Electric furnaces can reach extremely high temperatures, with industrial electric arc furnaces capable of reaching up to 1,800 °C (3,300 °F) and laboratory units exceeding 3,000 °C (5,400 °F). Preheating furnaces, depending on the model, can achieve maximum temperatures of around 1,200 °C. The ability to achieve such high temperatures makes electric furnaces suitable for a wide range of applications, from industrial metal processing to advanced laboratory research. Additionally, electric furnaces offer several advantages, including widespread availability of electricity, lower initial costs, enhanced safety by eliminating harmful byproducts, and high efficiency due to the absence of flues or chimneys.
Key Points Explained:
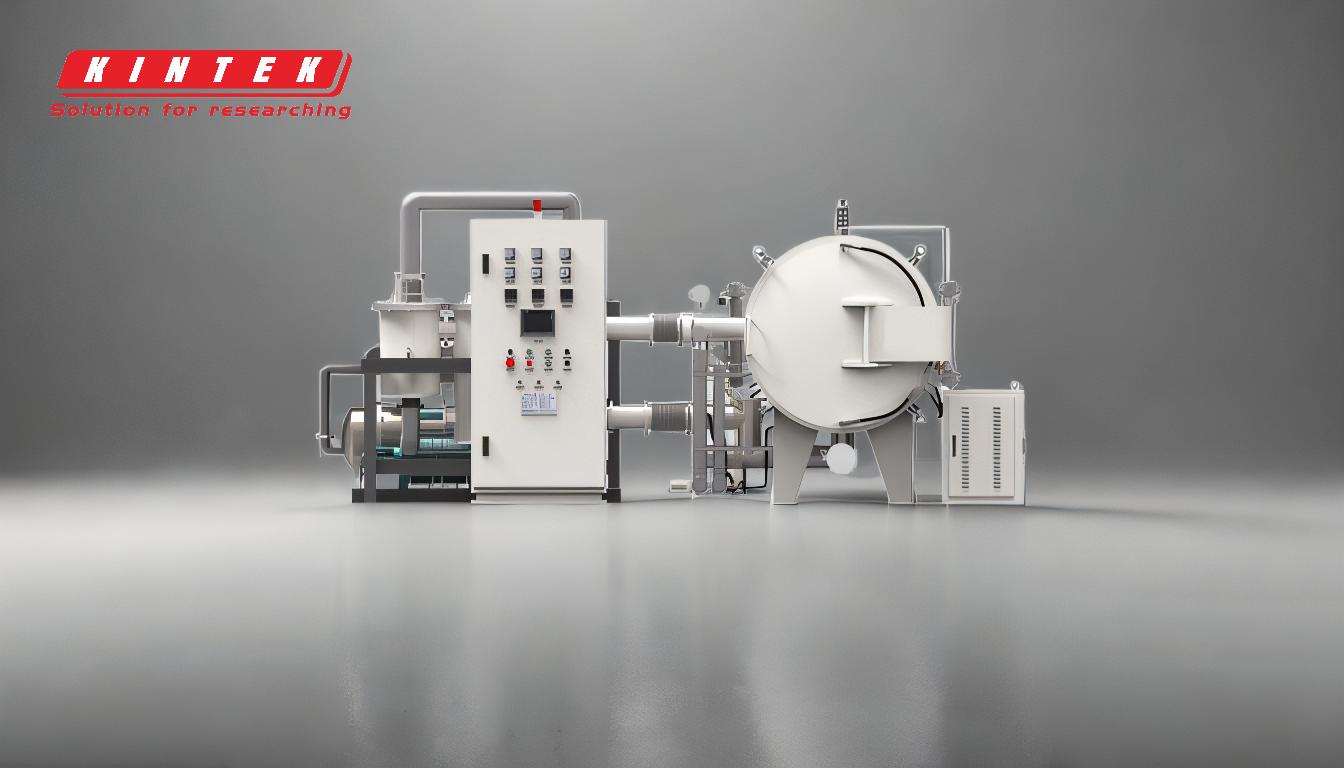
-
Temperature Capabilities of Electric Furnaces
- Industrial Electric Arc Furnaces: These furnaces can reach temperatures up to 1,800 °C (3,300 °F). They are commonly used in industries for melting metals and alloys, making them essential for steel production and other high-temperature processes.
