Thin film deposition is a critical process in various industries, including electronics, optics, and energy, where materials are applied in thin layers onto substrates. The choice of substrate material is crucial as it directly impacts the performance, durability, and functionality of the thin film. Common substrates used in thin film deposition include metals, oxides, and compounds, each with distinct properties that make them suitable for specific applications. Metals are valued for their strength and durability but can be costly. Oxides offer high-temperature resistance and durability but may be brittle. Compounds provide a balance of strength and durability but can be expensive and challenging to work with. The selection of the appropriate substrate depends on the desired properties of the final product, such as conductivity, thermal stability, and mechanical strength.
Key Points Explained:
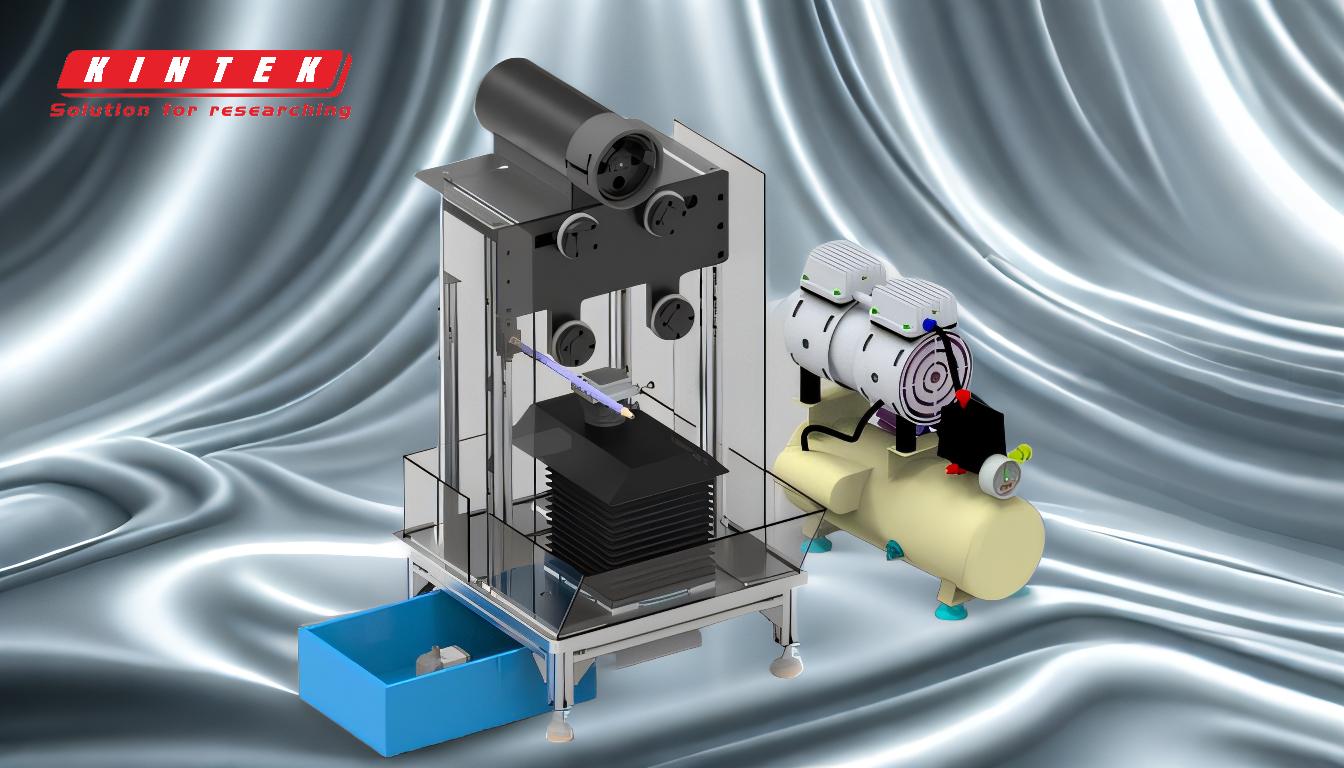
-
Metals as Substrates:
- Properties: Metals are known for their strength, durability, and excellent electrical conductivity. They are often used in applications requiring high thermal and electrical performance.
