Conventional heating and induction heating are fundamentally different in their mechanisms, efficiency, and applications. Conventional heating methods, such as gas or electric furnaces, rely on external heat sources like flames or heating elements to transfer heat to the material through convection and radiation. In contrast, induction heating generates heat directly within the material using electromagnetic induction, eliminating the need for direct contact with a heat source. This results in higher energy efficiency, faster heating times, and greater precision in temperature control. Induction heating is particularly advantageous in industrial applications where consistent, repeatable, and automated heating processes are required.
Key Points Explained:
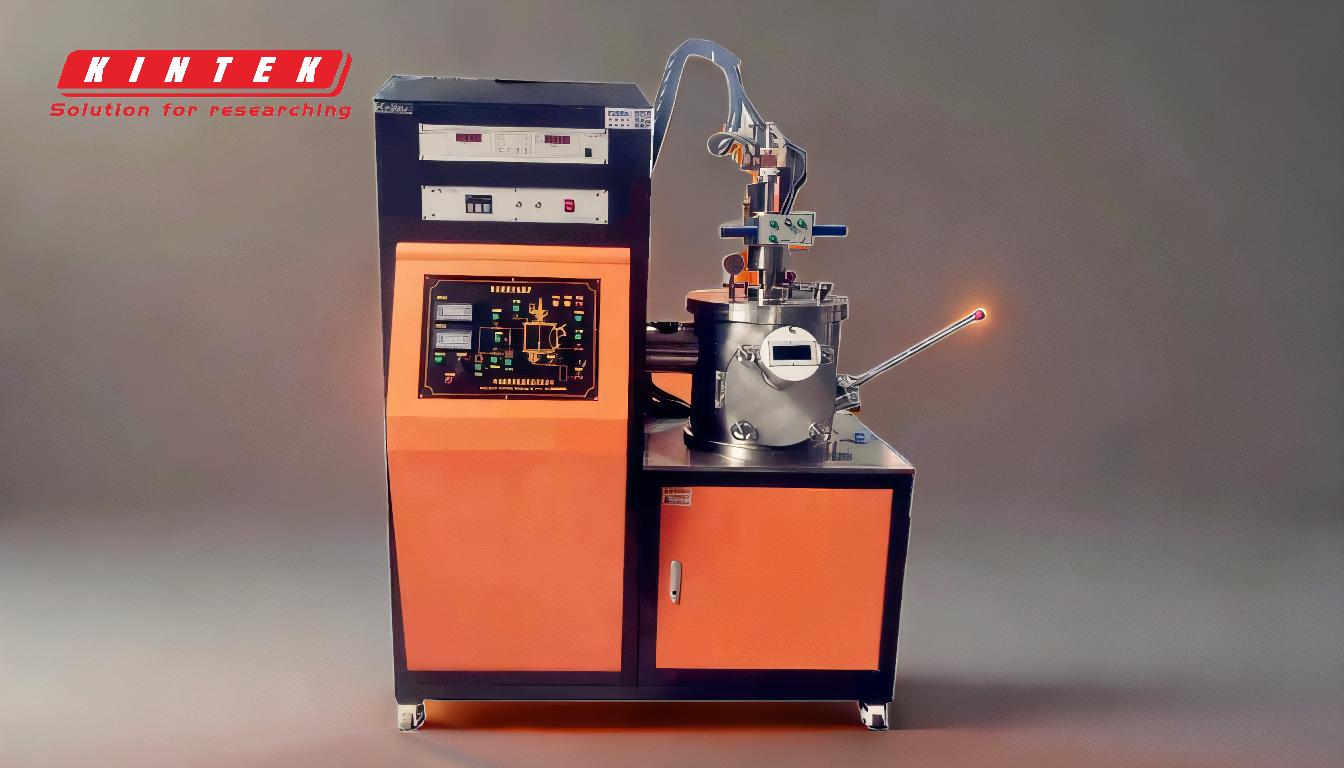
-
Mechanism of Heat Generation:
- Conventional Heating: Heat is generated externally using sources like flames (gas furnaces) or heating elements (electric furnaces). The heat is then transferred to the material through convection and radiation. This process often involves direct contact between the heat source and the material.
- Induction Heating: Heat is generated internally within the material through electromagnetic induction. An alternating current passes through a coil, creating a magnetic field that induces eddy currents in the conductive material. These currents generate heat directly within the material, without any direct contact with an external heat source.
-
Energy Efficiency:
- Conventional Heating: Typically less efficient, with gas-fired furnaces achieving around 20% efficiency. A significant amount of energy is lost during heat transfer through convection and radiation.
- Induction Heating: Highly efficient, with some systems achieving up to 92% efficiency. Since heat is generated directly within the material, energy losses are minimized, making it a more sustainable option.
-
Heating Speed and Control:
- Conventional Heating: Slower heating process due to the time required for heat transfer from the external source to the material. Temperature control can be less precise, leading to potential inconsistencies.
- Induction Heating: Faster heating process because heat is generated directly within the material. Offers precise control over heating power and temperature, enabling consistent and repeatable results. This is particularly beneficial for industrial processes requiring high-quality end products.
-
Safety and Cleanliness:
- Conventional Heating: Involves open flames or heating elements, which can pose safety risks and require careful handling. The use of fuel substances can also lead to contamination and require additional cleaning processes.
- Induction Heating: Contactless heating eliminates the need for open flames or fuel substances, improving safety and cleanliness. This reduces the risk of contamination and makes the process more environmentally friendly.
-
Applications and Automation:
- Conventional Heating: Suitable for a wide range of applications but may not be ideal for processes requiring high precision or automation. The reliance on external heat sources can limit the ability to integrate with automated systems.
- Induction Heating: Ideal for industrial applications where precision, repeatability, and automation are critical. The ability to control heating power and temperature with high accuracy makes it suitable for processes like induction melting, heat treatment, and brazing.
-
Depth of Heating:
- Conventional Heating: Heat is applied uniformly to the surface of the material, and the depth of heating depends on the duration and intensity of the heat source.
- Induction Heating: Allows for controlled heating at specific depths within the material by adjusting the frequency of the alternating current. This capability is particularly useful in applications requiring selective heating or hardening of specific areas.
In summary, induction heating offers significant advantages over conventional heating methods, including higher efficiency, faster heating times, precise temperature control, and improved safety and cleanliness. These benefits make it a preferred choice for many industrial applications, particularly those requiring high precision and automation.
Summary Table:
Aspect | Conventional Heating | Induction Heating |
---|---|---|
Mechanism | External heat transfer (flames, heating elements) | Internal heat generation via electromagnetic induction |
Efficiency | ~20% efficiency (gas furnaces) | Up to 92% efficiency |
Heating Speed | Slower due to external heat transfer | Faster, as heat is generated directly within the material |
Temperature Control | Less precise | Highly precise and repeatable |
Safety & Cleanliness | Open flames or heating elements pose risks; potential contamination | Contactless, no open flames or fuel, reducing contamination risks |
Applications | Suitable for general use but less ideal for precision or automation | Ideal for precision, repeatability, and automation in industrial processes |
Depth of Heating | Uniform surface heating | Controlled heating at specific depths within the material |
Ready to upgrade your heating process? Contact our experts today to explore induction heating solutions!