- Laboratory Electric Furnaces: Designed for more specialized applications, laboratory units can exceed 3,000 °C (5,400 °F). These high temperatures are crucial for advanced material research, including the development of ceramics, composites, and other high-performance materials.
- Preheating Furnaces: These furnaces typically reach maximum temperatures of around 1,200 °C. They are used in various industrial processes, such as preheating materials before further processing or treatment.
-
Factors Influencing Temperature Range
- Design and Construction: The materials used in the construction of the furnace, such as refractory linings and heating elements, play a significant role in determining the maximum temperature it can achieve.
- Power Supply: The electrical power supply must be sufficient to generate the required heat. Higher temperatures generally require more power.
- Control Systems: Advanced temperature control systems are necessary to maintain and regulate the high temperatures, ensuring consistent performance and safety.
-
Advantages of Electric Furnaces
- Availability: Electricity is widely accessible, making electric furnaces a convenient option in most locations. This contrasts with other heating sources like gas, which may not be as readily available.
- Reduced Initial Cost: Electric furnaces are generally cheaper to purchase and install compared to other types of furnaces. Their widespread use and standardized components contribute to lower costs.
- Safety: Electric furnaces eliminate the risk of harmful byproducts such as carbon monoxide, which can be produced by gas or oil furnaces. This makes them safer to operate, especially in enclosed spaces.
- Efficiency: Electric heating is highly efficient because it directly converts electrical energy into heat without the need for flues or chimneys to expel smoke or gases. This results in less energy waste and lower operational costs.
-
Applications of High-Temperature Electric Furnaces
- Industrial Applications: In industries such as steel production, electric arc furnaces are used to melt scrap metal and produce new steel. The high temperatures ensure that the metal is fully melted and impurities are removed.
- Laboratory Research: High-temperature electric furnaces are essential in research laboratories for developing new materials and conducting experiments that require extreme heat. This includes the synthesis of advanced ceramics, nanomaterials, and high-temperature alloys.
- Preheating Processes: Preheating furnaces are used in various manufacturing processes to prepare materials for further treatment, such as forging, rolling, or heat treatment. The controlled high temperatures ensure that the materials are uniformly heated, improving the quality of the final product.
-
Considerations for Purchasing an Electric Furnace
- Temperature Requirements: Determine the maximum temperature needed for your specific application. This will help you choose between industrial, laboratory, or preheating furnaces.
- Power Supply: Ensure that your facility has the necessary electrical infrastructure to support the furnace. High-temperature furnaces, especially laboratory units, may require significant power.
- Safety Features: Look for furnaces with advanced safety features, such as automatic shut-off systems and temperature monitoring, to prevent overheating and ensure safe operation.
- Efficiency and Cost: Consider the long-term operational costs, including energy consumption and maintenance. While electric furnaces are generally efficient, the specific design and features can impact overall cost-effectiveness.
In summary, electric furnaces are capable of reaching extremely high temperatures, making them suitable for a wide range of industrial and laboratory applications. Their advantages, including availability, safety, and efficiency, make them a preferred choice for many users. When purchasing an electric furnace, it is important to consider factors such as temperature requirements, power supply, safety features, and overall cost to ensure that the furnace meets your specific needs.
Summary Table:
Feature | Details |
---|---|
Industrial Arc Furnaces | Up to 1,800 °C (3,300 °F) for melting metals and steel production. |
Lab Furnaces | Exceed 3,000 °C (5,400 °F) for advanced material research. |
Preheating Furnaces | Up to 1,200 °C for industrial preheating processes. |
Advantages | Widespread electricity, low cost, enhanced safety, and high efficiency. |
Applications | Steel production, material research, and preheating for manufacturing. |
Ready to find the perfect electric furnace for your needs? Contact our experts today for personalized advice!