The thickness of PVD (Physical Vapor Deposition) coatings typically ranges from 0.25 to 5 microns. This thin layer is sufficient to enhance material properties such as hardness, wear resistance, and corrosion resistance without significantly altering the appearance or dimensions of the substrate. PVD coatings are widely used in various industries, including cutting tools, jewelry, and architectural components, due to their ability to provide functional and decorative finishes. The process operates at lower temperatures, making it suitable for heat-sensitive materials, and offers environmental benefits.
Key Points Explained:
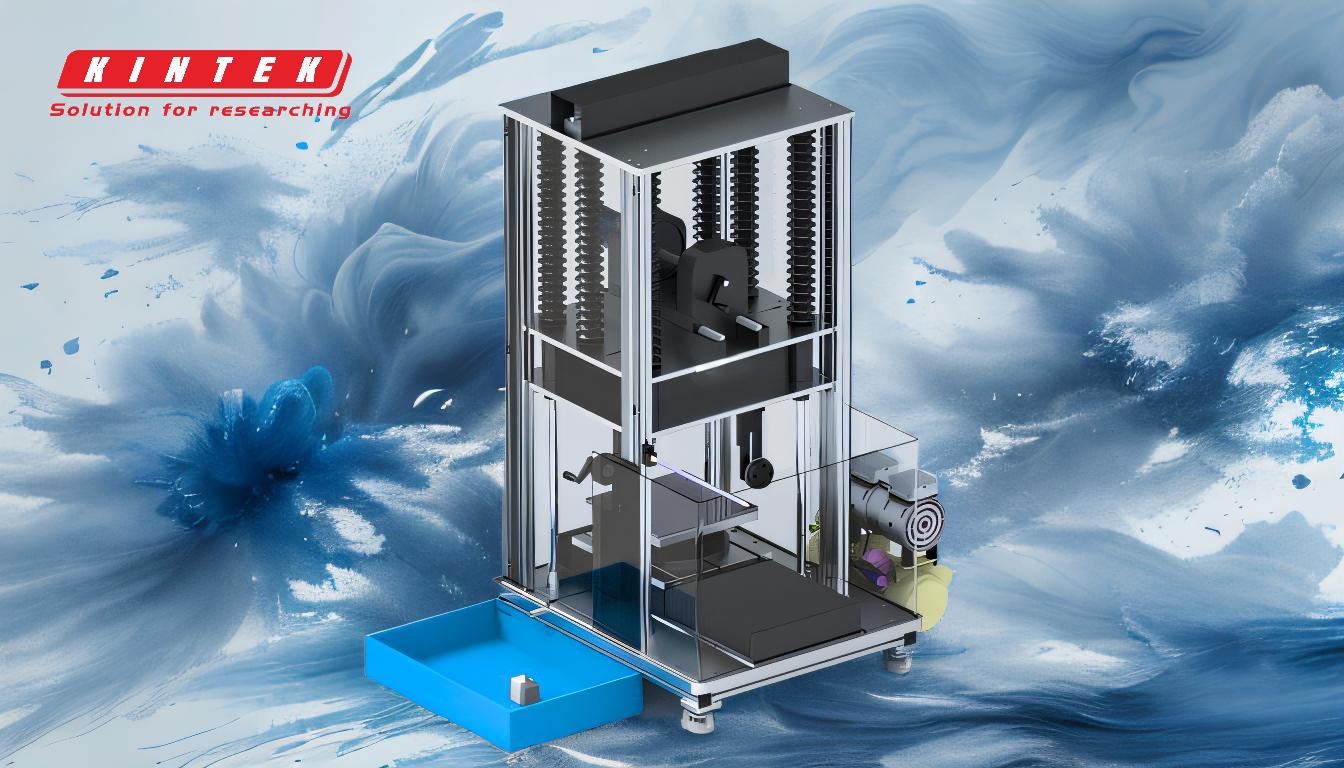
-
Typical Thickness Range of PVD Coatings:
- PVD coatings generally range from 0.25 to 5 microns in thickness. This range is thin enough to improve material properties without compromising the substrate's structural integrity or appearance.
- For jewelry, the thickness typically falls within the same range (0.25 to 5 microns), ensuring a decorative finish while maintaining the piece's delicate features.
- In functional applications, such as cutting tools, the thickness is often optimized between 2 to 5 microns to balance wear resistance and sharpness.
-
Comparison with Other Coating Methods:
- Compared to CVD (Chemical Vapor Deposition), which typically produces thicker coatings (5-10 microns), PVD coatings are thinner and more precise. This makes PVD ideal for applications requiring tight tolerances, such as fine blanking tools and optical coatings.
-
Advantages of Thin PVD Coatings:
- Enhanced Material Properties: PVD coatings improve hardness, wear resistance, and corrosion resistance while maintaining the substrate's original dimensions.
- Low Processing Temperatures: PVD operates at temperatures around 500 °C, reducing the risk of thermal damage to heat-sensitive materials.
- Environmental Friendliness: The process is eco-friendly, as it does not involve harmful chemicals or high energy consumption.
- Decorative and Functional Versatility: PVD coatings can provide both decorative finishes (e.g., jewelry) and functional enhancements (e.g., cutting tools).
-
Applications of PVD Coatings:
- Cutting Tools: PVD coatings are ideal for high-speed steel (HSS) and carbide tools, where a thin, hard layer preserves sharpness and reduces cutting force and heat.
- Jewelry: The thin coating enhances aesthetic appeal without adding significant weight or altering the design.
- Architectural Components: PVD coatings provide durable and decorative finishes for materials like stainless steel and glass.
-
Technical Considerations:
- Deposition Process: PVD is performed under vacuum conditions, allowing for precise control over coating thickness and uniformity.
- Compressive Stress Formation: During cooling, PVD coatings form compressive stress, which helps prevent crack formation and expansion, making them suitable for interrupted cutting processes like milling.
In summary, PVD coatings are a versatile and effective solution for enhancing material properties across a wide range of applications. Their thin, precise, and durable nature makes them a preferred choice in industries requiring both functional and decorative finishes.
Summary Table:
Aspect | Details |
---|---|
Thickness Range | 0.25 to 5 microns |
Applications | Cutting tools, jewelry, architectural components |
Key Benefits | Enhanced hardness, wear resistance, corrosion resistance, low-temperature processing |
Comparison with CVD | Thinner and more precise than CVD coatings (5-10 microns) |
Environmental Impact | Eco-friendly, no harmful chemicals or high energy consumption |
Interested in enhancing your materials with PVD coatings? Contact us today to learn more!