Annealing is a heat treatment process that significantly affects the hardness of materials, particularly metals. The process involves heating the material to a specific temperature, holding it at that temperature for a certain period, and then cooling it at a controlled rate. The primary effect of annealing is to soften the material, making it more ductile and less hard. This is achieved by reducing internal stresses, refining the grain structure, and allowing dislocations within the metal to rearrange themselves. The reduction in hardness is often desirable for materials that need to be machined, formed, or welded, as it improves workability. However, the extent to which annealing affects hardness depends on factors such as the material's composition, the annealing temperature, and the cooling rate.
Key Points Explained:
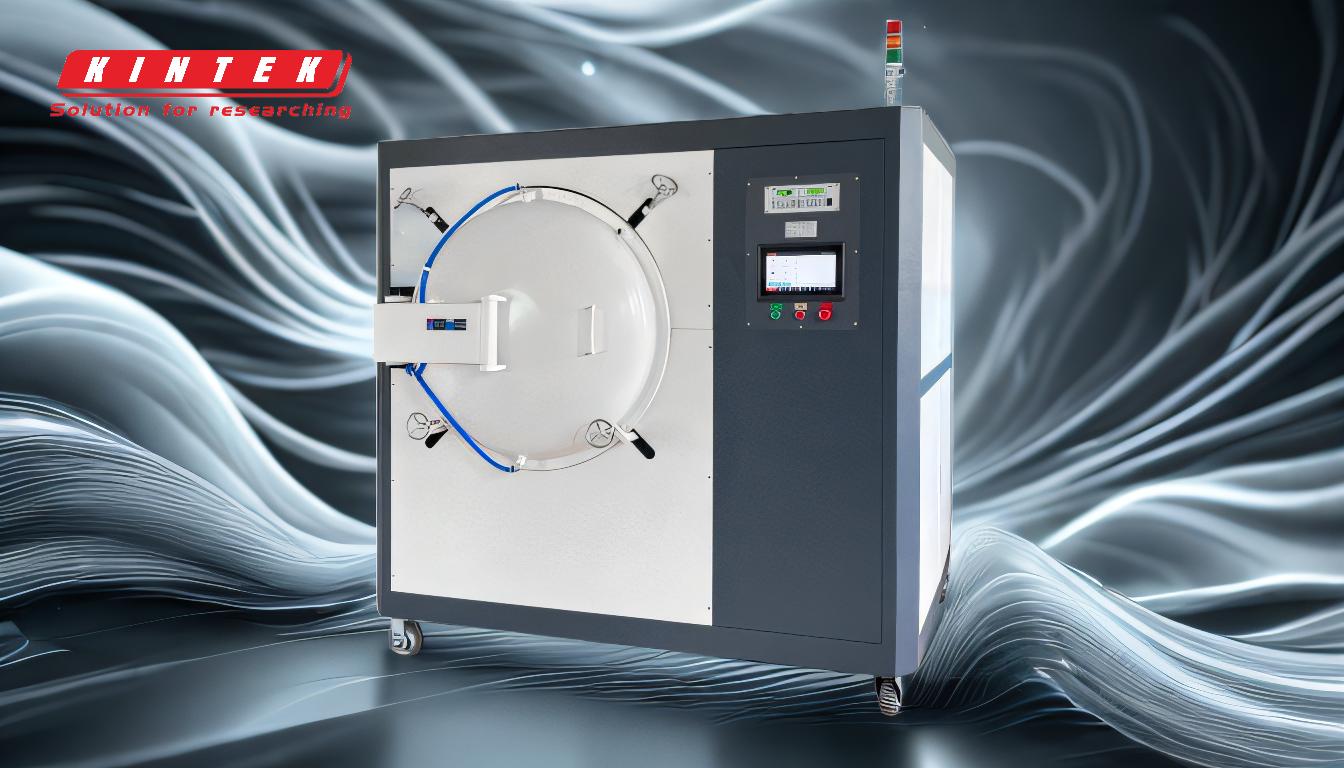
-
Mechanism of Annealing:
- Annealing works by heating the material to a temperature where its microstructure can change. This temperature is typically below the melting point but high enough to allow atoms to move and rearrange.
- During this process, dislocations (defects in the crystal structure) are reduced, and the grain structure becomes more uniform. This leads to a decrease in hardness and an increase in ductility.
-
Effect on Hardness:
- The primary effect of annealing is a reduction in hardness. This occurs because the process relieves internal stresses and allows the material to return to a more stable, less strained state.
- The reduction in hardness is beneficial for materials that need to be worked on, such as those undergoing machining, forming, or welding, as it makes them easier to shape and less prone to cracking.
-
Factors Influencing Annealing:
- Material Composition: Different materials respond differently to annealing. For example, steel, aluminum, and copper each have unique annealing temperatures and cooling rates that affect their final hardness.
- Annealing Temperature: The temperature at which annealing occurs plays a crucial role. If the temperature is too low, the material may not soften sufficiently. If it is too high, the material may become overly soft or even melt.
- Cooling Rate: The rate at which the material is cooled after annealing also affects hardness. Slow cooling generally results in a softer material, while rapid cooling can lead to increased hardness.
-
Applications of Annealing:
- Annealing is widely used in industries where materials need to be softened for further processing. For example, in the manufacturing of steel components, annealing is often used to prepare the material for machining or forming.
- It is also used in the production of wires, sheets, and other metal products where ductility and workability are essential.
-
Trade-offs:
- While annealing reduces hardness, it can also reduce strength and wear resistance. Therefore, it is essential to balance the need for softness with the material's required mechanical properties.
- In some cases, a secondary heat treatment process, such as tempering, may be used after annealing to achieve the desired balance of hardness and toughness.
-
Microstructural Changes:
- Annealing leads to significant changes in the material's microstructure. The grains become larger and more uniform, which reduces the number of grain boundaries. This change contributes to the material's increased ductility and decreased hardness.
- In some materials, such as steel, annealing can also lead to the formation of new phases, such as pearlite or ferrite, which further influence the material's mechanical properties.
In summary, annealing is a critical heat treatment process that reduces hardness by altering the material's microstructure. This softening effect is achieved through the relief of internal stresses, grain refinement, and dislocation rearrangement. The extent of hardness reduction depends on various factors, including material composition, annealing temperature, and cooling rate. While annealing is beneficial for improving workability, it is essential to consider the trade-offs in terms of strength and wear resistance.
Summary Table:
Aspect | Details |
---|---|
Primary Effect | Reduces hardness, increases ductility, and improves workability. |
Mechanism | Relieves internal stresses, refines grain structure, and rearranges dislocations. |
Key Factors | Material composition, annealing temperature, and cooling rate. |
Applications | Used in machining, forming, welding, and production of wires and sheets. |
Trade-offs | Reduced strength and wear resistance; may require secondary treatments. |
Microstructural Changes | Larger, more uniform grains; formation of new phases like pearlite or ferrite. |
Need help optimizing your material properties with annealing? Contact our experts today for tailored solutions!