Heat treatment is a critical process in metallurgy that significantly impacts the mechanical properties of metallic alloys. By controlling the rate of diffusion and cooling within the metal's microstructure, heat treatment can manipulate properties such as hardness, strength, toughness, ductility, and elasticity. This process allows engineers to tailor materials to specific applications, balancing trade-offs like strength and toughness. For instance, increasing hardness through case hardening or through hardening can enhance strength but may also introduce brittleness, necessitating tempering to restore ductility. Heat treatment techniques like annealing or re-tempering can also make overly brittle materials more usable by improving their ductility.
Key Points Explained:
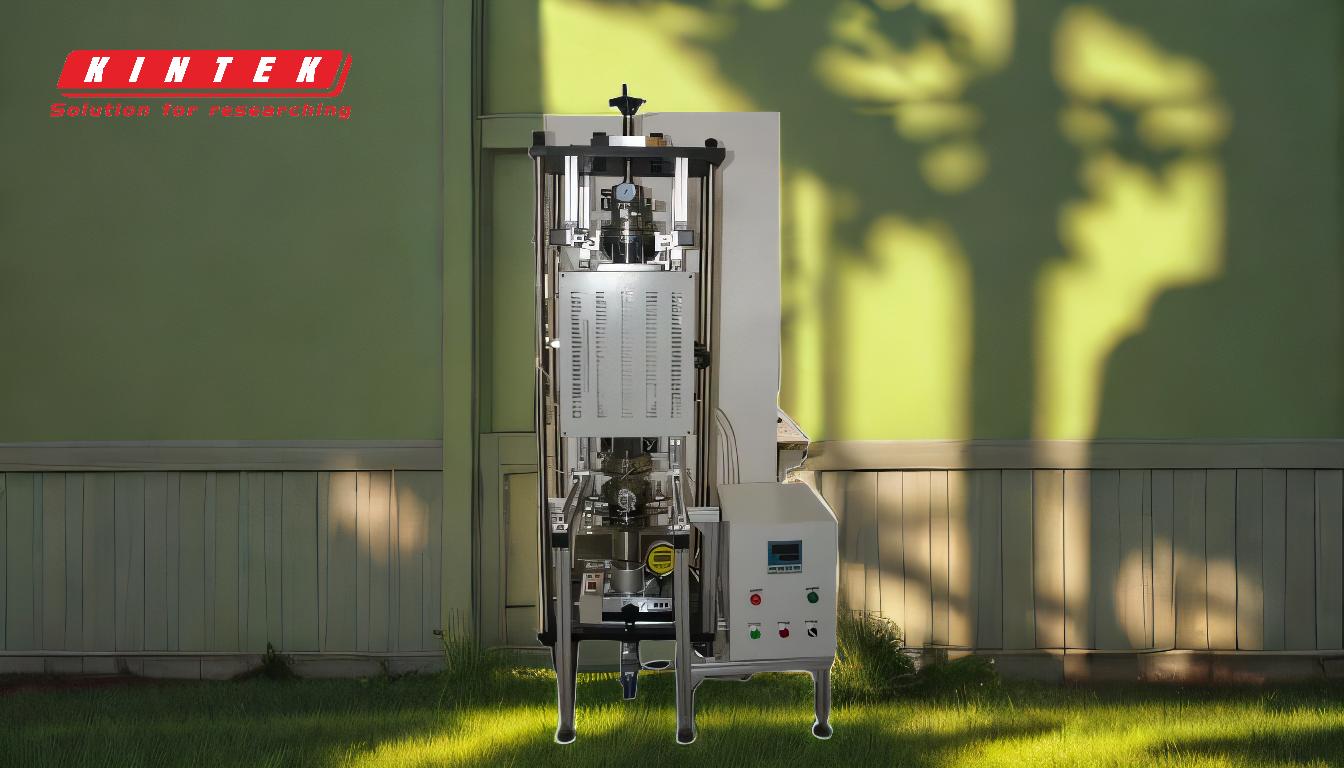
-
Manipulation of Mechanical Properties
- Heat treatment alters key mechanical properties of metallic alloys, including hardness, strength, toughness, ductility, and elasticity.
- These changes are achieved by controlling the rate of diffusion and cooling, which influence the metal's microstructure.
- For example, rapid cooling (quenching) can increase hardness and strength but may reduce toughness, while slow cooling (annealing) can enhance ductility and reduce internal stresses.
-
Trade-Off Between Strength and Toughness
- Strength and toughness are often inversely related; increasing one may reduce the other.
- Heat treatment processes like case hardening or through hardening increase strength but can introduce brittleness.
- Tempering is used to reduce brittleness and restore toughness, balancing the material's properties for specific applications.
- The degree of tempering is determined by the desired ultimate strength of the material.
-
Case Hardening and Through Hardening
- Case hardening increases the hardness of the material's surface while maintaining a tougher core, ideal for wear-resistant applications.
- Through hardening increases hardness throughout the material, making it suitable for applications requiring uniform strength.
- Both methods require tempering to mitigate brittleness and improve toughness.
-
Annealing and Re-Tempering
- Annealing involves heating the material to a specific temperature and then slowly cooling it to improve ductility and reduce internal stresses.
- Re-tempering is used to adjust the material's properties if it is too brittle as received, making it more usable for manufacturing processes.
- These processes are essential for materials that require a balance of strength and ductility.
-
Applications of Heat Treatment
- Heat treatment is widely used in industries such as automotive, aerospace, and construction to enhance material performance.
- For example, gears and shafts are often case hardened to withstand wear, while structural components may be tempered to achieve a balance of strength and toughness.
- The ability to tailor material properties through heat treatment makes it indispensable in modern engineering.
By understanding these key points, equipment and consumable purchasers can make informed decisions about material selection and heat treatment processes to meet specific application requirements.
Summary Table:
Key Aspect | Description |
---|---|
Mechanical Properties | Alters hardness, strength, toughness, ductility, and elasticity via microstructure control. |
Strength vs. Toughness | Trade-off managed through tempering to balance brittleness and toughness. |
Case Hardening | Increases surface hardness for wear resistance while maintaining a tough core. |
Through Hardening | Uniform hardness throughout the material, ideal for strength-focused applications. |
Annealing | Improves ductility and reduces internal stresses via slow cooling. |
Applications | Used in automotive, aerospace, and construction for enhanced material performance. |
Optimize your material performance with expert heat treatment solutions—contact us today!