Heating elements break due to a combination of thermal, mechanical, and chemical factors. Repeated expansion and contraction from heating and cooling cycles cause mechanical stress, leading to wear and tear over time. Hot spots can form due to uneven heating or shielding, accelerating localized damage. Oxidation and intermittent operation cause the protective oxide layer to crack and flake, exposing the metal to further degradation. High temperatures can also lead to grain growth in alloys, making them brittle. Additionally, contamination and corrosion from environmental gases or fumes can weaken the element. Together, these factors contribute to the eventual failure of heating elements.
Key Points Explained:
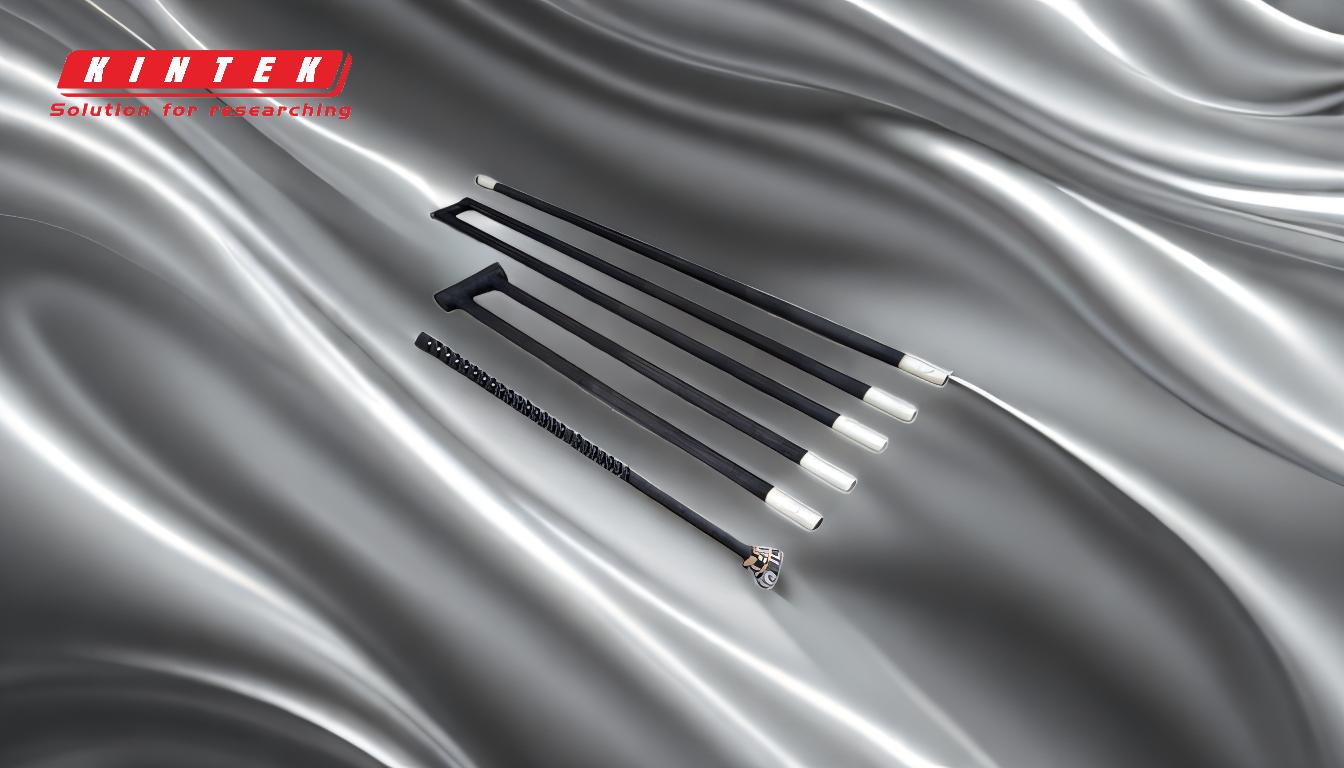
-
Thermal Expansion and Contraction
- Heating elements expand when heated and contract when cooled. This repeated cycle of expansion and contraction causes mechanical stress on the material.
- Over time, this stress leads to micro-cracks and structural weakening, eventually causing the element to break.
- This process is particularly pronounced in elements that undergo frequent heating and cooling cycles, such as those in ovens or furnaces.
-
Formation of Hot Spots
- Hot spots occur when certain areas of the heating element become significantly hotter than the rest due to uneven heat distribution or shielding by supports.
- These localized high temperatures accelerate oxidation and material degradation in the affected areas.
- Hot spots can also cause thermal runaway, where the temperature in the hotspot increases uncontrollably, leading to rapid failure.
-
Oxidation and Intermittent Operation
- Heating elements are often coated with a protective oxide layer that prevents further oxidation.
- Frequent heating and cooling cycles cause this oxide layer to crack and flake off, exposing fresh metal to oxidation.
- The loss of the protective layer accelerates material degradation, making the element more prone to failure.
-
Embrittlement Due to Grain Growth
- At high temperatures, the crystalline structure of the heating element material can change, leading to grain growth.
- In alloys containing iron, this results in the formation of large, brittle grains that are more susceptible to cracking.
- Embrittlement reduces the mechanical strength of the element, making it more likely to break under stress.
-
Contamination and Corrosion
- Heating elements operating in environments with gases or fumes can suffer from contamination.
- Contaminants react with the element material, causing dry corrosion and weakening the structure.
- Corrosion can also lead to the formation of pits or cracks, further compromising the element's integrity.
-
Overheating
- If a heating element overheats due to excessive current or insufficient cooling, it can cause rapid material degradation.
- Overheating accelerates oxidation, grain growth, and the formation of hot spots, all of which contribute to failure.
- In extreme cases, overheating can cause the element to melt or burn out completely.
By understanding these key factors, equipment and consumable purchasers can make informed decisions about selecting heating elements with materials and designs that minimize these failure mechanisms, ensuring longer operational lifespans and reduced maintenance costs.
Summary Table:
Factor | Description |
---|---|
Thermal Expansion | Repeated heating and cooling cycles cause stress, leading to cracks and weakening. |
Hot Spots | Uneven heating creates localized damage, accelerating oxidation and failure. |
Oxidation | Frequent cycles crack the protective oxide layer, exposing the metal to degradation. |
Grain Growth | High temperatures cause brittle grains, reducing mechanical strength. |
Contamination & Corrosion | Environmental gases or fumes weaken the element through corrosion. |
Overheating | Excessive heat accelerates oxidation, grain growth, and hot spots, leading to rapid failure. |
Need durable heating elements for your equipment? Contact us today to find the best solutions for your needs!