Heat treatment is a critical process in metallurgy and materials science, aimed at altering the physical and sometimes chemical properties of a material. The basic characteristics requirements in heat treatment include precise control over temperature, heating and cooling rates, and the environment in which the treatment occurs. These factors are crucial for achieving the desired mechanical properties such as hardness, toughness, and ductility. Additionally, the material's composition and the specific heat treatment method (e.g., annealing, quenching, tempering) play significant roles in determining the final outcome. Understanding these requirements is essential for optimizing the heat treatment process to achieve the desired material properties.
Key Points Explained:
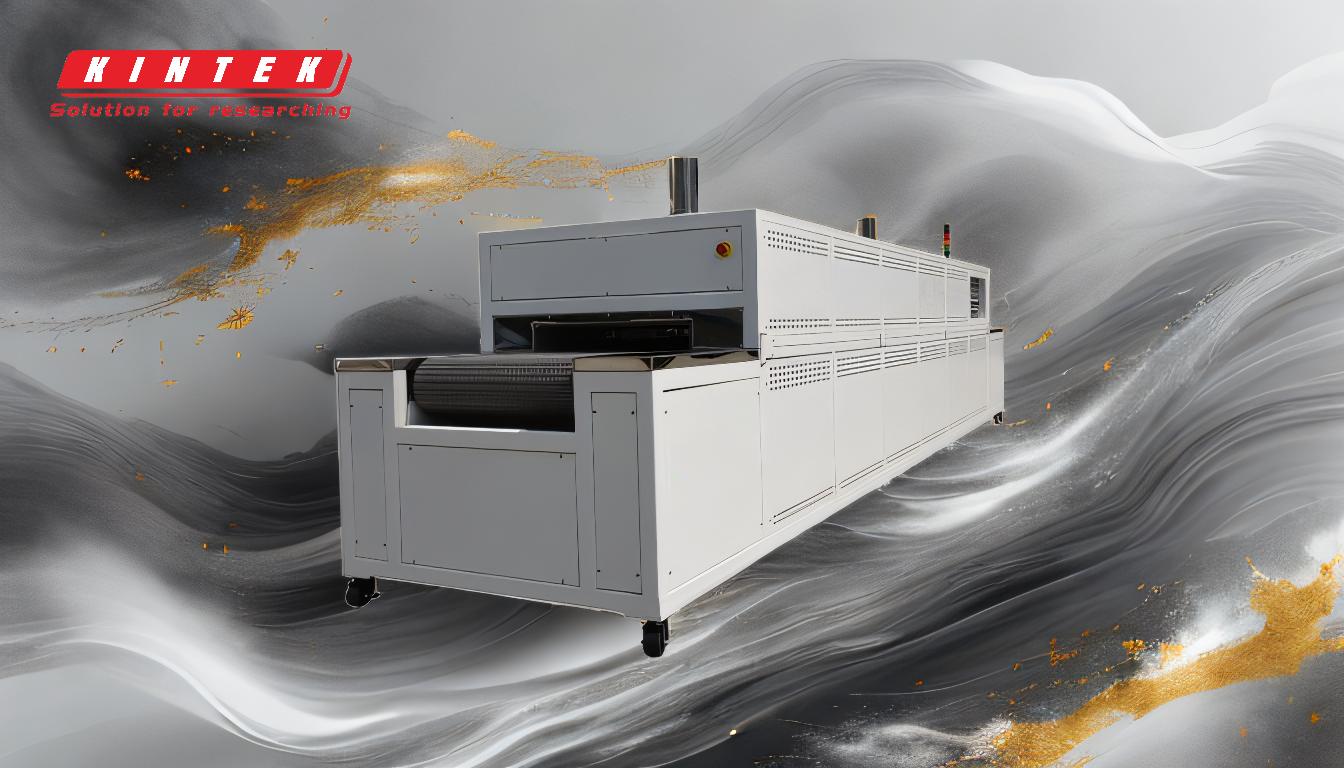
-
Temperature Control
- Precision: Accurate temperature control is paramount in heat treatment. The temperature must be precisely managed to ensure that the material reaches the correct phase transformation points.
- Uniformity: The material must be heated uniformly to prevent internal stresses and uneven properties.
- Monitoring: Continuous monitoring and adjustment of temperature are necessary to maintain the desired conditions throughout the process.
-
Heating and Cooling Rates
- Heating Rate: The rate at which the material is heated can affect the microstructure and properties. Too rapid heating can lead to thermal stresses, while too slow heating may not achieve the desired transformations.
- Cooling Rate: The cooling rate, especially after quenching, is critical. Rapid cooling can increase hardness but may also introduce brittleness. Controlled cooling rates are necessary to balance hardness and toughness.
- Quenching Medium: The choice of quenching medium (oil, water, air) affects the cooling rate and the final properties of the material.
-
Environmental Conditions
- Atmosphere: The atmosphere in which heat treatment occurs (e.g., inert gas, vacuum) can prevent oxidation and other surface reactions that could degrade the material's properties.
- Contamination: Ensuring a clean environment free from contaminants is essential to maintain the integrity of the material.
-
Material Composition
- Alloying Elements: The presence of alloying elements can significantly influence the heat treatment process and the resulting properties. Different elements can alter phase transformation temperatures and kinetics.
- Homogeneity: The material should be homogeneous in composition to ensure consistent properties throughout.
-
Heat Treatment Methods
- Annealing: This process involves heating the material to a specific temperature and then cooling it slowly to relieve internal stresses and increase ductility.
- Quenching: Rapid cooling from a high temperature to increase hardness, often followed by tempering to reduce brittleness.
- Tempering: Heating the quenched material to a lower temperature to reduce brittleness while maintaining hardness.
- Case Hardening: A process that hardens the surface of the material while keeping the core soft and tough.
-
Desired Mechanical Properties
- Hardness: The ability of the material to resist deformation and wear.
- Toughness: The ability to absorb energy and plastically deform without fracturing.
- Ductility: The ability to deform under tensile stress, often measured by elongation before fracture.
Understanding and controlling these basic characteristics requirements in heat treatment are essential for achieving the desired mechanical properties and ensuring the material performs as intended in its application.
Summary Table:
Key Factor | Description |
---|---|
Temperature Control | Precise, uniform heating with continuous monitoring to ensure phase transformations. |
Heating/Cooling Rates | Controlled rates to balance hardness and toughness; choice of quenching medium is critical. |
Environmental Conditions | Clean atmosphere (e.g., inert gas, vacuum) to prevent oxidation and contamination. |
Material Composition | Homogeneous composition with alloying elements influencing transformation properties. |
Heat Treatment Methods | Annealing, quenching, tempering, and case hardening for specific property outcomes. |
Mechanical Properties | Hardness, toughness, and ductility tailored for material performance. |
Need expert advice on optimizing your heat treatment process? Contact us today to achieve the best results for your materials!