Vacuum coating is a widely used process in various industries to apply thin, protective, or functional layers to substrates. The most common materials used for vacuum coating, particularly in sputter coating, are noble metals like gold (Au) and gold-palladium blends, due to their resistance to oxidation and excellent conductivity. These materials are favored for their durability, biocompatibility, and ability to enhance the performance of substrates in applications ranging from medical tools to aerospace components. The versatility of vacuum coating allows it to be applied to metals like stainless steel, aluminum, and copper, as well as plastics, making it a crucial process in industries such as automotive, semiconductor production, and medical manufacturing.
Key Points Explained:
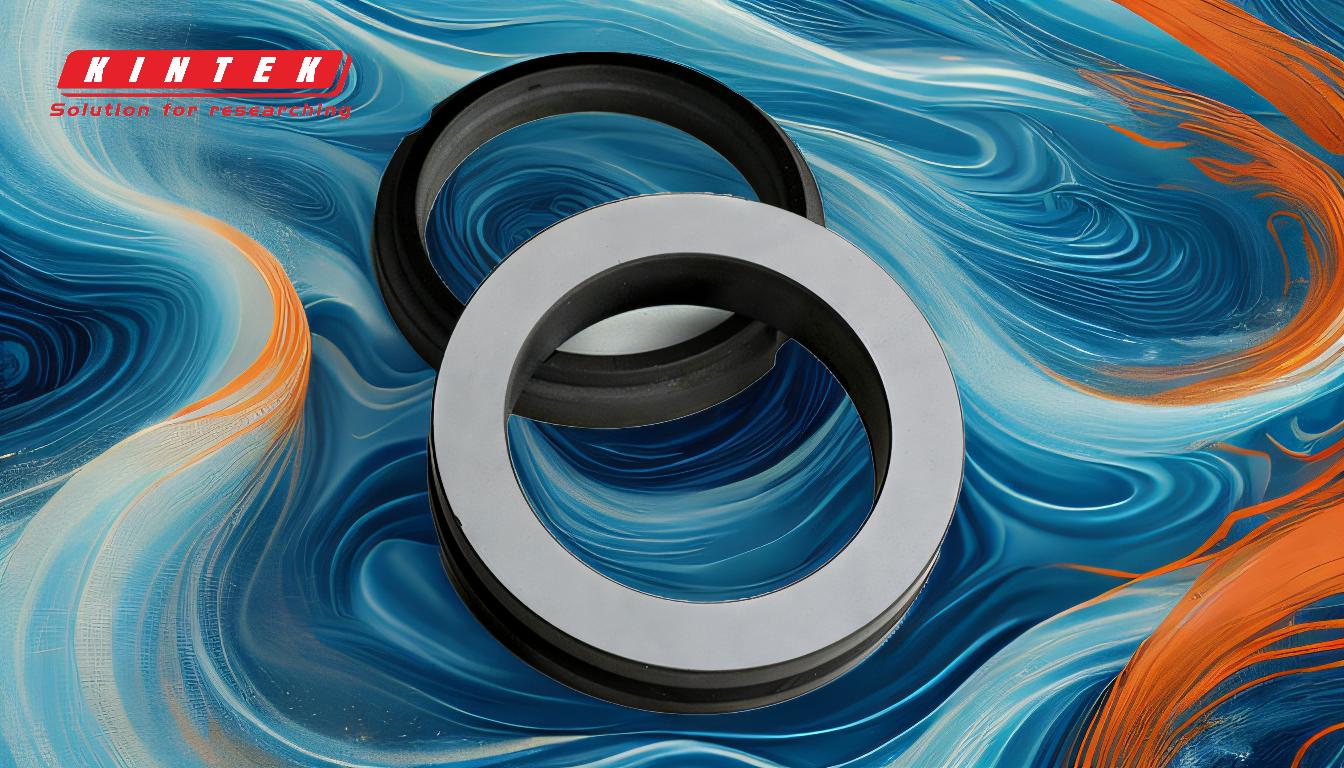
-
Most Common Vacuum Coated Materials:
- Noble Metals: Gold (Au) and gold-palladium blends are the most commonly used materials in vacuum coating, particularly in sputter coating. These materials are chosen because they do not oxidize easily, ensuring long-lasting performance and durability.
- Platinum Group Elements: Other noble metals from the platinum group are also used, especially in applications requiring high resistance to corrosion and wear.
-
Applications of Vacuum Coating:
- Industrial Applications: Vacuum coating is extensively used in industries such as aerospace, automotive, and medical manufacturing. For example, it is applied to carbon fiber composites in the automotive industry to enhance strength and durability.
- Functional Coatings: Vacuum coatings can provide various functional benefits, including corrosion protection, wear resistance, and biocompatibility. These characteristics are essential in medical tools and equipment, where safety and durability are critical.
- Decorative and Energy-Saving Coatings: Vacuum coating is also used for decorative purposes and energy-saving applications, such as low-emissivity glass, which helps in reducing energy consumption in buildings.
-
Substrates for Vacuum Coating:
- Metals: Vacuum coating can be applied to a wide range of metals, including stainless steel, aluminum, copper, and brass. These coatings enhance the properties of the metals, such as improving their resistance to wear and corrosion.
- Plastics: The process is also suitable for coating plastic parts, which is particularly useful in industries like injection molding and medical device manufacturing, where plastic components need to be protected or enhanced.
-
Characteristics of Vacuum Coatings:
- Protective Properties: Vacuum coatings provide excellent protection against wear, corrosion, and cold welding, making them ideal for harsh environments.
- Functional Enhancements: Depending on the application, vacuum coatings can offer non-stick effects, allergen reduction, and contour replication, which are beneficial in medical and industrial applications.
- Biocompatibility: In medical applications, vacuum coatings must be biocompatible to ensure they do not cause adverse reactions when in contact with human tissue.
-
Process and Thickness:
- Thin Film Deposition: Vacuum coating involves the application of a thin and steady layer of coating, typically ranging from 0.25 to 10 microns in thickness. This precise control over thickness is crucial for achieving the desired functional and protective properties.
- Versatility: The process can be tailored to meet specific application requirements, making it a versatile solution for a wide range of industries.
In summary, vacuum coating is a versatile and essential process used across multiple industries to enhance the performance and durability of various substrates. The most common materials used are noble metals like gold and gold-palladium blends, which offer excellent resistance to oxidation and wear. The process is applicable to both metals and plastics, providing a wide range of functional and protective benefits, making it indispensable in industries such as aerospace, automotive, and medical manufacturing.
Summary Table:
Aspect | Details |
---|---|
Common Materials | Gold (Au), gold-palladium blends, platinum group elements |
Applications | Aerospace, automotive, medical manufacturing, decorative, energy-saving |
Substrates | Metals (stainless steel, aluminum, copper) and plastics |
Characteristics | Corrosion resistance, wear resistance, biocompatibility, functional coatings |
Coating Thickness | 0.25 to 10 microns |
Enhance your products with advanced vacuum coating solutions—contact us today to learn more!