General Considerations for Magnetron Sputtering
Vacuum Environment Maintenance
Magnetron sputtering necessitates an impeccably maintained vacuum environment to avert the detrimental effects of airborne impurities on the film's quality. The vacuum environment is not merely a backdrop but a critical component that ensures the integrity and precision of the sputtering process.
In vacuum furnaces, the mechanical components, such as seals and braze joints, undergo rigorous maintenance to uphold the vacuum's leak-free status. This meticulous maintenance is essential because even minor leaks can compromise the vacuum levels, thereby affecting the end product's quality. The process of identifying and rectifying these leaks is both time-consuming and labor-intensive, underscoring the importance of preventive maintenance.
Moreover, contamination of furnace internals can arise from various sources, including residual gases and particulate matter, which can infiltrate the system during maintenance activities. Such contamination can lead to inconsistent film properties, necessitating thorough cleaning and validation protocols to ensure the vacuum environment remains pristine.
Maintenance Aspect | Importance |
---|---|
Seal Integrity | Ensures leak-free vacuum; critical for maintaining operational vacuum levels. |
Braze Joints | Require regular inspection and maintenance to prevent leaks. |
Furnace Internals | Must be kept free from contamination to maintain film quality. |
In summary, the vacuum environment's maintenance is a cornerstone of the magnetron sputtering process, demanding meticulous attention to detail and rigorous preventive measures to ensure the production of high-quality films.
Deposition Rate Control
The deposition rate is a critical parameter in the magnetron sputtering process, significantly influencing both the quality and thickness of the film. This rate dictates how quickly material from the target is transferred to the substrate, thereby affecting the uniformity, density, and final properties of the deposited film.
To achieve optimal results, the deposition rate must be meticulously controlled and adjusted according to specific conditions. Factors such as the type of target material, the desired film thickness, and the specific properties required for the application all play a role in determining the appropriate deposition rate. For instance, a higher deposition rate might be suitable for applications requiring thicker films, but it could also lead to issues like poor adhesion or non-uniformity if not managed correctly.
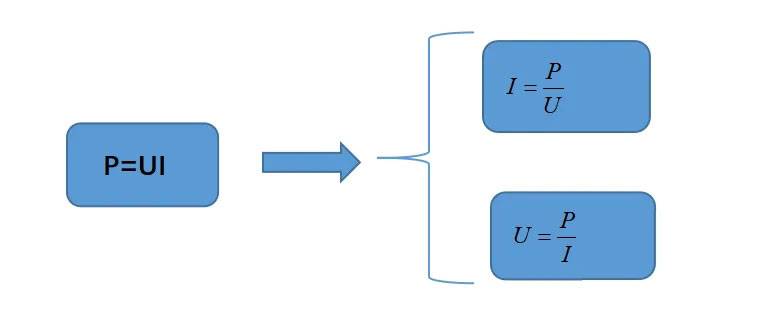
Factor | Impact on Deposition Rate |
---|---|
Target Material | Different materials have varying sputtering yields, affecting the rate at which they deposit. |
Substrate Temperature | Higher temperatures can enhance film adhesion but may also alter the deposition rate. |
Sputtering Power | Increased power typically results in a higher deposition rate, but must be balanced with other parameters. |
In summary, precise control over the deposition rate is essential for producing high-quality PZT films. This control ensures that the film not only meets the required thickness specifications but also exhibits the desired properties, such as electrical conductivity and mechanical strength.
Sputtering Power and Time Control
Sputtering power and time are critical parameters that significantly influence the quality of the film. These factors must be meticulously adjusted to align with the specific characteristics and requirements of the material being processed. The power level during sputtering affects the energy imparted to the target material, which in turn determines the rate at which atoms are ejected and deposited onto the substrate. Higher power levels generally result in faster deposition rates, but they can also lead to increased heat and stress on the substrate, potentially causing defects or altering the desired film properties.
