Brazing is a versatile joining process that utilizes various heating sources to achieve the required temperature for melting the filler metal without melting the base materials. The choice of heating source depends on factors such as the materials being joined, the complexity of the assembly, production volume, and desired precision. Common heating methods include torch brazing, furnace brazing, induction brazing, dip brazing, resistance brazing, infrared brazing, and advanced methods like laser or electron beam brazing. Each method has unique advantages and is suited for specific applications, ensuring efficient and high-quality joints.
Key Points Explained:
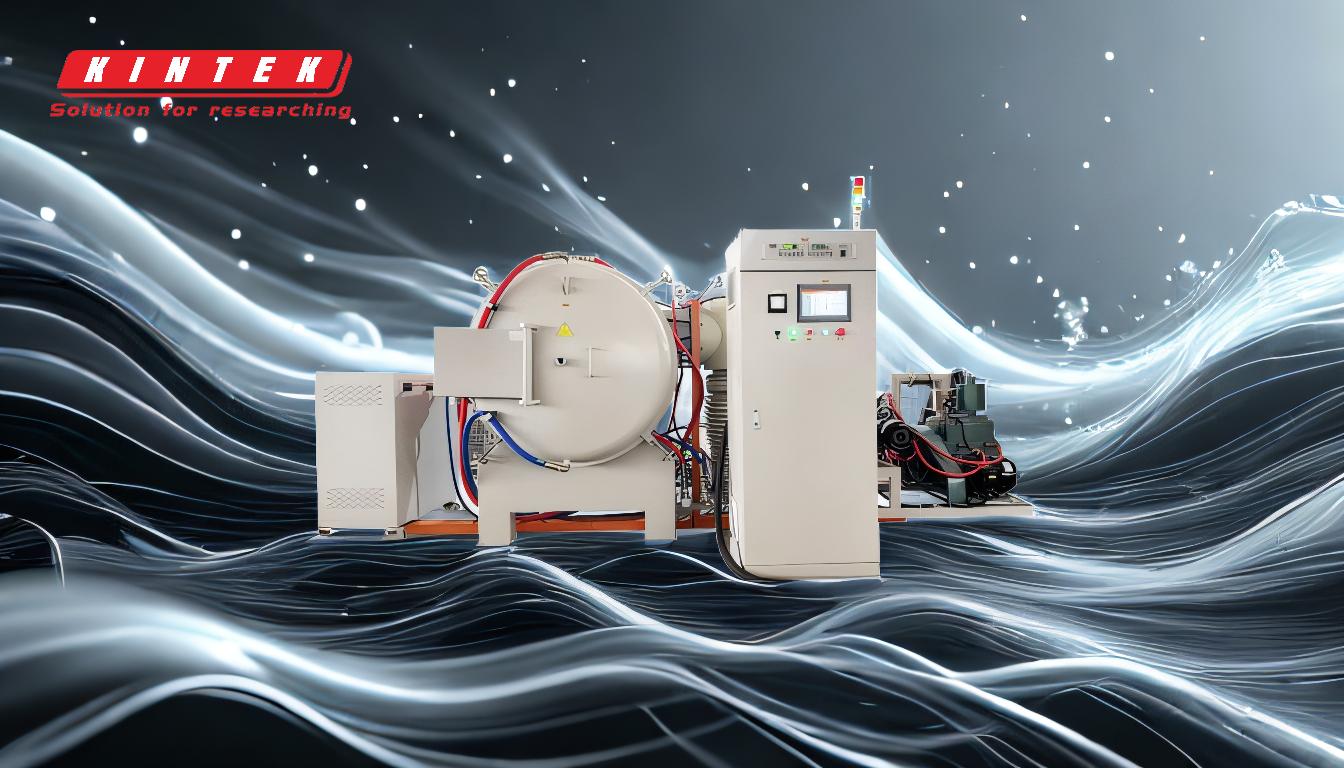
-
Torch Brazing:
- Description: Torch brazing uses a gas flame (typically oxy-acetylene or propane) to heat the joint area and melt the filler metal.
- Advantages: Portable, flexible, and suitable for small-scale or repair work.
- Applications: Commonly used for small assemblies, plumbing, and HVAC systems.
-
Furnace Brazing:
- Description: Furnace brazing involves heating the entire assembly in a controlled environment, such as a muffle furnace or vacuum furnace, to achieve uniform heating.
-
Types:
- Exothermic Atmosphere: Uses a gas mixture that reacts exothermically to provide heat.
- Hydrogen Atmosphere: Reduces oxides and prevents contamination.
- Argon Atmosphere: Inert gas prevents oxidation.
- Vacuum Atmosphere: Eliminates oxidation and contamination, ideal for sensitive materials.
- Advantages: High precision, repeatability, and suitability for large or complex assemblies.
- Applications: Aerospace, automotive, and electronics industries.
-
Induction Brazing:
- Description: Induction brazing uses electromagnetic induction to generate heat in the workpiece, localized to the joint area.
- Advantages: Fast, energy-efficient, and precise heating with minimal distortion.
- Applications: High-volume production, such as automotive components and electrical connections.
-
Dip Brazing:
- Description: The assembly is immersed in a molten salt or metal bath to heat the joint and melt the filler metal.
- Advantages: Uniform heating and protection from oxidation.
- Applications: Heat exchangers, radiators, and other assemblies requiring uniform heating.
-
Resistance Brazing:
- Description: Electrical resistance generates heat at the joint when current passes through the assembly.
- Advantages: Rapid heating and localized heat application.
- Applications: Electrical contacts, small components, and assemblies requiring precise heat control.
-
Infrared Brazing:
- Description: Infrared radiation is used to heat the joint area, often with a focused beam.
- Advantages: Non-contact heating with precise control.
- Applications: Small, delicate components and electronics.
-
Advanced Methods:
- Electron Beam Brazing: Uses a focused electron beam to heat the joint in a vacuum, ideal for high-precision applications.
- Laser Brazing: Employs a laser beam for localized heating, offering high precision and minimal heat-affected zones.
- Braze Welding: Combines brazing and welding techniques, using a filler metal with a lower melting point than the base material.
-
Material-Specific Considerations:
- Stainless Steel Brazing: Flame, induction, or furnace heating methods are commonly used, depending on the application and required precision.
Each heating method has its strengths and is chosen based on the specific requirements of the brazing process, ensuring optimal results for the materials and assemblies being joined.
Summary Table:
Heating Source | Advantages | Applications |
---|---|---|
Torch Brazing | Portable, flexible, suitable for small-scale or repair work | Small assemblies, plumbing, HVAC systems |
Furnace Brazing | High precision, repeatability, ideal for large or complex assemblies | Aerospace, automotive, electronics |
Induction Brazing | Fast, energy-efficient, precise heating with minimal distortion | Automotive components, electrical connections |
Dip Brazing | Uniform heating, protection from oxidation | Heat exchangers, radiators |
Resistance Brazing | Rapid heating, localized heat application | Electrical contacts, small components |
Infrared Brazing | Non-contact heating, precise control | Small, delicate components, electronics |
Advanced Methods | High precision, minimal heat-affected zones | Laser brazing for electronics, electron beam brazing for high-precision tasks |
Need help choosing the right brazing method for your project? Contact our experts today for personalized advice!