Selecting the right crucible size is a critical decision that depends on multiple factors, including the type of furnace, the material being processed, the operating conditions, and specific application requirements. A crucible that is too small may limit the amount of material you can process, while one that is too large may not fit in the furnace or could lead to inefficiencies. The material of the crucible, its compatibility with the furnace, and its ability to withstand the required temperatures and chemical environments must also be considered. Below, we break down the key considerations to help you determine the appropriate crucible size for your needs.
Key Points Explained:
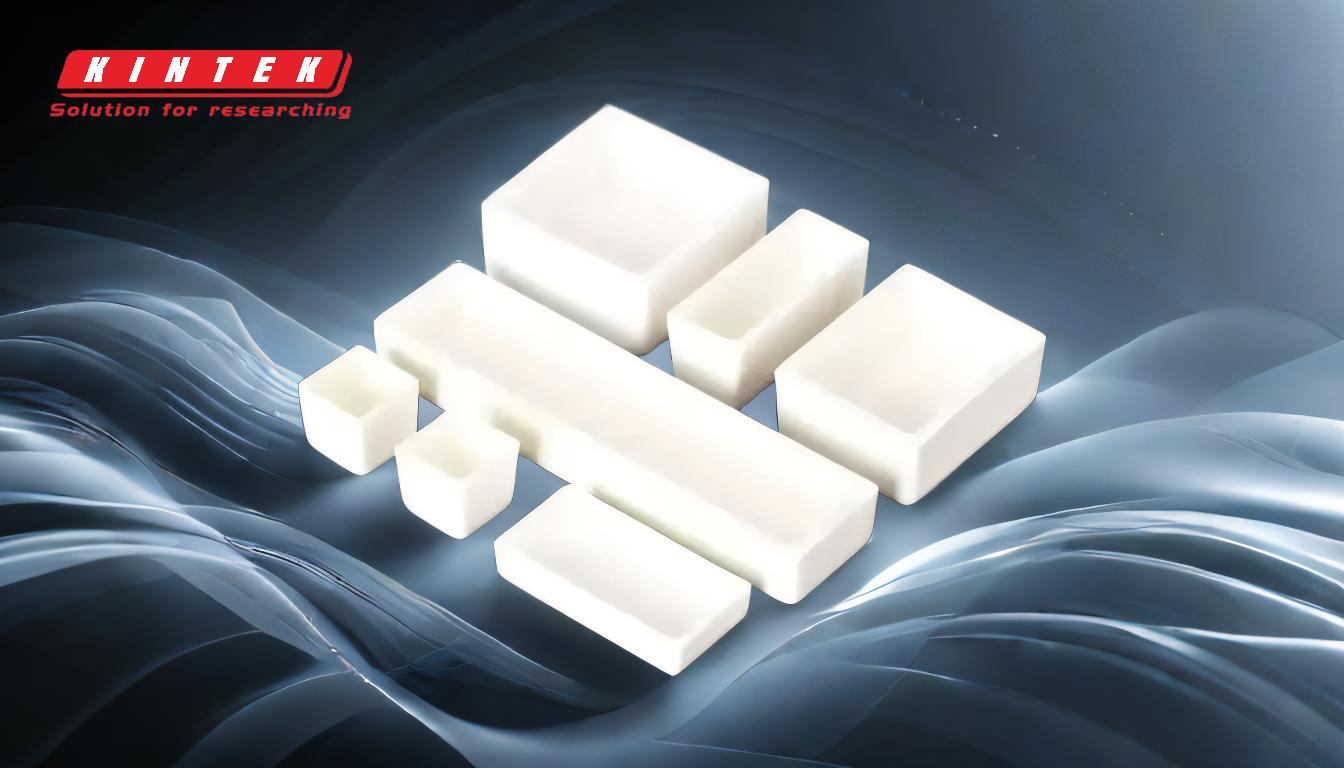
-
Furnace Compatibility
- The size and shape of the crucible must match the furnace's design and capacity.
- For example, taller crucibles may hold more material but may not be compatible with multi-hearth furnaces designed for shorter crucibles.
- Always check the furnace specifications to ensure the crucible dimensions (height, diameter, and shape) fit properly.
-
Material Capacity
- The crucible size should accommodate the volume of material you intend to process.
- Consider both the melting and holding capacities, as well as any additional space needed for fluxes, additives, or slag removal.
- Overfilling a crucible can lead to spillage, while underfilling may reduce efficiency.
-
Application-Specific Requirements
- For scientific applications, crucibles must be made of inert materials (e.g., platinum or zirconium) to prevent contamination of the sample.
- In industrial settings, the crucible material must match the alloy being melted and withstand the required temperatures (e.g., zirconia crucibles for temperatures above 2100°C).
-
Electrical and Thermal Properties
- For induction furnaces, the crucible's electrical resistivity must match the furnace's operating frequency.
- Lower frequency furnaces may require crucibles with high silicon carbide content, while higher frequency furnaces may need crucibles with high clay content.
- Mismatched electrical properties can lead to overheating or inefficient melting.
-
Operational Considerations
- Consider how the crucible will be charged (e.g., manual or automated), the temperature change rates, and the degassing or refining processes.
- Ensure the crucible can handle the thermal shock and mechanical stress during heating, cooling, and material transfer.
- Slag or dross removal methods and crucible emptying processes should also be factored into size selection.
-
Avoiding Cross-Contamination
- If processing multiple alloys or materials, ensure the crucible size and material are suitable to prevent cross-contamination.
- For example, using separate crucibles for different alloys or thoroughly cleaning crucibles between uses may be necessary.
-
Temperature and Chemical Stability
- The crucible material must withstand the maximum operating temperature and resist chemical reactions with the material being processed.
- For high-temperature applications, materials like zirconia or graphite are often preferred due to their thermal stability.
-
Sample Dimensions
- The crucible must accommodate the physical dimensions of the sample or material being processed.
- Ensure there is enough space for the sample to expand during heating and for any necessary stirring or mixing.
By carefully evaluating these factors, you can determine the appropriate crucible size for your specific application. Always consult the furnace manufacturer's guidelines and consider the material properties and operational requirements to ensure optimal performance and longevity of both the crucible and the furnace.
Summary Table:
Factor | Key Considerations |
---|---|
Furnace Compatibility | Match crucible size and shape to furnace design and capacity. |
Material Capacity | Ensure the crucible accommodates the volume of material and allows for additives. |
Application Requirements | Use inert materials for scientific applications; match alloy and temperature for industrial use. |
Electrical Properties | Align crucible resistivity with furnace frequency to avoid overheating or inefficiency. |
Operational Needs | Consider charging methods, thermal shock resistance, and slag removal processes. |
Cross-Contamination | Use separate crucibles or clean thoroughly when processing multiple materials. |
Temperature Stability | Choose materials like zirconia or graphite for high-temperature applications. |
Sample Dimensions | Ensure the crucible accommodates sample expansion and stirring needs. |
Need help selecting the right crucible size for your application? Contact our experts today for personalized advice!