Conversely, the duration of the sputtering process, or sputtering time, directly impacts the thickness and uniformity of the deposited film. Prolonged sputtering times can yield thicker films, but they also increase the risk of contamination and the likelihood of achieving non-uniform thickness across the substrate. Therefore, it is essential to balance sputtering power and time to achieve the optimal film quality.
To illustrate the importance of these parameters, consider the following table:
Sputtering Power (W) | Sputtering Time (min) | Film Thickness (nm) | Film Quality (Rating 1-10) |
---|---|---|---|
100 | 30 | 200 | 8 |
150 | 20 | 250 | 7 |
200 | 15 | 300 | 6 |
In this example, while higher power and shorter times result in thicker films, the film quality decreases due to increased stress and potential defects. Thus, the selection of appropriate sputtering power and time is a nuanced process that requires careful consideration of both the material properties and the desired film characteristics.
Target Material and Surface Preparation
Selection of Suitable Target Material
The selection of target material is a critical step in the magnetron sputtering process, significantly influencing the quality and performance of the resulting film. The choice of target material directly affects the chemical composition, structural integrity, and functional properties of the deposited film. Therefore, it is essential to select a target material that aligns with the specific requirements and desired outcomes of the film.
When choosing a target material, several factors must be considered:
-
Chemical Composition: The target material should match the desired chemical composition of the film. For instance, in the preparation of Lead Zirconate Titanate (PZT) films, the target should ideally consist of a homogeneous mixture of lead, zirconium, and titanium oxides.
-
Purity: High purity of the target material is crucial to avoid the introduction of impurities into the film, which can degrade its properties. Any contaminants can lead to defects, reduce the film's density, and affect its overall performance.
-
Physical Properties: The physical properties of the target, such as its density and thermal conductivity, can influence the sputtering process and the resulting film's characteristics. For example, a denser target material will typically result in a more uniform deposition rate.
-
Surface Condition: The surface of the target material must be smooth and free from defects to ensure efficient and uniform sputtering. Surface treatments may be necessary to achieve the required flatness and cleanliness.
The table below summarizes the key considerations for selecting a suitable target material:
Consideration | Importance |
---|---|
Chemical Composition | Ensures the desired chemical properties of the film. |
Purity | Prevents contamination and maintains film quality. |
Physical Properties | Influences sputtering efficiency and film uniformity. |
Surface Condition | Ensures efficient and uniform sputtering, avoiding defects in the film. |
In summary, the selection of the target material is a multifaceted decision that requires careful consideration of various factors to achieve high-quality and high-performance films.
Ensuring Purity and Flatness of Target Surface
The purity and flatness of the target surface are critical factors that significantly influence the sputtering process and the resultant film quality. Any impurities or irregularities on the target surface can lead to inconsistencies in the deposition of the PZT film, affecting its overall performance and uniformity.
To ensure optimal results, the target surface must undergo rigorous surface treatment and inspection protocols. This involves:
-
Surface Cleaning: Eliminating any contaminants such as dust, oils, or oxides that could compromise the purity of the target. Techniques like ultrasonic cleaning, chemical etching, and ion beam cleaning are commonly employed.
-
Flatness Inspection: Using advanced metrology tools such as profilometers and interferometers to measure the surface topography. Any deviations from the desired flatness must be corrected through polishing or other corrective measures.
Surface Treatment | Purpose | Common Techniques |
---|---|---|
Surface Cleaning | Remove contaminants | Ultrasonic cleaning, Chemical etching, Ion beam cleaning |
Flatness Inspection | Verify surface uniformity | Profilometers, Interferometers |
By meticulously adhering to these procedures, the purity and flatness of the target surface can be ensured, thereby enhancing the quality and consistency of the PZT film produced through magnetron sputtering.
Substrate and Environment Control
Control of Substrate Temperature
The substrate temperature plays a pivotal role in determining the final properties of the deposited film, such as crystallinity, density, and surface roughness. These properties are critical for the performance and functionality of the film, making precise temperature control an essential aspect of the magnetron sputtering process.
