Induction brazing is a highly efficient and precise method for joining metals using heat generated by electromagnetic induction. The duration of the process depends on several factors, including the materials being joined, the size and geometry of the components, the type of filler metal used, and the power of the induction heating system. Generally, induction brazing can take anywhere from a few seconds to several minutes. The process is faster than traditional brazing methods due to its localized heating, which minimizes heat-affected zones and reduces overall cycle times. Proper setup and optimization of parameters are crucial to achieving consistent and high-quality results.
Key Points Explained:
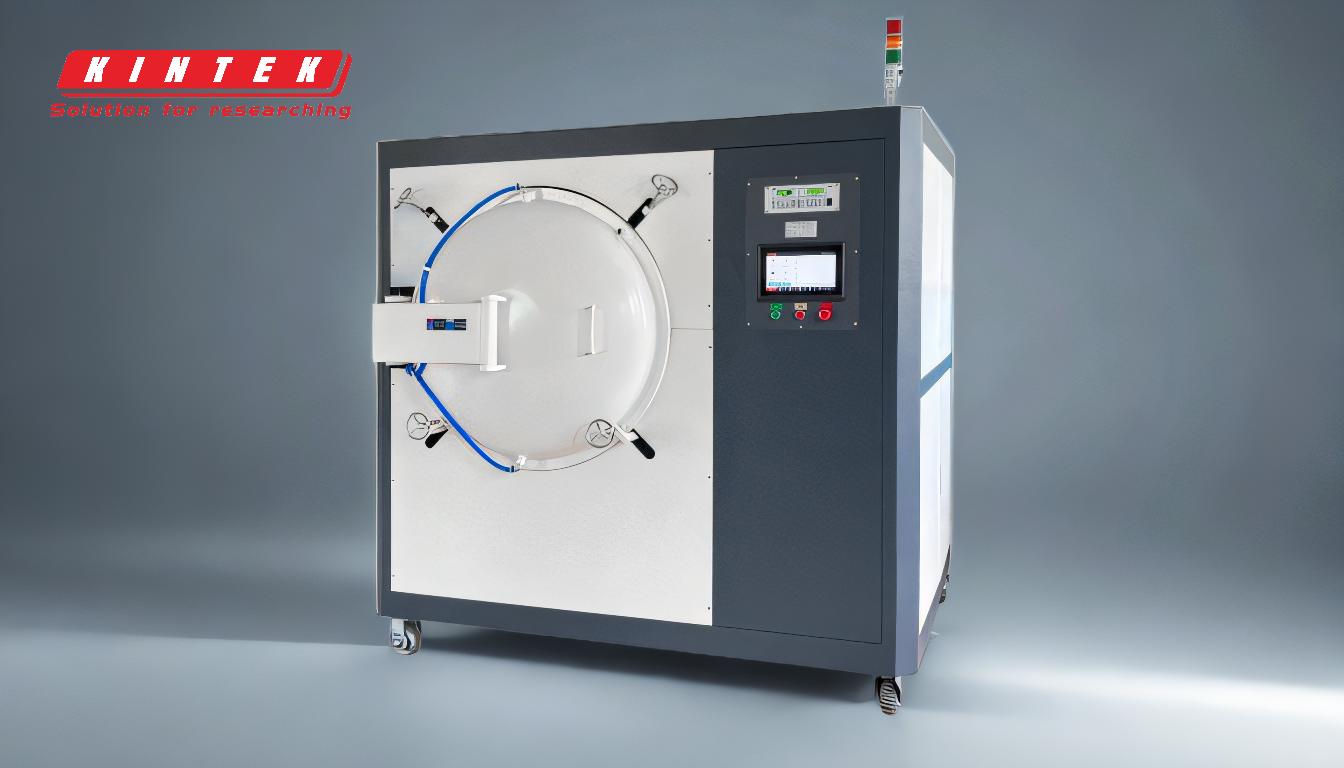
-
Factors Influencing Induction Brazing Time
- Material Properties: The thermal conductivity and melting points of the base metals and filler material significantly affect the heating time. For example, materials with high thermal conductivity, like copper, heat up faster than those with lower conductivity, such as stainless steel.
- Component Size and Geometry: Larger or more complex parts require more time to heat evenly. Thin sections heat faster than thick sections, and uniform geometries are easier to heat than irregular shapes.
- Filler Metal Characteristics: The melting point and flow characteristics of the filler metal influence the brazing time. Filler metals with lower melting points reduce the overall cycle time.
- Induction Heating Power: Higher power induction systems can generate heat more quickly, reducing the total brazing time. However, excessive power must be avoided to prevent overheating or damaging the components.
-
Typical Induction Brazing Time Range
- Induction brazing is generally much faster than traditional methods like torch brazing or furnace brazing.
- For small components, the process can take as little as 5 to 10 seconds.
- Medium-sized parts may require 30 seconds to 2 minutes.
- Larger or more complex assemblies can take 2 to 5 minutes or longer, depending on the factors mentioned above.
-
Advantages of Induction Brazing in Terms of Time Efficiency
- Localized Heating: Induction brazing heats only the specific area where the joint is located, reducing the overall heating time and minimizing energy consumption.
- Rapid Heating Rates: The electromagnetic induction process generates heat directly within the workpiece, allowing for faster heating compared to external heating methods.
- Reduced Cycle Times: The ability to precisely control heating and cooling cycles ensures efficient production, especially in high-volume manufacturing.
-
Optimizing Induction Brazing Time
- Proper Coil Design: The induction coil must be designed to match the geometry of the workpiece, ensuring even and efficient heating.
- Parameter Tuning: Adjusting parameters such as power, frequency, and heating time is essential to achieve optimal results without overheating or underheating.
- Pre-Placement of Filler Metal: Positioning the filler metal correctly before heating ensures uniform melting and flow, reducing the need for extended heating times.
-
Applications and Examples
- Automotive Industry: Induction brazing is used for joining components like heat exchangers and transmission parts, where fast cycle times are critical for high-volume production.
- Electronics: Small components such as connectors and terminals are often brazed in seconds using induction heating.
- Aerospace: Complex assemblies with stringent quality requirements benefit from the precision and speed of induction brazing.
-
Comparison with Other Brazing Methods
- Torch Brazing: Typically slower and less consistent due to manual control and broader heat application.
- Furnace Brazing: Suitable for large batches but often involves longer heating and cooling cycles, making it less time-efficient for small or medium-sized parts.
- Induction Brazing: Offers the best combination of speed, precision, and repeatability, making it ideal for modern manufacturing environments.
In conclusion, induction brazing is a versatile and time-efficient process that can be tailored to meet specific application requirements. By understanding and optimizing the factors that influence brazing time, manufacturers can achieve high-quality joints with minimal cycle times, enhancing productivity and reducing costs.
Summary Table:
Factor | Impact on Brazing Time |
---|---|
Material Properties | High thermal conductivity (e.g., copper) heats faster than low conductivity (e.g., steel). |
Component Size/Geometry | Larger or complex parts take longer; thin sections heat faster than thick ones. |
Filler Metal | Lower melting point filler metals reduce cycle time. |
Induction Heating Power | Higher power systems heat faster but require careful control to avoid damage. |
Typical Time Range | Small parts: 5-10 sec; Medium parts: 30 sec-2 min; Large parts: 2-5 min or more. |
Optimize your induction brazing process for faster, high-quality results—contact our experts today!