Graphite furnaces are widely used in high-temperature applications due to their unique properties, such as fast heating speed, excellent temperature uniformity, and high-temperature controllability. They are particularly suitable for processes like sintering, graphitizing, and pyrolysis, and are favored in metallurgical and corrosive environments. However, graphite furnaces also have disadvantages, including the need for careful handling due to their brittleness and susceptibility to oxidation at high temperatures. Additionally, while graphite is lightweight and easy to repair, it may require protective layers to extend its lifespan in harsh conditions. Overall, graphite furnaces offer significant advantages but require proper maintenance and operational considerations.
Key Points Explained:
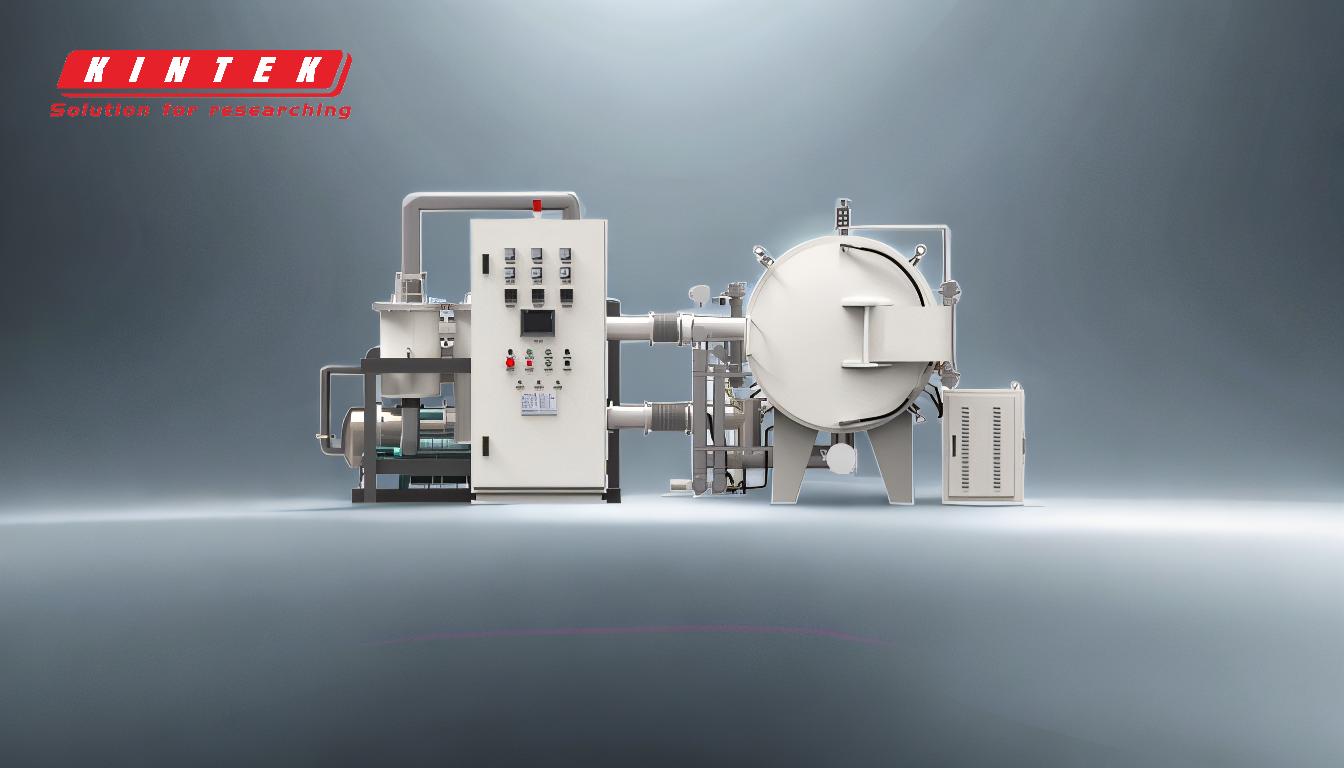
Advantages of Graphite Furnaces:
-
Fast Heating Speed:
- Graphite furnaces heat up quickly due to the material's low thermal capacity and high thermal conductivity. This makes them ideal for applications requiring rapid temperature changes, such as sintering and pyrolysis.
