Soldering or brazing stainless steel is indeed possible, but it requires careful consideration of the material type, the method used, and the specific conditions of the application. While most stainless steel types can be brazed, certain grades, such as those stabilized with titanium or niobium, may present challenges. Brazing can be performed using various heating methods, including flame, induction, or furnace heating, each with its own advantages and limitations. Understanding the nuances of the process is crucial for achieving strong, durable joints.
Key Points Explained:
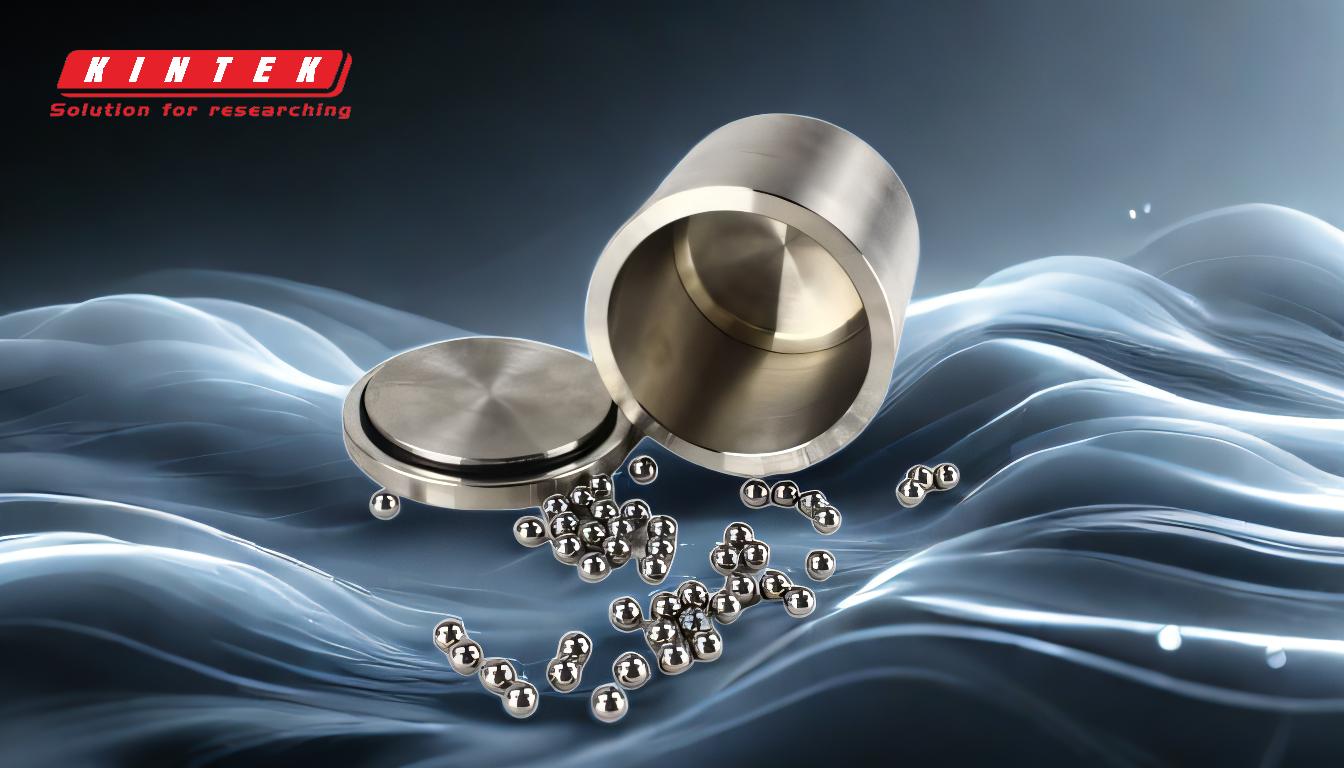
-
Brazing vs. Soldering Stainless Steel
- Brazing involves joining metals using a filler material with a melting point above 450°C (842°F), while soldering uses filler materials with lower melting points.
- Stainless steel is more commonly brazed than soldered due to its high strength and corrosion resistance, which aligns well with the properties of brazed joints.
- Soldering is typically reserved for less demanding applications or when lower temperatures are required.
-
Compatibility of Stainless Steel Grades
- Most stainless steel grades can be brazed, including austenitic, ferritic, and martensitic types.
- However, titanium or niobium-stabilized grades (e.g., 321 or 347 stainless steel) are exceptions due to their unique alloying elements, which can interfere with the brazing process.
- These stabilized grades are prone to carbide precipitation, which can weaken the joint and reduce corrosion resistance.
-
Brazing Methods for Stainless Steel
- Flame Brazing: Uses a gas torch to heat the joint and filler material. It is suitable for small-scale or manual operations.
- Induction Brazing: Employs electromagnetic induction to generate heat, offering precise temperature control and faster heating rates.
- Furnace Brazing: Involves heating the entire assembly in a controlled atmosphere furnace, ideal for complex or high-volume production.
- Each method has specific advantages, such as speed, precision, or scalability, depending on the application.
-
Filler Materials for Brazing Stainless Steel
- Common filler materials include silver-based alloys, nickel-based alloys, and copper-based alloys.
- Silver-based fillers are popular for their excellent flow characteristics and compatibility with stainless steel.
- Nickel-based fillers are preferred for high-temperature applications due to their strength and corrosion resistance.
- The choice of filler material depends on the operating environment, joint strength requirements, and cost considerations.
-
Surface Preparation and Flux Usage
- Proper surface preparation is critical for successful brazing. This includes cleaning the stainless steel to remove oxides, oils, and contaminants.
- Fluxes are often used to prevent oxidation during heating and to promote wetting of the filler material.
- For stainless steel, fluoride-based fluxes are commonly used due to their ability to dissolve chromium oxides, which can form on the surface.
-
Challenges and Considerations
- Stainless steel's low thermal conductivity can lead to uneven heating, requiring careful control of the brazing process.
- The formation of chromium carbides in certain grades can reduce corrosion resistance, necessitating the use of stabilized grades or post-braze heat treatment.
- Joint design and fit-up are crucial to ensure proper filler material flow and joint strength.
-
Applications of Brazed Stainless Steel
- Brazed stainless steel joints are widely used in industries such as automotive, aerospace, medical devices, and food processing.
- The high strength and corrosion resistance of brazed joints make them ideal for demanding environments.
- Examples include heat exchangers, piping systems, and precision components.
By understanding these key points, you can make informed decisions about whether to braze or solder stainless steel and how to approach the process effectively. Each step, from material selection to surface preparation and method choice, plays a vital role in achieving a successful and durable joint.
Summary Table:
Aspect | Details |
---|---|
Brazing vs. Soldering | Brazing uses filler with >450°C melting point; soldering for lower temps. |
Compatible Grades | Most grades can be brazed; titanium/niobium-stabilized grades are exceptions. |
Brazing Methods | Flame, induction, or furnace brazing, each with unique advantages. |
Filler Materials | Silver, nickel, or copper-based alloys, chosen based on application needs. |
Surface Preparation | Clean surfaces and use fluoride-based fluxes to prevent oxidation. |
Challenges | Uneven heating, carbide formation, and joint design are key considerations. |
Applications | Used in automotive, aerospace, medical devices, and food processing. |
Need expert advice on brazing or soldering stainless steel? Contact us today for tailored solutions!