Cleaning your furnace can significantly improve its efficiency, reduce energy consumption, and extend its lifespan. Regular maintenance, including cleaning the furnace chamber, blower, and ducts, ensures optimal performance by removing dust, impurities, and contaminants that can hinder heat transfer and airflow. This leads to better heating efficiency, lower electricity bills, and fewer repairs or replacements. Additionally, cleaning prevents safety hazards such as fires or explosions, making it a cost-effective and essential practice for homeowners.
Key Points Explained:
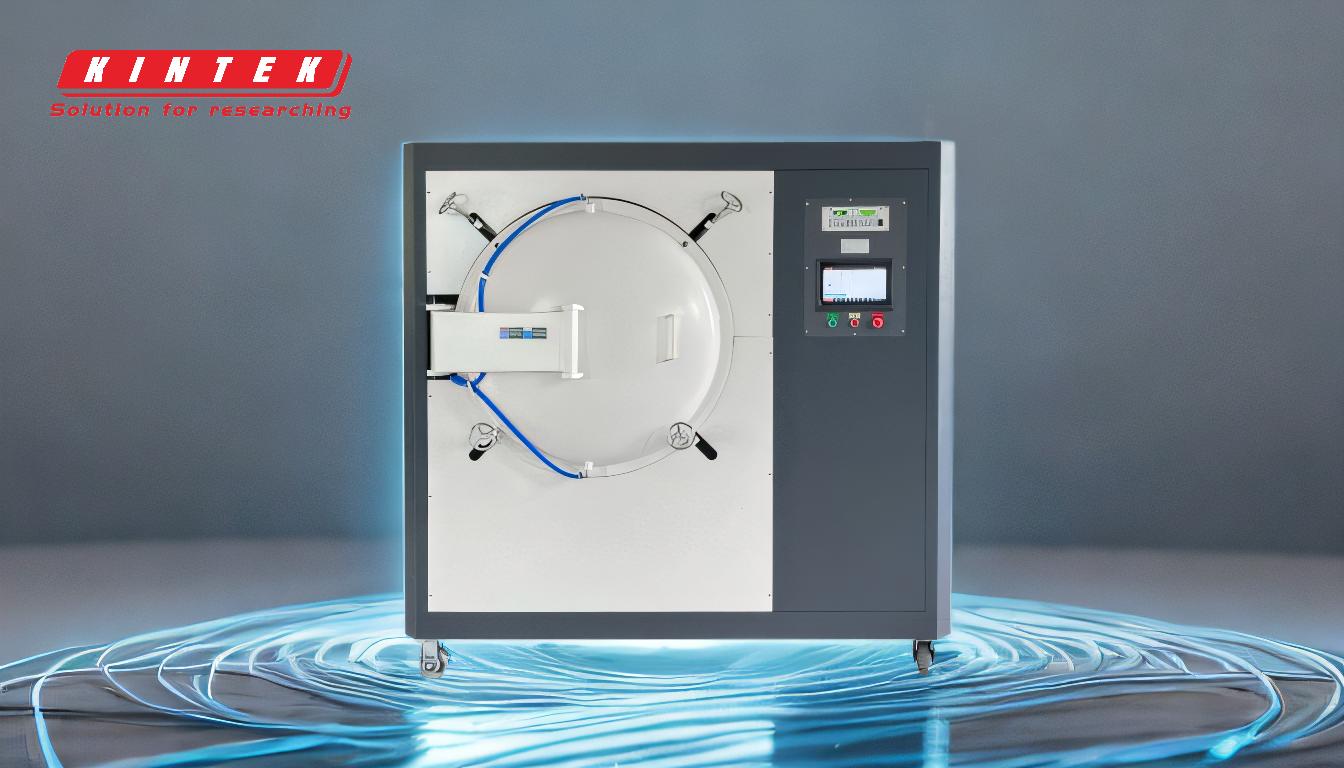
-
Improved Heating Efficiency
- Cleaning the furnace, including the boiler, ducts, and blower, ensures that heat is distributed more effectively throughout the home.
- Dust and debris can insulate components, making the furnace work harder and longer to achieve the desired temperature.
- A clean furnace operates at better rates, reducing runtime and energy consumption.
-
Energy Savings
- A clean furnace blower improves fan performance and motor efficiency, reducing electricity usage.
- Removing dust and contaminants from the furnace chamber and quartz tube enhances heat transfer, allowing the furnace to heat the home more efficiently.
- Lower energy consumption translates to reduced utility bills over time.
-
Extended Equipment Lifespan
- Regular cleaning removes residual impurities and contaminants that can degrade the furnace's components over time.
- A well-maintained furnace experiences less wear and tear, reducing the likelihood of costly repairs or replacements.
- Proper maintenance ensures the furnace operates optimally for years, saving money in the long run.
-
Prevention of Safety Hazards
- Dust buildup in the furnace can pose fire or explosion risks, especially in systems with high operating temperatures.
- Cleaning the furnace chamber and vacuum pump ensures safe operation by eliminating potential ignition sources.
- Regular maintenance minimizes the risk of accidents, protecting both the home and its occupants.
-
Cost Savings
- Cleaning the furnace blower and other components prevents the need for expensive repairs or replacements.
- Improved efficiency reduces the amount of fuel or electricity required to heat the home, lowering annual heating costs.
- Investing in regular maintenance is a cost-effective way to avoid unexpected expenses and maximize the furnace's performance.
-
Optimal Performance
- A clean furnace operates at peak performance, ensuring consistent and reliable heating.
- Removing contaminants from the quartz tube and furnace chamber prevents blockages and ensures efficient heat transfer.
- Regular cleaning maintains the furnace's efficiency, providing comfort and peace of mind during colder months.
By prioritizing furnace cleaning and maintenance, homeowners can enjoy a more efficient, cost-effective, and safer heating system. Regular upkeep not only enhances performance but also protects the investment in the furnace, ensuring it remains reliable for years to come.
Summary Table:
Benefit | Key Impact |
---|---|
Improved Heating Efficiency | Better heat distribution, reduced runtime, and lower energy consumption. |
Energy Savings | Lower electricity usage and reduced utility bills. |
Extended Equipment Lifespan | Fewer repairs, less wear and tear, and long-term cost savings. |
Prevention of Safety Hazards | Minimized fire or explosion risks, ensuring safe operation. |
Cost Savings | Avoids expensive repairs and lowers annual heating costs. |
Optimal Performance | Consistent and reliable heating for comfort and peace of mind. |
Ready to improve your furnace's performance? Contact us today for expert maintenance tips!