Hydrogen annealing is a specialized heat treatment process conducted in a hydrogen atmosphere to remove hydrogen from materials, particularly metals like steel, to prevent hydrogen embrittlement. The process typically occurs at temperatures between 200 °C and 300 °C, as hydrogen atoms diffuse out of the material at these temperatures. This method is crucial after processes like welding, coating, or galvanizing, where hydrogen embrittlement can degrade mechanical properties. The hydrogen atmosphere also prevents oxidation and promotes surface cleaning, making it ideal for applications requiring bright, clean surfaces. However, precautions are necessary to avoid decarburization of steel parts.
Key Points Explained:
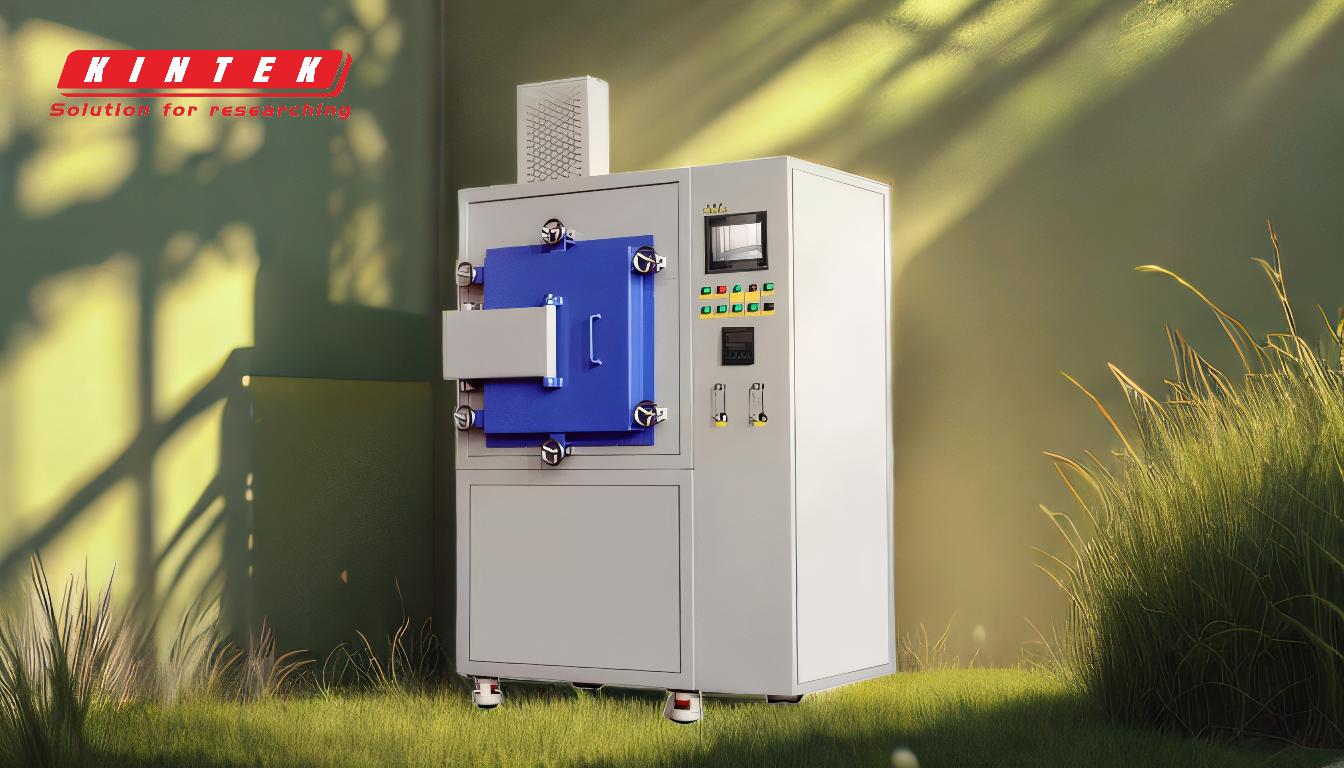
-
Temperature Range for Hydrogen Annealing:
- The process is conducted at 200 °C to 300 °C, which is the optimal range for hydrogen atoms to diffuse out of metals like iron and stainless steel.
- At 200 °C, hydrogen atoms begin to effuse from the material, which is the minimum temperature required for effective hydrogen removal.
- Higher temperatures within this range may enhance the diffusion rate but must be controlled to avoid adverse effects like decarburization.
-
Purpose of Hydrogen Annealing:
- The primary goal is to remove hydrogen from materials to prevent hydrogen embrittlement, a phenomenon where hydrogen atoms weaken the metal's mechanical properties, such as plasticity, ductility, and fracture toughness.
- It is particularly important after processes like welding, coating, or galvanizing, where hydrogen can be introduced into the material.
-
Hydrogen Atmosphere:
- The process uses a 100% hydrogen atmosphere to prevent oxidation and ensure a clean, bright surface finish, often referred to as bright annealing.
- Hydrogen acts as a reducing gas, cleaning oxidized surfaces by reducing oxides on the material.
- However, hydrogen can decarburize steel, so precautions are necessary to protect the material's integrity.
-
Mechanical Property Changes:
- Hydrogen annealing can alter the mechanical properties of materials. For example:
- In X80 pipeline steel, annealing at 200 °C for 12 hours increases yield strength by approximately 10% but reduces elongation by about 20%.
- This change is due to carbon atoms diffusing into interstitial sites of dislocations, forming a Cottrell atmosphere, which pins dislocations and reduces their mobility.
- Hydrogen annealing can alter the mechanical properties of materials. For example:
-
Limitations and Alternatives:
- While effective for internal hydrogen embrittlement, hydrogen annealing is less effective for hydrogen embrittlement caused by surface-absorbed hydrogen.
- The process is expensive due to the use of pure hydrogen. A cost-effective alternative is using nitrogen-hydrogen blends, which provide similar benefits at a lower cost.
-
Applications:
- Hydrogen annealing is commonly used in industries where hydrogen embrittlement is a concern, such as:
- Pipeline construction (e.g., X80 steel).
- Aerospace and automotive manufacturing, where high-strength materials are required.
- Electronics and wire production, where bright, clean surfaces are essential.
- Hydrogen annealing is commonly used in industries where hydrogen embrittlement is a concern, such as:
-
Process Duration:
- The material is typically held at the annealing temperature for several hours to ensure complete hydrogen removal.
- The exact duration depends on the material type, thickness, and the extent of hydrogen embrittlement.
By understanding these key points, equipment and consumable purchasers can make informed decisions about when and how to use hydrogen annealing to achieve desired material properties and prevent hydrogen-related failures.
Summary Table:
Aspect | Details |
---|---|
Temperature Range | 200 °C to 300 °C (optimal for hydrogen diffusion) |
Purpose | Removes hydrogen to prevent embrittlement; crucial post-welding/coating |
Atmosphere | 100% hydrogen for oxidation prevention and surface cleaning |
Mechanical Changes | Increases yield strength (10%) but reduces elongation (20%) in X80 steel |
Applications | Pipeline construction, aerospace, automotive, electronics, and wire production |
Process Duration | Several hours, depending on material type and thickness |
Limitations | Less effective for surface-absorbed hydrogen; expensive due to pure hydrogen use |
Alternative | Nitrogen-hydrogen blends for cost-effective results |
Discover how hydrogen annealing can improve your material properties—contact our experts today for more information!