Vertical core induction type furnaces are specialized equipment used in various industrial applications, particularly where precise and controlled heating is required. These furnaces are known for their efficiency, scalability, and ability to handle high-temperature processes. They are widely used in industries such as aerospace, metallurgy, electronics, and manufacturing, where they play a critical role in melting, alloying, and heat treatment processes. The vertical orientation of these furnaces ensures uniform heating, making them ideal for applications like sintering, calcination, and the production of high-performance materials.
Key Points Explained:
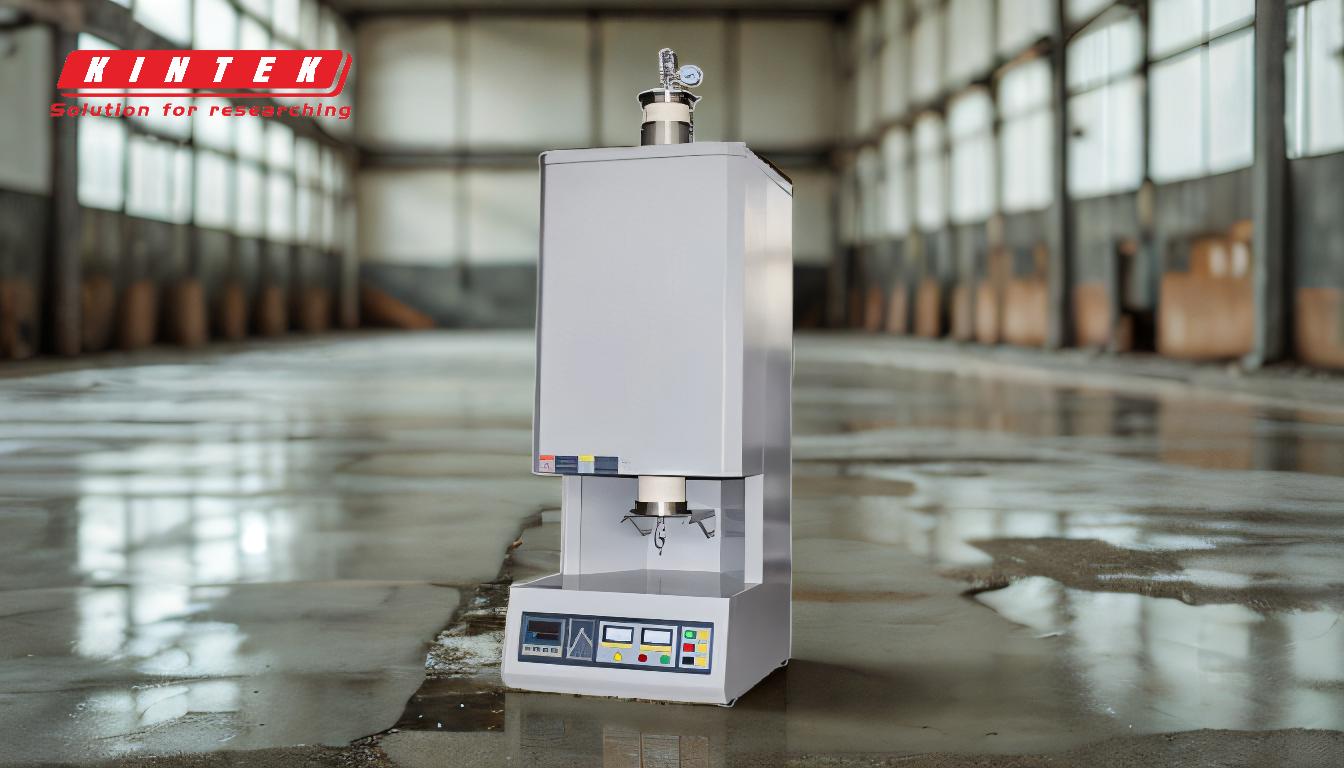
-
High-Temperature Applications:
- Vertical core induction furnaces are capable of reaching extremely high temperatures, making them suitable for processes like melting, alloying, and heat treatment. These furnaces are often used in the production of high-temperature alloys, stainless steel, and other specialized materials required in industries such as aerospace and atomic energy.
- Their ability to maintain uniform heating ensures consistent quality in the final product, which is critical for applications in precision engineering and advanced manufacturing.
-
Uniform Heating for Precision Processes:
- The vertical orientation of these furnaces allows for uniform heating of materials, which is essential for processes like sintering and calcination. This uniformity is particularly important in the production of powders and ceramics, where even heat distribution is necessary to achieve the desired material properties.
- This feature also makes them ideal for laboratory work and R&D, where precise control over heating conditions is required to develop new materials or improve existing ones.
-
Versatility in Industrial Applications:
- Vertical core induction furnaces are used in a wide range of industrial applications, including aging, annealing, brazing, and curing. Their modular and scalable design makes them adaptable to various investment programs, catering to the needs of both small foundries and large-scale manufacturing facilities.
- They are also employed in the production of magnetic materials, elastic alloys, and expansion alloys, which are critical components in the electronics and engineering industries.
-
Role in Vacuum Metallurgy:
- These furnaces are integral to vacuum metallurgy, where they are used to melt alloys and special steels. The vacuum environment prevents contamination and ensures the production of high-purity materials, which are essential for applications in aerospace, missiles, rockets, and atomic energy equipment.
- The ability to operate under vacuum conditions also makes them suitable for producing ultra-high-strength steel, tool steel, and bearing steel, which require precise control over composition and microstructure.
-
Benefits for Foundries and Manufacturing:
- Vertical core induction furnaces are highly beneficial for foundries and manufacturing industries, particularly in the production of castings and metal components. Their efficiency and ability to handle large volumes of material make them a cost-effective solution for mass production.
- They are also used in the gold smelting sector, where their high-temperature capabilities and precise control ensure efficient extraction and refining of precious metals.
-
Adaptability for Laboratories and R&D:
- These furnaces are widely used in laboratories and R&D centers for developing new materials and improving existing processes. Their modular design allows for easy customization, making them suitable for a wide range of experimental setups.
- They are particularly valuable in the development of high-performance materials, such as heat-resistant steel and magnetic alloys, which require precise control over heating and cooling rates.
In summary, vertical core induction type furnaces are versatile and efficient tools used across a wide range of industries. Their ability to provide uniform heating, operate at high temperatures, and function in vacuum environments makes them indispensable for applications in metallurgy, aerospace, electronics, and manufacturing. Their adaptability and scalability further enhance their value, making them a critical component in both industrial and research settings.
Summary Table:
Application | Key Benefits |
---|---|
High-Temperature Processes | Melting, alloying, heat treatment, and production of high-performance materials. |
Uniform Heating | Ideal for sintering, calcination, and precision engineering applications. |
Industrial Versatility | Aging, annealing, brazing, curing, and production of magnetic/elastic alloys. |
Vacuum Metallurgy | High-purity material production for aerospace, atomic energy, and tool steel. |
Foundries and Manufacturing | Cost-effective mass production of castings and metal components. |
Laboratories and R&D | Development of heat-resistant steel, magnetic alloys, and advanced materials. |
Unlock the potential of vertical core induction furnaces for your industry—contact our experts today to learn more!