-
Excellent Temperature Uniformity:
- The emissivity of graphite is close to 1, creating near-ideal black body conditions. This ensures uniform heat distribution within the furnace, which is critical for processes like alloy melting and high-temperature testing.
-
High-Temperature Controllability:
- Graphite furnaces can achieve extremely high temperatures with precise control, making them suitable for advanced applications such as graphitizing and silicizing.
-
Lightweight and Durable:
- Graphite's low density and modest thermal capacity reduce the overall weight of the furnace, making it easier to handle and install. Additionally, graphite is easily repairable, and sacrificial layers can be applied to enhance its durability in corrosive environments.
-
Versatility in Applications:
- Graphite furnaces are used in a wide range of high-temperature processes, including melting alloys, pressure sintering, foaming, and studying reaction kinetics at extreme conditions.
Disadvantages of Graphite Furnaces:
-
Brittleness and Susceptibility to Damage:
- Graphite is brittle and can crack or break under mechanical stress. This requires careful handling during installation, operation, and maintenance.
-
Oxidation at High Temperatures:
- Graphite oxidizes when exposed to air at high temperatures, which can degrade its performance over time. Protective atmospheres or coatings are often needed to mitigate this issue.
-
Cost and Maintenance:
- While graphite is repairable, the need for protective layers and regular maintenance can increase operational costs. Additionally, the initial investment in high-quality graphite materials can be significant.
-
Orientation-Specific Properties:
- Graphite's properties, such as thermal conductivity, can vary depending on the orientation of the material. This requires careful design and engineering to ensure optimal performance.
-
Limited Lifespan in Harsh Conditions:
- Despite its durability, graphite may degrade over time in highly corrosive or high-temperature environments, necessitating periodic replacement or refurbishment.
Applications of Graphite Furnaces:
-
Metallurgical Processes:
- Graphite furnaces are commonly used for melting and alloying metals due to their ability to achieve high temperatures and maintain uniform heat distribution.
-
High-Temperature Testing:
- They are ideal for test facilities that require precise temperature control and uniformity, such as investigations of reaction kinetics and solid electrolyte heating.
-
Industrial Processes:
- Graphite furnaces are employed in sintering, graphitizing, silicizing, and pyrolysis, where high temperatures and controlled environments are essential.
-
Research and Development:
- Their versatility and controllability make graphite furnaces valuable tools for R&D in materials science and high-temperature chemistry.
In summary, graphite furnaces offer significant advantages in terms of heating speed, temperature uniformity, and controllability, making them indispensable in high-temperature applications. However, their brittleness, susceptibility to oxidation, and maintenance requirements are important considerations. Proper handling, protective measures, and regular maintenance can help maximize their performance and lifespan.
Summary Table:
Aspect | Advantages | Disadvantages |
---|---|---|
Heating Speed | Fast heating due to low thermal capacity and high thermal conductivity. | Brittle and prone to cracking under mechanical stress. |
Temperature Uniformity | Excellent uniformity with near-ideal black body conditions. | Susceptible to oxidation at high temperatures, requiring protective measures. |
Controllability | Precise high-temperature control for advanced applications. | Higher maintenance costs due to protective layers and regular upkeep. |
Durability | Lightweight, easy to repair, and can be enhanced with sacrificial layers. | Orientation-specific properties may affect performance. |
Applications | Versatile for metallurgical, industrial, and R&D processes. | Limited lifespan in harsh conditions, requiring periodic replacement. |
Discover how graphite furnaces can optimize your high-temperature processes—contact us today for expert advice!