To make a glassy carbon electrode, the primary method involves pyrolyzing a carbon polymer under carefully controlled conditions at extremely high temperatures, typically around 2000°C. This process transforms the polymer into a unique material characterized by an intertwining ribbon-like structure, which retains high conductivity, hardness, and chemical inertness. These properties make glassy carbon electrodes highly suitable for applications in electrochemical analysis, such as voltammetry and biosensing. The production process requires precise temperature control and a controlled atmosphere to ensure the desired material properties are achieved.
Key Points Explained:
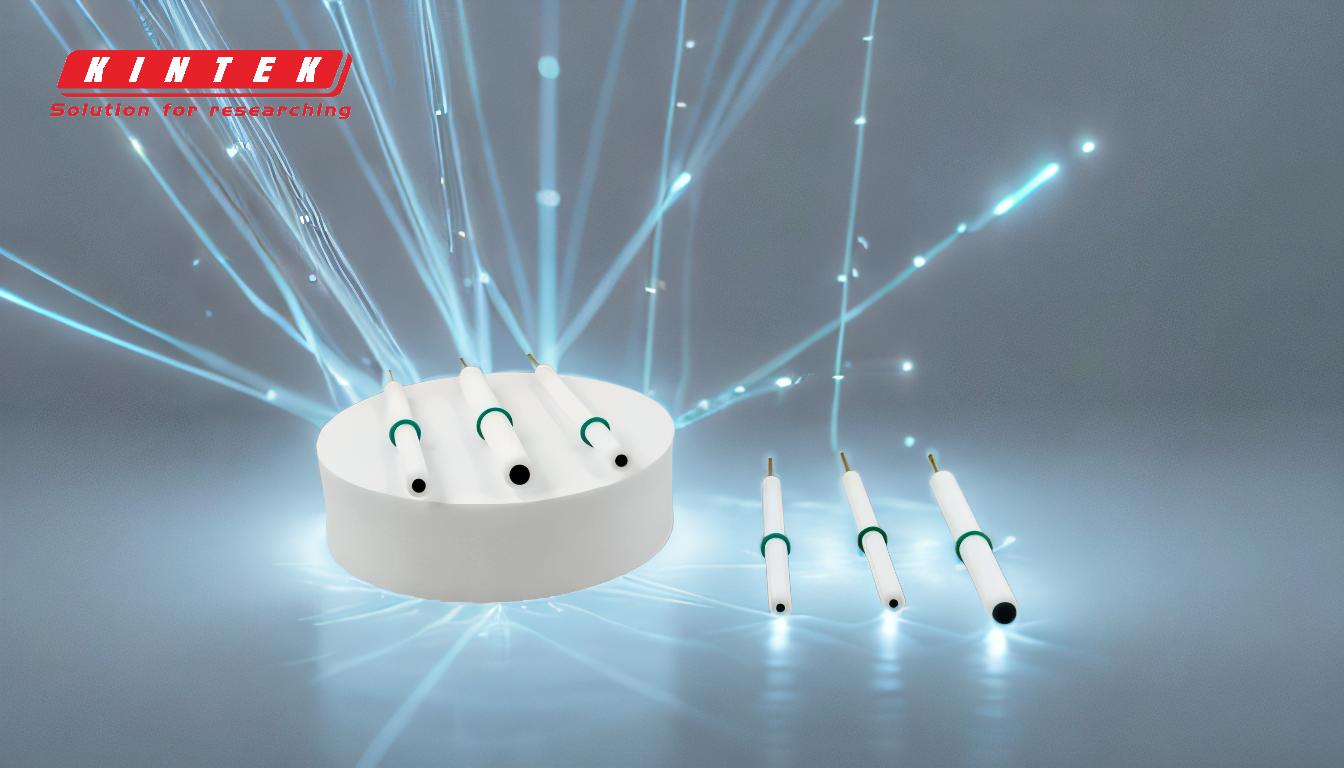
-
Material Selection:
- The process begins with selecting a suitable carbon polymer precursor. Common precursors include phenolic resins or other thermosetting polymers. These materials are chosen for their ability to form a stable carbon structure during pyrolysis.
-
Pyrolysis Process:
- The carbon polymer is subjected to pyrolysis, a thermal decomposition process that occurs in the absence of oxygen. This step is critical for converting the polymer into glassy carbon.
- The pyrolysis is conducted under carefully controlled conditions, including:
- Temperature: The polymer is heated to temperatures as high as 2000°C. This high temperature ensures the complete carbonization of the polymer and the formation of the glassy carbon structure.
- Atmosphere: The process is carried out in an inert atmosphere (e.g., nitrogen or argon) to prevent oxidation and ensure the formation of pure carbon.
-
Formation of Glassy Carbon Structure:
- During pyrolysis, the polymer undergoes a series of chemical transformations, leading to the formation of an intertwining ribbon-like structure. This structure is responsible for the unique properties of glassy carbon, including:
- High Conductivity: The ribbon-like structure allows for efficient electron transfer, making glassy carbon an excellent conductor.
- Hardness: The material becomes extremely hard, making it durable and resistant to physical damage.
- Chemical Inertness: Glassy carbon is highly resistant to chemical reactions, making it suitable for use in corrosive environments or in contact with reactive chemicals.
- During pyrolysis, the polymer undergoes a series of chemical transformations, leading to the formation of an intertwining ribbon-like structure. This structure is responsible for the unique properties of glassy carbon, including:
-
Post-Processing:
- After pyrolysis, the glassy carbon material may undergo additional processing steps to shape it into electrodes. This can include cutting, polishing, and cleaning to achieve the desired dimensions and surface finish.
- The final product is a glassy carbon electrode, ready for use in various electrochemical applications.
-
Applications of Glassy Carbon Electrodes:
- Glassy carbon electrodes are widely used in electrochemical analysis due to their excellent properties. Common applications include:
- Voltammetry: Used to study redox reactions and determine the concentration of analytes.
- Biosensing: Employed in the detection of biological molecules, such as glucose or DNA.
- Corrosion Studies: Utilized to investigate the corrosion behavior of metals and alloys.
- Glassy carbon electrodes are widely used in electrochemical analysis due to their excellent properties. Common applications include:
By following these steps, a glassy carbon electrode with the desired properties can be successfully produced, making it a valuable tool in electrochemical research and analysis.
Summary Table:
Step | Details |
---|---|
Material Selection | Choose carbon polymer precursors like phenolic resins for stable pyrolysis. |
Pyrolysis Process | Heat to ~2000°C in an inert atmosphere (e.g., nitrogen or argon). |
Structure Formation | Forms an intertwining ribbon-like structure for high conductivity & hardness. |
Post-Processing | Cutting, polishing, and cleaning to shape the electrode. |
Applications | Voltammetry, biosensing, and corrosion studies. |
Discover how glassy carbon electrodes can enhance your electrochemical research—contact us today!