Laser sintering is a type of additive manufacturing (3D printing) technology that uses a high-powered laser to fuse powdered material into a solid structure. It is widely used in industries such as aerospace, automotive, and healthcare for creating complex, high-precision parts. The process involves layering powdered material and selectively sintering it with a laser to build the desired object layer by layer. This method is particularly advantageous for producing parts with intricate geometries, high strength, and excellent surface finish. It is also energy-efficient and cost-effective, as it minimizes material waste and allows for the use of high-melting-point materials without melting them entirely.
Key Points Explained:
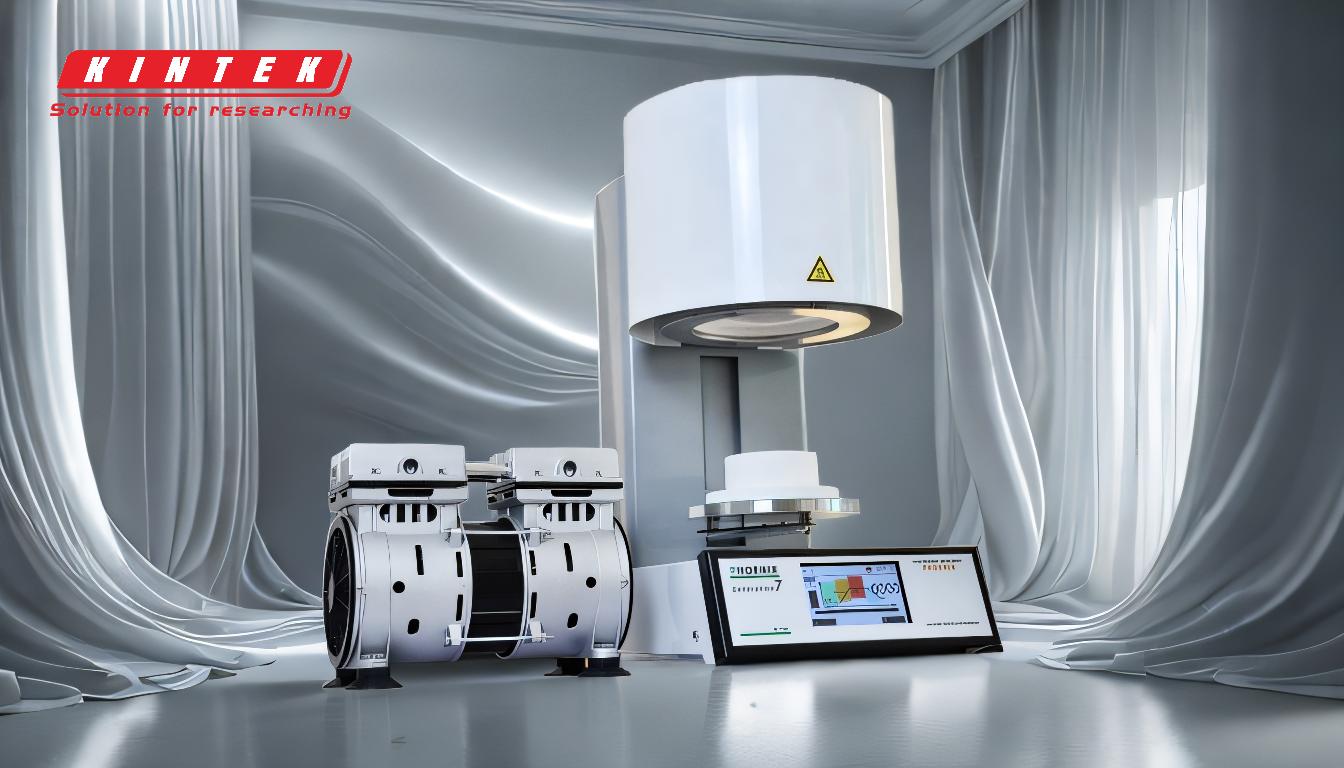
-
Definition of Laser Sintering:
- Laser sintering is an additive manufacturing process that uses a laser to fuse powdered material into a solid structure.
- It is a layer-by-layer process, where each layer of powder is selectively sintered to create the final 3D object.
-
Materials Used in Laser Sintering:
- Common materials include metals (e.g., titanium, aluminum, stainless steel), polymers (e.g., nylon, polyamide), and ceramics.
- The choice of material depends on the desired properties of the final part, such as strength, durability, and thermal resistance.
-
Process Overview:
- Step 1: Preparation: A 3D model of the part is created using CAD software and sliced into thin layers.
- Step 2: Powder Deposition: A thin layer of powdered material is spread evenly across the build platform.
- Step 3: Laser Sintering: A high-powered laser scans the powder bed, selectively sintering the powder according to the 3D model's design.
- Step 4: Layer Addition: The build platform lowers, and a new layer of powder is spread over the previous layer. The process repeats until the part is complete.
- Step 5: Post-Processing: After the part is built, it may undergo additional processes such as cooling, cleaning, and surface finishing.
-
Advantages of Laser Sintering:
- Material Conservation: Laser sintering minimizes material waste, as only the necessary powder is sintered.
- Energy Efficiency: The process requires less energy compared to traditional manufacturing methods, as it does not involve melting the entire material.
- Cost-Effectiveness: Reduced material waste and energy consumption lead to lower production costs.
- Design Flexibility: Laser sintering allows for the creation of complex geometries and intricate designs that would be difficult or impossible to achieve with traditional methods.
- High Precision and Consistency: The process offers excellent control over the sintering process, resulting in parts with high dimensional accuracy and consistent quality.
- Enhanced Material Properties: Sintered parts often exhibit improved mechanical properties, such as increased strength and hardness, due to the controlled sintering process.
-
Applications of Laser Sintering:
- Aerospace: Used to manufacture lightweight, high-strength components such as turbine blades and structural parts.
- Automotive: Applied in the production of custom parts, prototypes, and complex components like engine parts and brackets.
- Healthcare: Utilized for creating patient-specific implants, prosthetics, and surgical instruments with high precision.
- Consumer Goods: Employed in the production of custom jewelry, eyewear, and other consumer products with intricate designs.
-
Challenges and Considerations:
- Material Limitations: Not all materials are suitable for laser sintering, and some may require specialized powders or post-processing treatments.
- Surface Finish: While laser sintering produces parts with good surface finish, additional post-processing may be required for applications requiring ultra-smooth surfaces.
- Cost of Equipment: The initial investment in laser sintering equipment can be high, which may be a barrier for small-scale manufacturers.
- Process Control: Achieving consistent results requires precise control over parameters such as laser power, scanning speed, and powder layer thickness.
In summary, laser sintering is a versatile and efficient additive manufacturing method that offers numerous advantages, including material conservation, energy efficiency, and the ability to produce complex, high-precision parts. Despite some challenges, it is widely used across various industries for its ability to create durable, high-quality components with minimal waste.
Summary Table:
Aspect | Details |
---|---|
Definition | Additive manufacturing using a laser to fuse powdered material layer by layer. |
Materials | Metals (titanium, aluminum), polymers (nylon), ceramics. |
Process Steps | Preparation, powder deposition, laser sintering, layer addition, post-processing. |
Advantages | Material conservation, energy efficiency, cost-effectiveness, design flexibility, high precision. |
Applications | Aerospace, automotive, healthcare, consumer goods. |
Challenges | Material limitations, surface finish, equipment cost, process control. |
Ready to explore how laser sintering can enhance your production process? Contact us today to learn more!