The deposition rate in sputtering processes is influenced by a variety of factors, including the properties of the target material, the methodologies employed during the process, and the performance of the sputtering system itself. Understanding these factors is crucial for optimizing the deposition rate and achieving the desired film quality. Below, we will explore the key elements that affect the deposition rate in detail.
Key Points Explained:
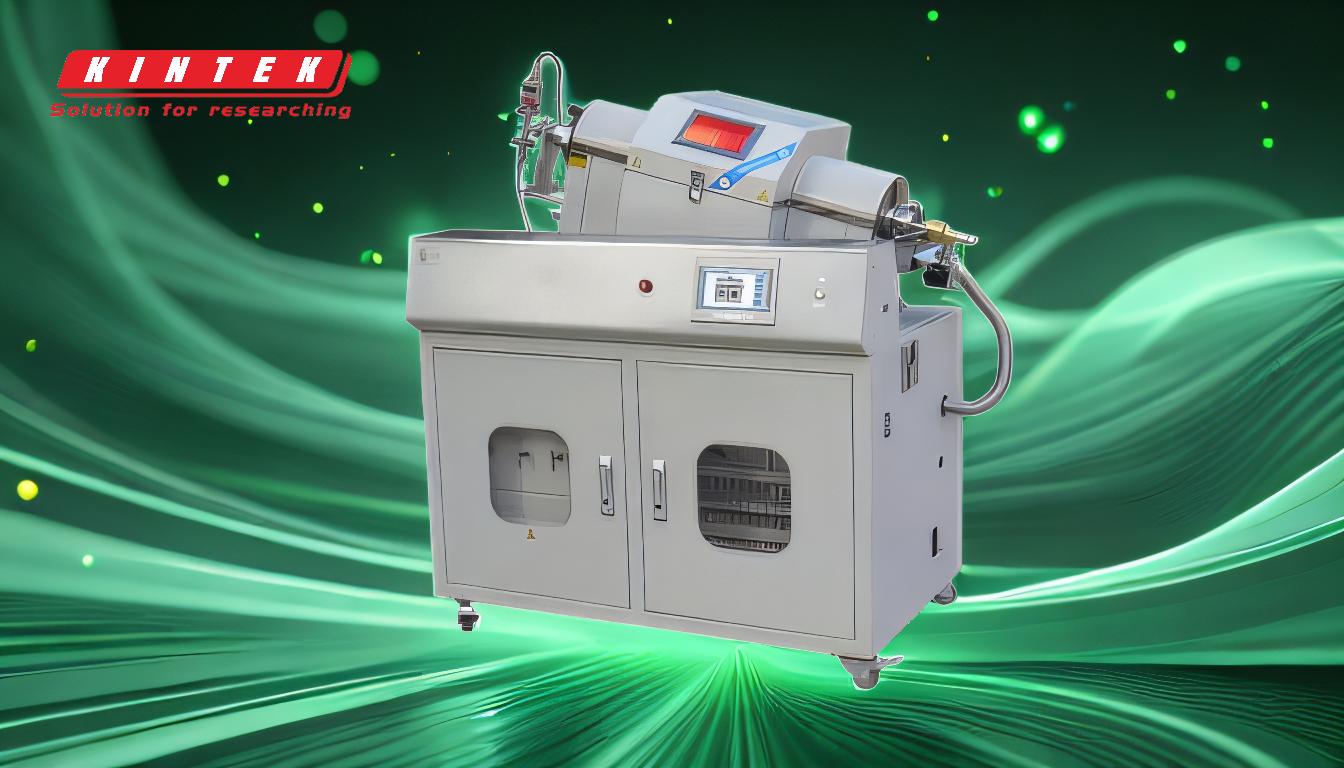
-
Target Material Properties:
- Material Composition: The type of material being sputtered significantly impacts the deposition rate. Different materials have varying sputtering yields, which is the number of atoms ejected from the target per incident ion. For example, metals generally have higher sputtering yields compared to insulators.
- Purity and Density: High-purity targets tend to have more consistent and predictable deposition rates. Impurities can lead to irregularities in the sputtering process, affecting the rate and quality of the deposited film.
- Surface Condition: The surface roughness and cleanliness of the target material can also influence the deposition rate. A smoother and cleaner surface typically results in a more uniform and higher deposition rate.
-
Process Methodologies:
- Sputtering Power: The power applied to the sputtering system directly affects the deposition rate. Higher power levels increase the energy of the ions bombarding the target, leading to a higher sputtering yield and thus a higher deposition rate.
- Gas Pressure and Composition: The type and pressure of the sputtering gas (usually argon) play a critical role. Optimal gas pressure ensures efficient ion bombardment, while deviations can lead to either insufficient sputtering or excessive scattering of sputtered atoms.
- Substrate Temperature: The temperature of the substrate can influence the mobility of the deposited atoms, affecting the film's growth rate and quality. Higher temperatures generally enhance atom mobility, leading to better film quality but potentially affecting the deposition rate.
-
Sputtering System Performance:
- Magnetic Field Configuration: In magnetron sputtering systems, the magnetic field configuration affects the plasma density and, consequently, the deposition rate. A well-optimized magnetic field can enhance the ionization of the sputtering gas, leading to a higher deposition rate.
- Target-to-Substrate Distance: The distance between the target and the substrate can influence the deposition rate. A shorter distance generally results in a higher deposition rate due to reduced scattering of sputtered atoms, but it must be balanced to avoid non-uniform film deposition.
- System Vacuum Level: The vacuum level within the sputtering chamber is crucial. A high vacuum reduces the presence of contaminants and ensures efficient sputtering. Poor vacuum conditions can lead to impurities in the film and a lower deposition rate.
In summary, the deposition rate in sputtering processes is a complex interplay of target material properties, process methodologies, and sputtering system performance. By carefully controlling these factors, it is possible to optimize the deposition rate and achieve high-quality films. Understanding these elements allows for better process design and troubleshooting, ultimately leading to more efficient and effective sputtering operations.
Summary Table:
Factor | Key Details |
---|---|
Target Material Properties | - Material Composition: Metals have higher sputtering yields than insulators. |
- Purity and Density: High-purity targets ensure consistent deposition rates. | |
- Surface Condition: Smoother, cleaner surfaces yield higher deposition rates. | |
Process Methodologies | - Sputtering Power: Higher power increases deposition rate. |
- Gas Pressure and Composition: Optimal argon pressure ensures efficient sputtering. | |
- Substrate Temperature: Higher temperatures enhance atom mobility and film quality. | |
Sputtering System Performance | - Magnetic Field Configuration: Optimized fields enhance plasma density. |
- Target-to-Substrate Distance: Shorter distances reduce scattering of atoms. | |
- System Vacuum Level: High vacuum ensures efficient sputtering and reduces impurities. |
Optimize your sputtering process today—contact our experts for tailored solutions!