When the substrate temperature is too low, the film may exhibit poor crystallinity and low density, leading to increased surface roughness. Conversely, if the temperature is too high, it can cause undesirable phase changes or even thermal damage to the substrate. Therefore, the temperature must be meticulously adjusted based on the specific characteristics and requirements of the material being deposited.
For instance, in the case of Lead Zirconate Titanate (PZT) films, the optimal substrate temperature can vary significantly depending on the desired phase structure and ferroelectric properties. Typically, temperatures ranging from 400°C to 600°C are used to achieve the desired perovskite phase and optimal piezoelectric response.
To ensure precise control, modern sputtering systems often incorporate advanced temperature monitoring and control mechanisms, such as infrared thermometers and PID controllers. These tools allow for real-time adjustments, ensuring that the substrate temperature remains within the optimal range throughout the deposition process.
Temperature Range | Film Properties |
---|---|
< 400°C | Poor crystallinity, low density, high roughness |
400°C - 600°C | Desired perovskite phase, optimal piezoelectric response |
> 600°C | Possible phase changes, thermal damage |
In summary, the control of substrate temperature is a critical parameter in the magnetron sputtering process, directly influencing the quality and performance of the deposited film. Proper temperature management ensures that the film meets the required specifications and enhances its overall functionality.
Ensuring Vacuum and Atmosphere Control
The sputtering process for preparing Lead Zirconate Titanate (PZT) film layers is highly sensitive to environmental conditions. To achieve optimal results, it must be conducted in a meticulously controlled high vacuum environment. This stringent requirement is non-negotiable as it directly impacts the integrity and performance of the PZT film.
In a high vacuum environment, the absence of atmospheric gases significantly reduces the risk of contamination. Airborne particles, moisture, and other impurities can introduce defects into the film, compromising its structural and electrical properties. By maintaining a vacuum, these potential contaminants are effectively eliminated, ensuring a pristine deposition surface.
Moreover, the control of atmospheric conditions extends beyond mere vacuum maintenance. It also involves preventing oxidation, which can alter the chemical composition of the PZT film. Oxidation can lead to variations in the stoichiometry of the film, affecting its ferroelectric and piezoelectric properties. Therefore, maintaining a controlled atmosphere is crucial to preserving the desired chemical and physical characteristics of the PZT film.
To achieve and sustain this high vacuum environment, advanced vacuum systems are employed. These systems include high-efficiency pumps, leak detectors, and pressure sensors that work in tandem to maintain the required vacuum level. Regular monitoring and calibration of these systems are essential to ensure continuous and reliable vacuum control.
In summary, ensuring vacuum and atmosphere control is a critical aspect of the magnetron sputtering process for PZT film preparation. It not only safeguards against contamination and oxidation but also ensures the consistency and quality of the deposited film. This meticulous control is a cornerstone of the entire process, underpinning the successful fabrication of high-performance PZT films.
Uniformity Control
Uniformity is a critical property of thin films, particularly in the context of preparing Lead Zirconate Titanate (PZT) films via magnetron sputtering. Achieving uniform film deposition is essential for ensuring consistent performance and reliability across the entire substrate. This uniformity is primarily managed through meticulous control over the sputtering process, which involves several key parameters and techniques.
Firstly, the positioning and orientation of both the sputtering source and the substrate play a pivotal role in achieving uniform film deposition. The sputtering source, typically a target material, should be placed at an optimal distance from the substrate to ensure that the atoms or particles ejected from the target are evenly distributed across the surface. Additionally, the angle at which these particles travel to the substrate must be carefully controlled to prevent any directional bias in the deposition process.
Secondly, employing advanced techniques such as substrate rotation can significantly enhance uniformity. By rotating the substrate during the sputtering process, the film deposition becomes more evenly distributed, mitigating the effects of any localized variations in the sputtering source's output. This method ensures that every part of the substrate receives a consistent amount of material, leading to a more uniform final film.
