Strain hardening, also known as work hardening, is a process where a material becomes stronger and harder due to plastic deformation. This process affects the material's microstructure, particularly by increasing dislocation density. The relationship between strain hardening and conductivity is complex because conductivity is primarily influenced by the material's ability to allow the flow of electrons, which is affected by factors such as lattice imperfections, impurities, and dislocations. Strain hardening introduces more dislocations, which can scatter electrons and reduce conductivity. However, the extent of this effect depends on the material type, the degree of deformation, and other factors like temperature and purity. In general, strain hardening tends to reduce electrical conductivity, but the impact may vary depending on the specific material and conditions.
Key Points Explained:
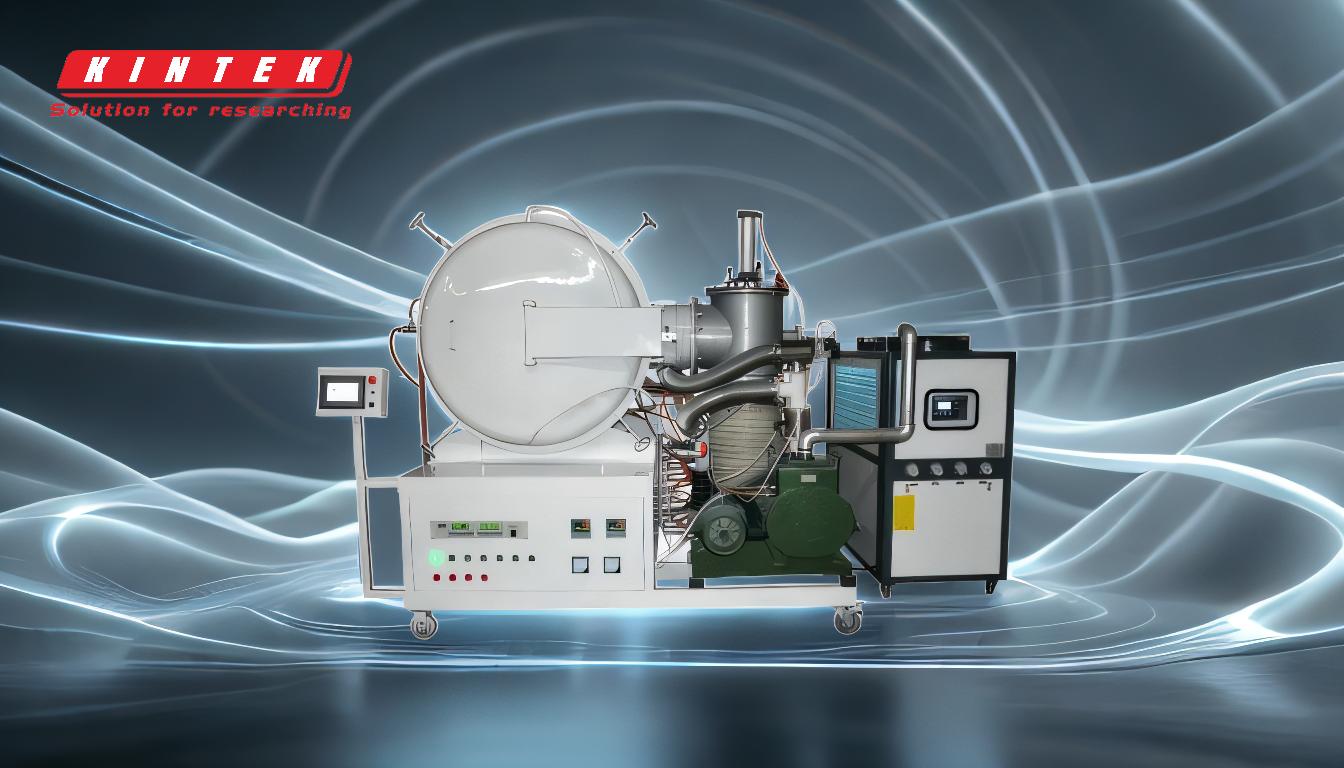
-
What is Strain Hardening?
- Strain hardening is the process by which a material becomes stronger and harder through plastic deformation. This occurs when dislocations in the crystal structure of the material interact and multiply, creating obstacles that make further deformation more difficult.
-
How Strain Hardening Affects Microstructure
- During strain hardening, the density of dislocations increases significantly. These dislocations disrupt the orderly arrangement of atoms in the crystal lattice, which can impede the movement of electrons. This disruption is a key factor in how strain hardening influences electrical conductivity.
-
Relationship Between Dislocations and Conductivity
- Electrical conductivity is determined by the ease with which electrons can move through a material. Dislocations act as scattering centers for electrons, reducing their mean free path and increasing electrical resistance. As strain hardening increases dislocation density, it generally leads to a decrease in conductivity.
-
Material-Specific Effects
- The impact of strain hardening on conductivity varies depending on the material. For example:
- In metals like copper and aluminum, which are highly conductive, strain hardening can noticeably reduce conductivity due to their reliance on a well-ordered lattice for electron flow.
- In alloys or materials with already high dislocation densities, the effect may be less pronounced because the baseline conductivity is already lower.
- The impact of strain hardening on conductivity varies depending on the material. For example:
-
Temperature and Purity Considerations
- Temperature can influence the relationship between strain hardening and conductivity. At higher temperatures, thermal vibrations may dominate over dislocation scattering, reducing the impact of strain hardening on conductivity.
- The purity of the material also plays a role. Impurities can introduce additional scattering centers, and in highly pure materials, the effect of strain hardening on conductivity may be more noticeable.
-
Practical Implications for Material Selection
- For applications where both strength and conductivity are critical (e.g., electrical wiring or connectors), understanding the trade-off between strain hardening and conductivity is essential. Materials may need to be annealed (heat-treated to reduce dislocation density) to restore conductivity after strain hardening.
-
Experimental Evidence
- Studies have shown that cold-working metals like copper and aluminum leads to a measurable decrease in electrical conductivity. This is consistent with the idea that increased dislocation density from strain hardening scatters electrons more effectively.
-
Conclusion
- Strain hardening generally reduces electrical conductivity due to the increased dislocation density, which scatters electrons and increases resistance. However, the extent of this effect depends on the material, degree of deformation, temperature, and purity. For applications requiring both mechanical strength and high conductivity, careful material processing and treatment are necessary to balance these properties.
Summary Table:
Aspect | Impact on Conductivity |
---|---|
Dislocation Density | Increases, leading to more electron scattering and reduced conductivity. |
Material Type | Highly conductive metals (e.g., copper, aluminum) show more noticeable conductivity loss. |
Temperature | Higher temperatures may reduce the impact of strain hardening on conductivity. |
Purity | Impurities and high purity levels can influence the extent of conductivity reduction. |
Practical Applications | Balancing strength and conductivity may require annealing or specialized processing. |
Need help understanding the effects of strain hardening on your materials? Contact our experts today for tailored solutions!