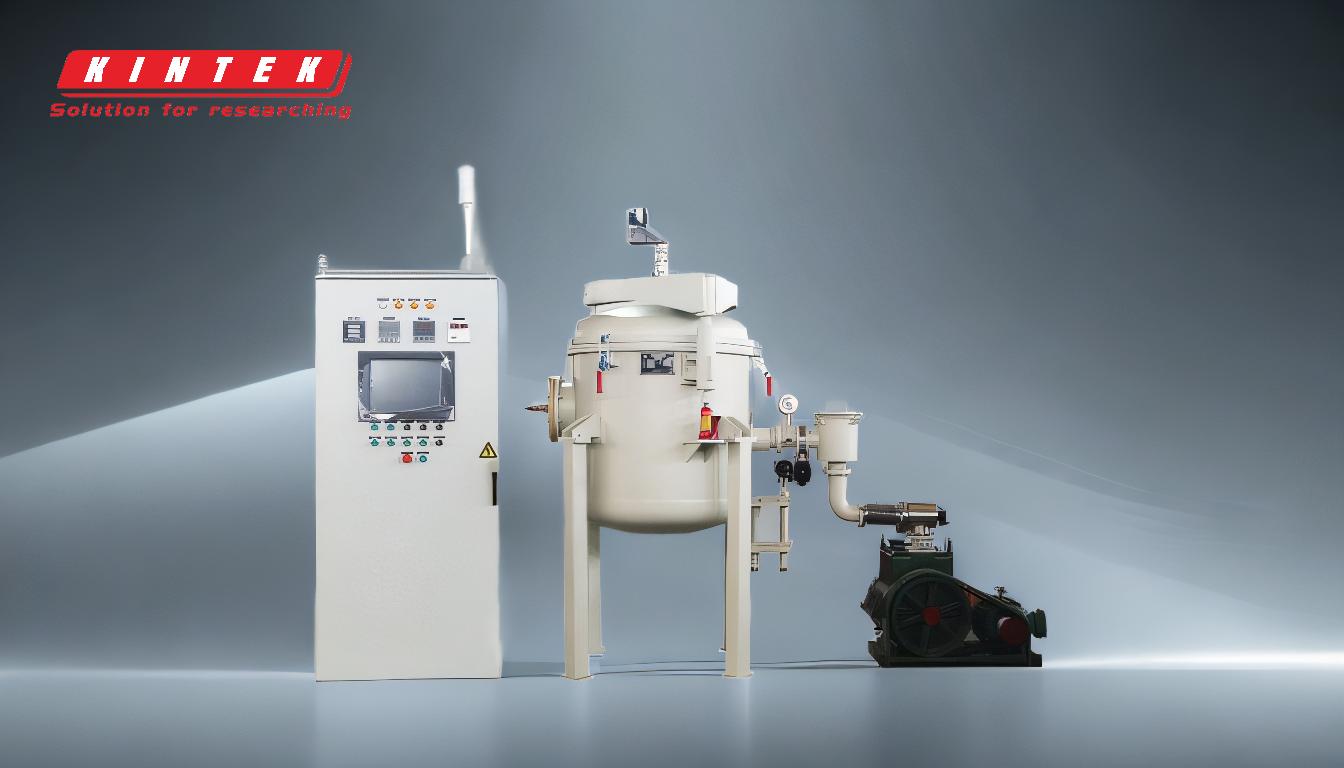
-
Insulation Materials:
- Lightweight Alumina Ceramic Fiber: This material is used for its excellent thermal insulation properties, reducing heat loss and improving energy efficiency.
- High-Quality Insulation Boards: These boards provide additional backing to the insulation layers, further enhancing thermal efficiency.
- Asbestos-Free Design: Modern furnaces avoid asbestos, ensuring safer and more environmentally friendly operation.
-
Refractory Materials:
- Alumina Ceramic: Commonly used for furnace chambers, alumina ceramic is highly resistant to high temperatures and chemical corrosion, making it ideal for most high-temperature applications.
- Quartz Glass: Known for its transparency, quartz glass allows for visual monitoring of experiments while maintaining high temperature and corrosion resistance.
-
Heating Elements:
- Silicon Carbide (SiC): SiC heating rods are widely used due to their excellent thermal conductivity, high melting point, and resistance to thermal shock.
- Molybdenum Disilicide (MoSi2): This material is chosen for its ability to withstand extremely high temperatures and its oxidation resistance.
- Platinum and Tungsten: These exotic materials are used in specialized applications where extreme temperature resistance and durability are required.
- Iron-Chrome Aluminum and Nickel Chrome Alloys: Commonly used in industrial furnaces, these alloys are shaped into various forms (cylindrical, semi-circular, or flat panels) to provide efficient and uniform heating.
-
Refractory Metals:
- Dense and Hard Materials: Refractory metals like tungsten and molybdenum are used in furnace construction due to their high density, hardness, and resistance to heat and wear.
- High Melting Points: These metals can withstand the extreme temperatures encountered in high-temperature furnaces without degrading.
-
Design Considerations:
- Multi-Layer Insulation: The use of multiple layers of insulation materials ensures minimal heat loss and optimal energy efficiency.
- Vertical Installation of Heating Rods: This design allows for uniform heat distribution and efficient operation of the furnace.
By combining these materials and design principles, high-temperature furnaces achieve the necessary durability, efficiency, and performance required for demanding industrial and laboratory applications.
Summary Table:
Component | Materials | Key Benefits |
---|---|---|
Insulation Materials | Lightweight Alumina Ceramic Fiber, High-Quality Insulation Boards | Minimize heat loss, improve energy efficiency, asbestos-free design |
Refractory Materials | Alumina Ceramic, Quartz Glass | High temperature and corrosion resistance, transparent for visual monitoring |
Heating Elements | Silicon Carbide (SiC), Molybdenum Disilicide (MoSi2), Platinum, Tungsten | High thermal conductivity, extreme temperature resistance, durability |
Refractory Metals | Tungsten, Molybdenum | High density, hardness, and resistance to heat and wear |
Design Considerations | Multi-Layer Insulation, Vertical Installation of Heating Rods | Uniform heat distribution, minimal heat loss, energy efficiency |
Need a high-temperature furnace tailored to your needs? Contact our experts today for a customized solution!