Dental sintering furnaces are specialized equipment used in dentistry to sinter zirconia, a material commonly used for dental restorations like crowns and bridges. These furnaces operate at extremely high temperatures, typically ranging from 1200°C to 1400°C, which are necessary to achieve the final hardness and durability of zirconia. The sintering process transforms the zirconia from a porous, chalk-like state into a dense, strong material suitable for dental applications. The furnace's design ensures it can handle these high temperatures while maintaining precise control over the sintering environment, which is critical for consistent and reliable results.
Key Points Explained:
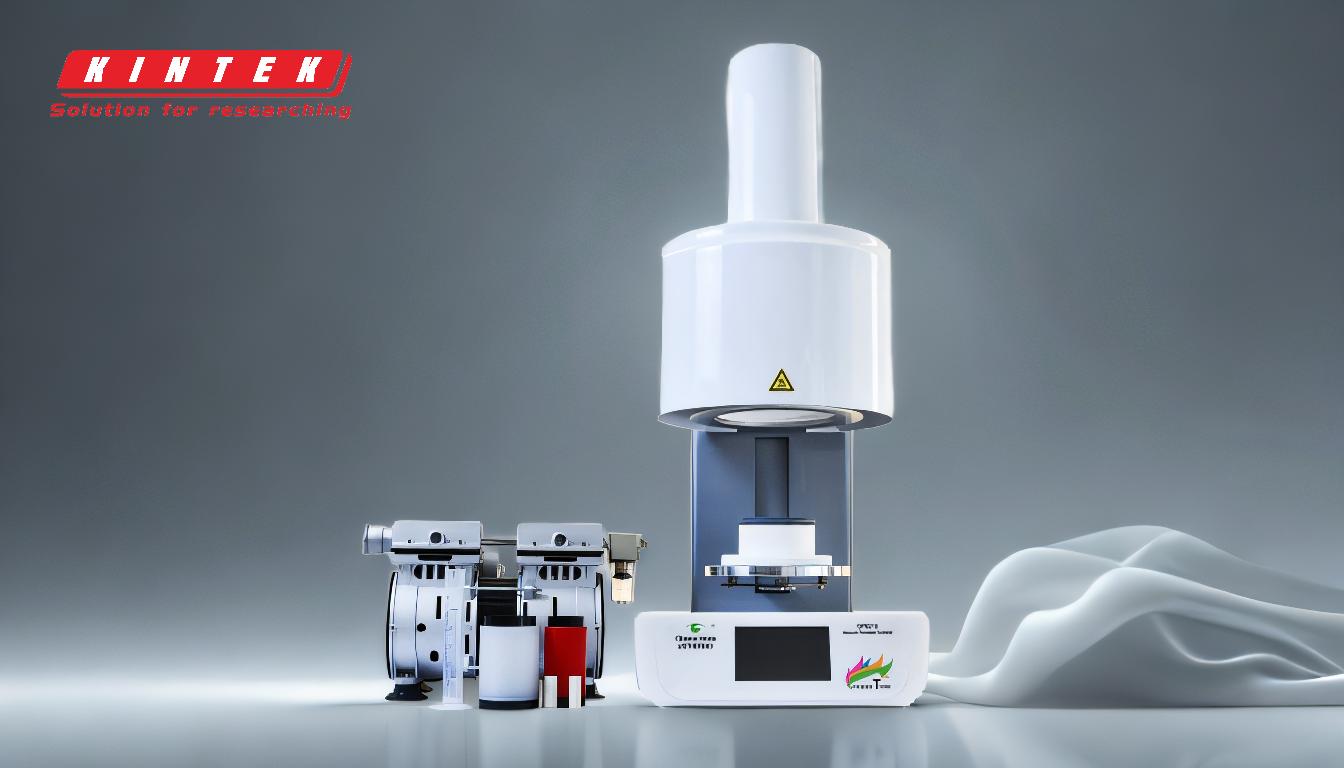
-
Temperature Range for Sintering:
- Dental sintering furnaces operate within a temperature range of 1200°C to 1400°C.
- This high temperature is essential for the sintering process, which involves heating zirconia to a point where its particles fuse together, resulting in a dense and durable material.
- The exact temperature may vary slightly depending on the specific zirconia material and the furnace's design, but the range of 1200°C to 1400°C is standard for most dental applications.
-
Purpose of High Temperatures:
- The primary purpose of these high temperatures is to sinter zirconia, transforming it from a porous, pre-sintered state into a fully dense and hard material.
- Sintering ensures the zirconia achieves the necessary mechanical properties, such as strength, toughness, and wear resistance, making it suitable for dental restorations.
- Without reaching these temperatures, the zirconia would remain brittle and unsuitable for clinical use.
-
Furnace Design and Environmental Considerations:
- Dental sintering furnaces are designed to operate in controlled indoor environments with ambient temperatures ranging from 2°C to 40°C and relative humidity up to 80% at 31°C.
- These environmental conditions ensure the furnace operates efficiently and safely, without overheating or malfunctioning due to external factors.
- The furnace can also function at altitudes up to 1500 meters, with specialized models available for higher altitudes up to 3500 meters.
-
Voltage and Electrical Requirements:
- The furnace requires a stable power supply, with rated voltage fluctuations not exceeding plus/minus 10% of the rated voltage.
- This ensures consistent performance and prevents damage to the furnace or interruptions during the sintering process.
-
Importance of Temperature Control:
- Precise temperature control is critical in dental sintering furnaces to ensure uniform sintering and avoid defects such as warping or cracking in the zirconia.
- Modern furnaces often include advanced features like programmable temperature profiles and real-time monitoring to maintain optimal sintering conditions.
-
Applications in Dentistry:
- Dental sintering furnaces are primarily used for fabricating zirconia-based dental restorations, such as crowns, bridges, and implants.
- The ability to reach and maintain high temperatures ensures that these restorations meet the stringent mechanical and aesthetic requirements of modern dentistry.
In summary, dental sintering furnaces operate at temperatures between 1200°C and 1400°C to sinter zirconia, transforming it into a durable material for dental restorations. The furnace's design and environmental controls ensure reliable performance, while precise temperature management guarantees high-quality results. These factors make dental sintering furnaces indispensable in modern dental laboratories.
Summary Table:
Key Aspect | Details |
---|---|
Temperature Range | 1200°C to 1400°C |
Purpose of High Temperatures | Sinter zirconia to achieve strength, toughness, and wear resistance. |
Environmental Conditions | Ambient: 2°C to 40°C, Humidity: ≤80% at 31°C, Altitude: Up to 1500m (3500m for specialized models). |
Voltage Requirements | Stable power supply with ±10% voltage fluctuation tolerance. |
Temperature Control | Precise control ensures uniform sintering and avoids defects. |
Applications | Used for zirconia crowns, bridges, and implants in modern dentistry. |
Ready to enhance your dental lab's capabilities? Contact us today to find the perfect sintering furnace for your needs!