- Advantages: Metals like aluminum, copper, and gold are commonly used due to their ability to form strong, adherent films. They are also relatively easy to deposit using techniques such as sputtering or evaporation.
- Disadvantages: The primary drawback of metals is their cost. Precious metals like gold and silver are particularly expensive, which can limit their use in cost-sensitive applications. Additionally, some metals may oxidize or corrode over time, affecting the longevity of the thin film.
-
Oxides as Substrates:
- Properties: Oxides, such as silicon dioxide (SiO₂) and aluminum oxide (Al₂O₃), are valued for their durability and ability to withstand high temperatures. They are often used in applications requiring thermal stability and electrical insulation.
- Advantages: Oxides are highly resistant to environmental factors such as moisture and oxidation, making them ideal for protective coatings. They also provide excellent dielectric properties, which are essential in electronic applications.
- Disadvantages: The brittleness of oxides can be a significant drawback, especially in applications where mechanical flexibility is required. Additionally, depositing oxide films often requires high-temperature processes, which can be energy-intensive and may limit the types of substrates that can be used.
-
Compounds as Substrates:
- Properties: Compounds, including nitrides (e.g., titanium nitride, TiN) and carbides (e.g., silicon carbide, SiC), offer a combination of strength, durability, and specialized properties such as hardness or chemical resistance.
- Advantages: Compounds can be engineered to provide specific properties tailored to the application, such as enhanced wear resistance or improved thermal conductivity. They are often used in demanding environments where performance is critical.
- Disadvantages: The complexity of depositing compound films can be a challenge. Techniques like chemical vapor deposition (CVD) or atomic layer deposition (ALD) may be required, which can be expensive and time-consuming. Additionally, some compounds may be difficult to work with due to their reactivity or the need for precise control over deposition conditions.
-
Deposition Techniques:
- Physical Vapor Deposition (PVD): Techniques like sputtering and evaporation are commonly used for depositing metals and some compounds. PVD is favored for its ability to produce high-purity films with excellent adhesion.
- Chemical Vapor Deposition (CVD): CVD is often used for depositing oxides and compounds, particularly when precise control over film composition and thickness is required. However, CVD processes typically involve high temperatures and reactive gases, which can limit substrate choices.
- Atomic Layer Deposition (ALD): ALD is a highly controlled technique that allows for the deposition of ultra-thin, uniform films. It is particularly useful for depositing oxides and compounds where atomic-level precision is needed.
-
Selection Criteria for Substrates:
- Application Requirements: The choice of substrate is heavily influenced by the specific requirements of the application, such as electrical conductivity, thermal stability, mechanical strength, and chemical resistance.
- Cost Considerations: The cost of the substrate material and the deposition process must be balanced against the performance benefits. For example, while gold offers excellent conductivity, its high cost may make it unsuitable for large-scale applications.
- Compatibility with Deposition Techniques: The substrate must be compatible with the chosen deposition technique. For instance, high-temperature processes like CVD may not be suitable for substrates that cannot withstand elevated temperatures.
In conclusion, the selection of substrates for thin film deposition is a complex decision that involves balancing material properties, application requirements, and cost considerations. Metals, oxides, and compounds each offer unique advantages and challenges, and the choice of substrate will ultimately depend on the specific needs of the application. Understanding the properties and limitations of each material is essential for optimizing the performance and durability of thin film coatings.
Summary Table:
Substrate Type | Key Properties | Advantages | Disadvantages |
---|---|---|---|
Metals | Strength, durability, electrical conductivity | Strong, adherent films; easy deposition (e.g., sputtering) | High cost; potential oxidation/corrosion |
Oxides | High-temperature resistance, durability | Resistant to moisture/oxidation; excellent dielectric properties | Brittle; energy-intensive deposition |
Compounds | Strength, durability, specialized properties (e.g., hardness, chemical resistance) | Tailored properties for demanding environments | Expensive; complex deposition techniques (e.g., CVD, ALD) |
Need help selecting the right substrate for your thin film deposition? Contact our experts today to optimize your process!