Sintering is a critical process in material science and manufacturing, offering numerous advantages that enhance the properties and performance of materials. It involves heating powdered materials to a temperature below their melting point, causing the particles to bond and form a solid structure. This process is widely used in various industries, including automotive, aerospace, and electronics, due to its ability to improve material properties, reduce costs, and enable the production of complex shapes. The use of a sintering furnace is essential in achieving these benefits, as it provides the controlled environment needed for precise temperature and pressure management.
Key Points Explained:
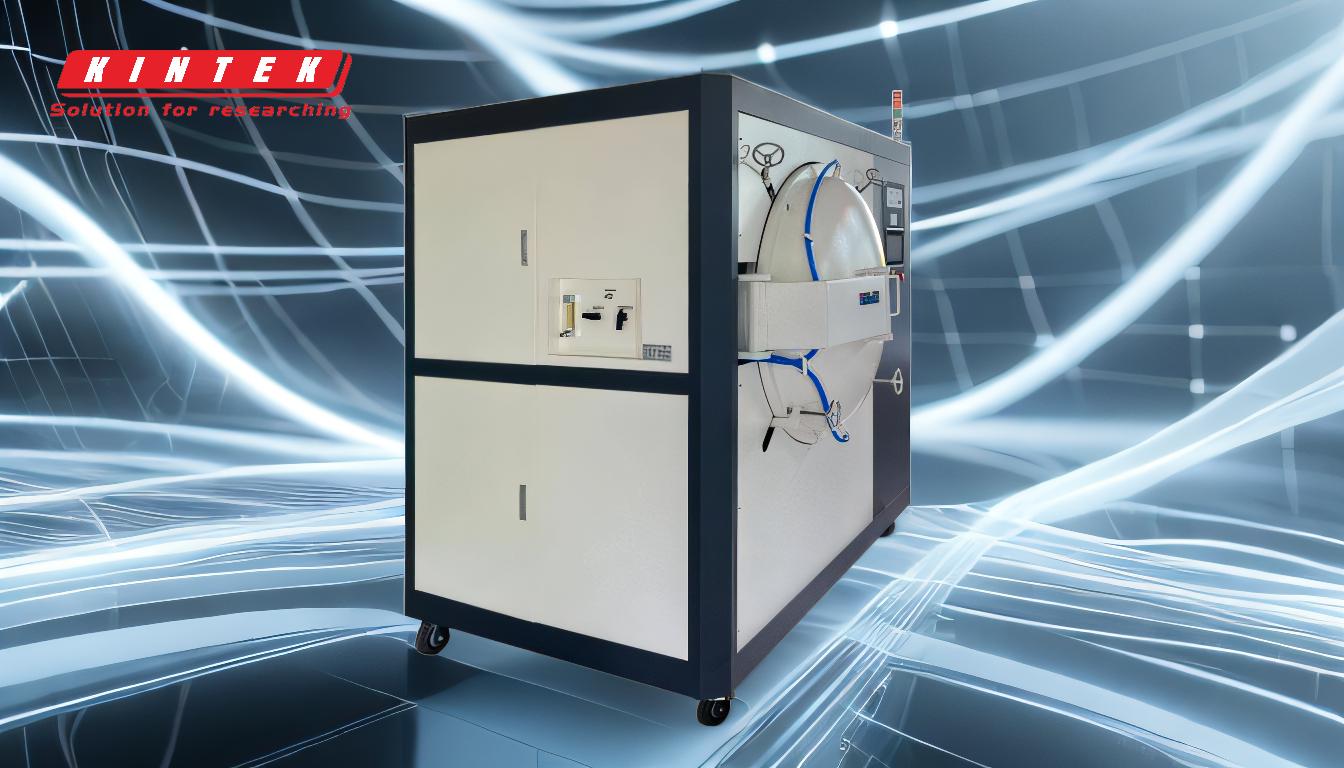
-
Enhanced Material Properties:
- Sintering improves the thermal and electrical conductivity, strength, and integrity of materials. This is particularly beneficial for components that require high performance and durability, such as those used in machinery or vehicles.
- The process also enhances translucency, which is crucial for materials used in optical applications.
-
Design Flexibility and Complex Shapes:
- Sintering allows for the production of highly complex parts and shapes that would be difficult or impossible to achieve with traditional manufacturing methods. This flexibility is invaluable in industries where intricate designs are required.
- The ability to create components with high porosity, such as those used in plumbing or ball bearings, is another significant advantage.
-
Cost Efficiency and Material Savings:
- The sintering process generates less material waste compared to other manufacturing techniques, leading to lowered costs. This is especially beneficial for high-volume production.
- The ability to produce parts from a variety of materials further enhances cost efficiency by allowing manufacturers to choose the most economical material for their needs.
-
Superior Quality and Fewer Defects:
- Sintering results in parts with excellent surface finishes and good tolerance control, reducing the need for additional finishing processes.
- The process minimizes defects, leading to superior quality components that are less likely to fail in critical applications.
-
Environmentally Friendly Process:
- Sintering is an environmentally friendly process, as it produces less waste and can be performed in a controlled environment that minimizes emissions. This is increasingly important in industries striving to reduce their environmental impact.
-
Quick Turnaround and High Productivity:
- The use of advanced sintering furnaces allows for quick turnaround times, as the process can be optimized through programmable stages that adjust temperature, ramp rates, and hold times.
- This optimization leads to maximum productivity, making sintering a highly efficient manufacturing method.
-
Versatility in Applications:
- Sintering is used in a wide range of applications, from creating metallic compounds that reduce component failure to producing materials with specific properties, such as high porosity or enhanced strength.
- The process is also crucial in the Metal Injection Molding (MIM) process, where it is used to achieve the desired density and remove impurities, enhancing the mechanical properties and surface quality of the final part.
In summary, sintering offers a multitude of advantages that make it a preferred method in various industries. The use of a sintering furnace is integral to achieving these benefits, providing the controlled environment necessary for precise and efficient material processing. Whether for enhancing material properties, reducing costs, or enabling complex designs, sintering is a versatile and valuable process in modern manufacturing.
Summary Table:
Advantage | Description |
---|---|
Enhanced Material Properties | Improves conductivity, strength, and translucency for high-performance materials. |
Design Flexibility | Enables production of complex shapes and high-porosity components. |
Cost Efficiency | Reduces material waste and lowers production costs. |
Superior Quality | Produces parts with excellent finishes, tolerance control, and fewer defects. |
Environmentally Friendly | Minimizes waste and emissions, supporting sustainable manufacturing. |
Quick Turnaround | Optimized sintering furnaces ensure high productivity and efficiency. |
Versatility in Applications | Used in automotive, aerospace, electronics, and Metal Injection Molding (MIM). |
Unlock the full potential of sintering for your manufacturing needs—contact our experts today!