Control Parameter | Impact on Uniformity |
---|---|
Sputtering Source Position | Ensures even distribution of particles |
Substrate Angle | Prevents directional bias in deposition |
Substrate Rotation | Enhances even distribution of material |
In summary, achieving uniformity in thin film deposition requires a combination of precise control over the sputtering source and substrate, as well as the strategic use of techniques like substrate rotation. These measures collectively contribute to the production of high-quality, uniform PZT films, which are essential for their intended applications.
Process Monitoring and Post-Treatment
Monitoring and Adjustment of Sputtering Power
Sputtering power is a critical parameter in the magnetron sputtering process, significantly influencing the thickness and composition of the deposited film. The power level directly affects the energy of the ions bombarding the target material, which in turn determines the rate at which material is ejected and deposited onto the substrate. For instance, higher sputtering power typically results in faster deposition rates but may also lead to increased film roughness and non-uniformity if not properly managed.
To ensure optimal film quality, it is essential to monitor and adjust the sputtering power dynamically. This involves using advanced monitoring systems that can provide real-time data on power levels, deposition rates, and film properties. By correlating these metrics, operators can fine-tune the sputtering power to achieve the desired film characteristics. For example, if the film thickness deviates from the target, the sputtering power can be adjusted to compensate, ensuring consistent layer thickness across the substrate.
Additionally, the composition of the film can be influenced by the sputtering power. Different power levels can cause varying degrees of sputtering from different elements within a multi-component target, leading to changes in the film's stoichiometry. Therefore, precise control of sputtering power is necessary to maintain the desired chemical composition of the film. This is particularly important in the preparation of complex oxide films like Lead Zirconate Titanate (PZT), where maintaining the correct ratio of lead, zirconium, and titanium is crucial for achieving the desired electrical and mechanical properties.
In summary, the monitoring and adjustment of sputtering power are not just about controlling the deposition rate but also about achieving the right balance of thickness, uniformity, and composition in the film. This dynamic control ensures that the final product meets the stringent requirements for applications in electronics, optics, and other high-tech fields.
Film Post-Treatment
Post-treatment processes are crucial steps in the preparation of Lead Zirconate Titanate (PZT) films, aimed at enhancing their properties and ensuring long-term stability. These treatments often include annealing and oxidizing, which are designed to refine the film's microstructure and improve its mechanical and electrical characteristics.
Annealing
Annealing involves heating the film to a specific temperature and then slowly cooling it. This process can:
- Enhance Crystallinity: By promoting the growth of larger, more uniform crystals, annealing can significantly improve the film's structural integrity.
- Reduce Stress: Internal stresses within the film can be alleviated, leading to a more stable and durable material.
- Improve Electrical Properties: The dielectric constant and ferroelectric properties of the film can be optimized through controlled annealing.
Oxidizing
Oxidizing the film involves exposing it to an oxygen-rich environment, which can:
- Stabilize the Oxide Layer: Ensuring that the film's surface oxide layer is uniform and stable can prevent issues such as delamination and degradation over time.
- Enhance Chemical Resistance: An oxidized surface is less susceptible to chemical attacks, making the film more robust in various environments.
- Control Surface Roughness: Oxidation can help to smooth out any irregularities on the film's surface, improving its overall quality and performance.
Both annealing and oxidizing are critical in post-treatment, as they not only address immediate quality concerns but also contribute to the film's long-term performance and reliability.
Quality Control and Testing
The prepared films undergo rigorous quality control and testing to ensure they meet the stringent requirements necessary for their intended applications. This process involves multiple facets, each meticulously assessed to guarantee the films' integrity and performance.
Key Parameters for Quality Control
-
Surface Morphology: The surface of the film is examined under high-resolution microscopes to detect any defects such as cracks, pinholes, or unevenness. This step is crucial as surface imperfections can significantly impact the film's functionality.
-
Thickness Measurement: The thickness of the film is measured using precision instruments like ellipsometers or profilometers. Consistency in thickness is essential for uniform electrical and mechanical properties across the film.
