Sintered metal parts are manufactured through a series of well-defined steps that transform powdered metals into solid, durable components. The process typically involves powder preparation, compaction, and sintering, followed by optional post-treatment steps to enhance the final product's properties. By carefully selecting metal powders, applying precise compaction techniques, and controlling the sintering environment, manufacturers can produce parts with specific mechanical, thermal, and chemical properties. This method is widely used in industries such as automotive, aerospace, and electronics due to its ability to create complex shapes with high precision and material efficiency.
Key Points Explained:
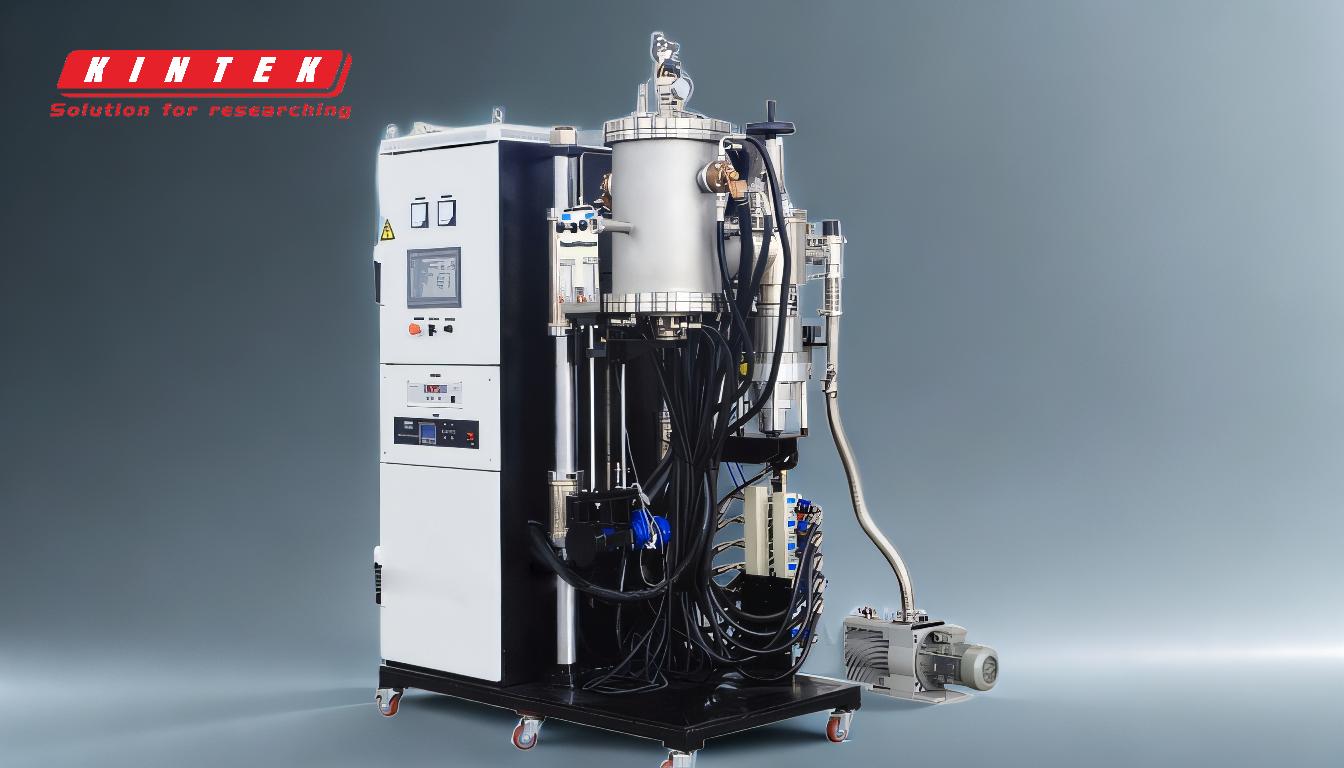
-
Powder Preparation
- Purpose: The first step involves creating or selecting the appropriate metal powder composition, which determines the final properties of the sintered part.
- Process: Metal powders, such as iron, nickel, molybdenum, or copper, are often blended with alloying elements, lubricants, or additives to achieve desired characteristics like strength, hardness, or corrosion resistance.
- Considerations: The particle size, shape, and distribution of the powder are critical, as they influence the compaction and sintering behavior.
-
Mixing and Blending
- Purpose: Ensures uniformity in the powder mixture, which is essential for consistent part properties.
- Process: Powders are mixed with additives like lubricants (e.g., wax or stearic acid) to improve flowability and reduce friction during compaction.
- Considerations: Proper blending prevents segregation of particles and ensures even distribution of alloying elements.
-
Compaction
- Purpose: Converts loose powder into a "green" part with a specific shape and initial strength.
- Process: The powder is pressed into a die or mold under high pressure (typically 20-50 tons per square inch) to form a coherent shape.
- Considerations: The compaction force must be carefully controlled to avoid defects like cracks or uneven density. Lubricants are often used to facilitate ejection from the die.
-
Sintering
- Purpose: Bonds the particles together to create a solid, durable part with optimal mechanical properties.
- Process: The green part is heated in a controlled atmosphere (e.g., hydrogen, nitrogen, or vacuum) to a temperature just below the melting point of the metal. This causes the particles to bond through diffusion, reducing porosity and increasing strength.
- Considerations: The sintering temperature, time, and atmosphere must be precisely controlled to achieve the desired density, hardness, and microstructure.
-
Post-Treatment
- Purpose: Enhances the properties of the sintered part to meet specific application requirements.
-
Process: Common post-treatment steps include:
- Machining: Precision machining with diamond tools or ultrasound to achieve tight tolerances.
- Heat Treatment: Processes like quenching and tempering to improve hardness and strength.
- Surface Treatment: Coatings or plating to enhance wear resistance or corrosion resistance.
- Assembly: Joining sintered parts with other components through brazing or metallization.
- Considerations: Post-treatment steps are tailored to the part's intended use, ensuring it meets performance standards.
-
Advantages of Sintered Metal Parts
- Material Efficiency: Minimal waste compared to traditional machining.
- Complex Shapes: Ability to produce intricate geometries that are difficult or impossible to achieve with other methods.
- Cost-Effectiveness: Lower production costs for high-volume manufacturing.
- Customizability: Tailored material properties through precise control of powder composition and processing parameters.
By following these steps, manufacturers can produce sintered metal parts with exceptional precision, durability, and performance, making them ideal for a wide range of industrial applications.
Summary Table:
Step | Purpose | Key Considerations |
---|---|---|
Powder Preparation | Select metal powder composition for desired properties | Particle size, shape, and distribution influence compaction and sintering. |
Mixing and Blending | Ensure uniformity in powder mixture for consistent part properties | Proper blending prevents segregation and ensures even distribution of additives. |
Compaction | Convert loose powder into a coherent shape with initial strength | Control compaction force to avoid defects like cracks or uneven density. |
Sintering | Bond particles to create a solid, durable part with optimal properties | Precise control of temperature, time, and atmosphere is critical. |
Post-Treatment | Enhance properties to meet specific application requirements | Includes machining, heat treatment, surface treatment, and assembly. |
Need custom sintered metal parts for your industry? Contact us today for expert solutions!