Sintered parts are intricate, complex-shaped components produced through a process called sintering, which involves compacting powdered materials into a desired shape (green state) and then heating them to bond the particles without melting the material completely. This process is particularly useful for materials with high melting points, such as tungsten and molybdenum. Sintered parts are widely used across industries like automotive, aerospace, biomedical, and fashion due to their near-net-shape production, energy efficiency, and ability to create custom shapes. The sintering process enhances material properties by reducing porosity and improving strength, making it a versatile manufacturing technique for both traditional and advanced applications, including additive manufacturing and powder metallurgy.
Key Points Explained:
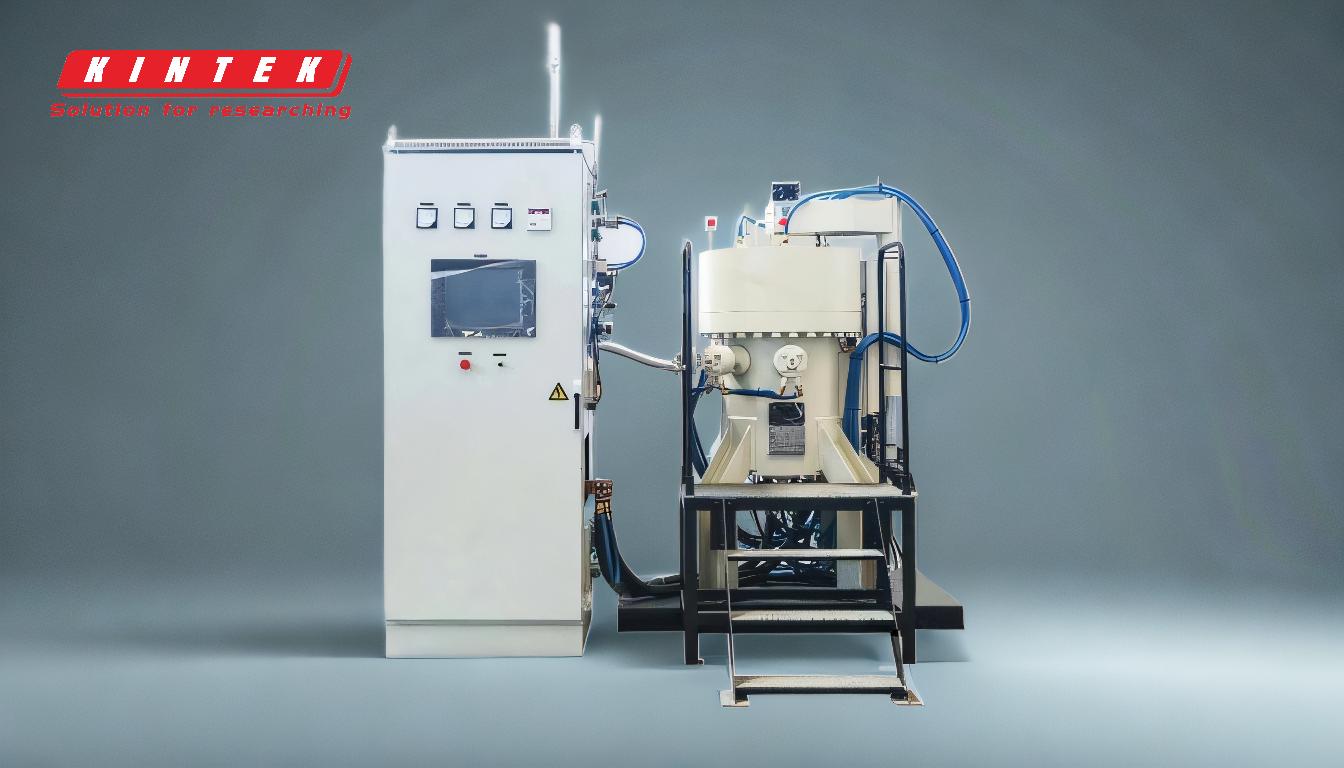
-
Definition of Sintered Parts
- Sintered parts are components created by compacting powdered materials into a specific shape (green state) and then heating them to bond the particles together without fully melting the material.
- This process is particularly effective for materials with high melting points, such as tungsten and molybdenum, where traditional melting methods are impractical.
-
How Sintering Works
- Sintering involves applying heat or pressure to powdered materials, causing the atoms to diffuse across particle boundaries and fuse together.
- The process avoids liquefaction, making it energy-efficient compared to melting.
- It reduces surface porosity, enhancing the material's mechanical properties, such as strength and durability.
-
Applications of Sintered Parts
- Automotive Industry: Used for components like gears, bearings, and filters due to their strength and precision.
- Biomedical Industry: Utilized in dental implants and surgical instruments because of their biocompatibility and customizability.
- Aerospace Industry: Employed for lightweight, high-strength parts that can withstand extreme conditions.
- Fashion Industry: Used in jewelry and accessories for intricate designs and durability.
- Additive Manufacturing: Enables the creation of custom metal shapes layer by layer using 3D printing technologies like binder jetting and metal FDM.
-
Technologies Used in Sintering
- Powder Pressing: Compacts metal powders into a mold to form the green state.
- Metal Injection Molding (MIM): Combines metal powders with a binder to create complex shapes, which are then sintered.
- Binder Jetting: A 3D printing method that uses a liquid binder to join powder particles, followed by sintering.
- Metal FDM (Fused Deposition Modeling): Extrudes metal-filled filaments to build parts layer by layer, which are then sintered.
-
Advantages of Sintering
- Energy Efficiency: Lower temperatures are required compared to melting, saving energy.
- Material Versatility: Suitable for high-melting-point materials and a wide range of applications.
- Customizability: Allows for the production of complex, near-net-shape parts with minimal post-processing.
- Improved Properties: Reduces porosity and enhances strength, making sintered parts ideal for demanding applications.
-
Industries Benefiting from Sintering
- Aerospace: Lightweight, high-strength components for aircraft and spacecraft.
- Dental Equipment: Biocompatible materials for implants and tools.
- Battery Manufacturing: Electrodes and other components with precise geometries.
- Engineering and Research: Custom parts for prototyping and experimentation.
- Automotive: Durable and precise parts for engines, transmissions, and other systems.
-
Future of Sintering
- As new sintering technologies emerge, the range of applications continues to expand.
- Innovations in additive manufacturing and material science are driving the development of more efficient and versatile sintering processes.
- Sintering is increasingly being integrated into sustainable manufacturing practices due to its energy efficiency and material conservation benefits.
By understanding the sintering process and its applications, equipment and consumable purchasers can make informed decisions about the suitability of sintered parts for their specific needs, ensuring optimal performance and cost-effectiveness.
Summary Table:
Aspect | Details |
---|---|
Definition | Components made by compacting and heating powdered materials without melting. |
Process | Heat or pressure bonds particles, reducing porosity and enhancing strength. |
Applications | Automotive, aerospace, biomedical, fashion, additive manufacturing. |
Technologies Used | Powder pressing, MIM, binder jetting, metal FDM. |
Advantages | Energy-efficient, versatile, customizable, improved material properties. |
Industries Benefiting | Aerospace, dental, battery manufacturing, engineering, automotive. |
Future Trends | Innovations in additive manufacturing and sustainable practices. |
Explore how sintered parts can transform your manufacturing process—contact our experts today!