-
Composition Analysis: The chemical composition of the film is analyzed using techniques such as X-ray diffraction (XRD) and energy-dispersive X-ray spectroscopy (EDS). This ensures that the film's composition matches the desired stoichiometry, which is critical for its intended use.
-
Electrical Properties: Electrical tests, including resistivity, capacitance, and dielectric constant measurements, are performed to assess the film's performance in electrical applications. These properties are directly influenced by the film's structure and composition.
Testing Methods and Instruments
Parameter | Testing Method | Instrument Used |
---|---|---|
Surface Morphology | Microscopy | Scanning Electron Microscope (SEM) |
Thickness Measurement | Optical and Mechanical Techniques | Ellipsometer, Profilometer |
Composition Analysis | Spectroscopic Techniques | X-ray Diffraction (XRD), EDS |
Electrical Properties | Electrical Measurements | LCR Meter, Impedance Analyzer |
By systematically evaluating these parameters, the quality control process ensures that each film meets the predefined standards, thereby guaranteeing the reliability and performance of the final product.
Continuous Improvement and Environmental Considerations
Continuous Improvement and Optimization
Thin film preparation is an iterative process that demands continuous scrutiny and refinement to achieve optimal results. The preparation process, from the initial setup to the final product, requires meticulous analysis and improvement to enhance both the quality and efficiency of the film. This ongoing refinement involves several key aspects:
-
Process Parameters Monitoring: Regular monitoring and adjustment of critical parameters such as sputtering power, deposition rate, and substrate temperature are essential. These parameters significantly influence the film's properties, including its thickness, uniformity, and overall quality.
-
Technological Upgrades: Incorporating advanced technologies and methodologies can lead to substantial improvements. For instance, the use of automated systems for real-time monitoring and control can reduce human error and enhance process consistency.
-
Quality Control: Rigorous quality control measures are indispensable. This includes comprehensive testing of the film's surface morphology, thickness, composition, and electrical properties to ensure it meets the required standards.
-
Feedback Loops: Establishing effective feedback loops allows for the rapid identification and correction of any deviations from the desired outcomes. This iterative approach ensures that each cycle of film preparation is better than the last.
-
Environmental Considerations: While improving film quality, it is also crucial to consider the environmental impact of the preparation process. Adopting energy-efficient methods and minimizing waste can contribute to a more sustainable production cycle.
By continuously analyzing and refining these aspects, the preparation process can be optimized to yield high-quality films with improved efficiency and reduced environmental footprint.
Environmental Protection and Energy Consumption
In the quest for sustainable practices within the magnetron sputtering process, special emphasis must be placed on environmental protection and energy consumption. The traditional sputtering methods, while effective, often come with significant environmental and energy-related drawbacks. To mitigate these, adopting more environmentally friendly and energy-efficient preparation techniques is not just a recommendation but a necessity.
One approach to achieving this is through the optimization of the sputtering parameters. By fine-tuning factors such as sputtering power, deposition rate, and substrate temperature, it is possible to reduce the overall energy footprint of the process. For instance, lower sputtering powers can be employed without compromising the quality of the film, thereby conserving energy. Additionally, the use of advanced vacuum technologies can help in maintaining a cleaner environment by minimizing the release of harmful gases and particulates into the atmosphere.
Moreover, the selection of materials plays a crucial role in environmental sustainability. Opting for target materials that are less toxic and have a lower environmental impact can significantly enhance the eco-friendliness of the process. This not only protects the environment but also ensures compliance with increasingly stringent environmental regulations.
In summary, while the primary focus in magnetron sputtering is on the quality and performance of the PZT film, integrating environmental and energy considerations into the preparation process is equally important. This holistic approach ensures that the advancements in film technology are aligned with the broader goals of environmental stewardship and sustainability.
CONTACT US FOR A FREE CONSULTATION
KINTEK LAB SOLUTION's products and services have been recognized by customers around the world. Our staff will be happy to assist with any inquiry you might have. Contact us for a free consultation and talk to a product specialist to find the most suitable solution for your application needs!