Deposition coatings are essential in various industries for enhancing the surface properties of materials, such as improving wear resistance, corrosion resistance, and aesthetic appeal. These coatings are applied through different techniques, each suited to specific applications and material requirements. The main types of deposition coatings include physical vapor deposition (PVD), chemical vapor deposition (CVD), electroplating, thermal spray coating, and atomic layer deposition (ALD). Each method has unique characteristics, advantages, and limitations, making them suitable for different industrial applications. Understanding these types helps in selecting the right coating method based on the desired properties and operational conditions.
Key Points Explained:
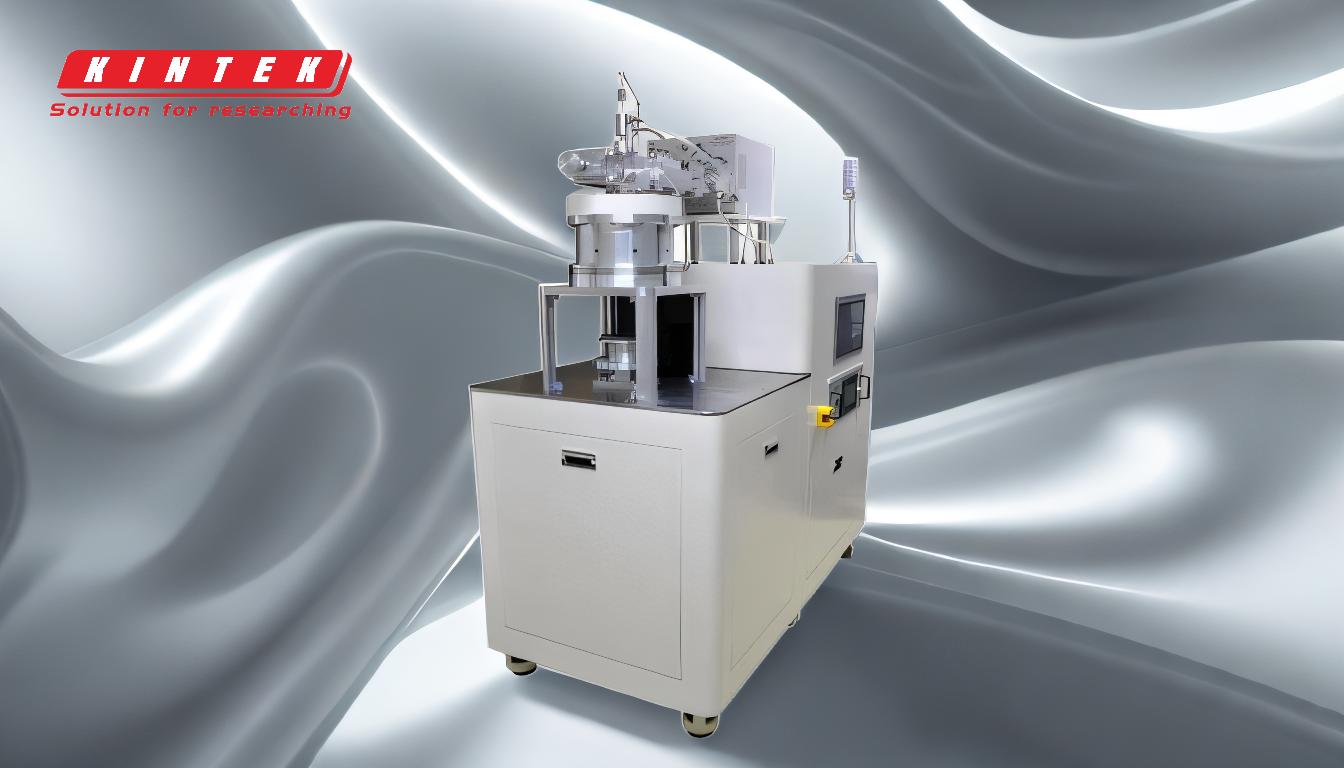
-
Physical Vapor Deposition (PVD)
- Process: PVD involves the vaporization of a solid material in a vacuum environment, which then condenses on the substrate to form a thin film.
- Types: Common PVD techniques include sputtering, evaporation, and ion plating.
- Applications: Widely used in the aerospace, automotive, and tooling industries for coatings that improve hardness, wear resistance, and thermal stability.
- Advantages: Produces high-purity, dense coatings with excellent adhesion and minimal environmental impact.
- Limitations: Requires high vacuum conditions, which can be costly and complex.
-
Chemical Vapor Deposition (CVD)
- Process: CVD involves the chemical reaction of gaseous precursors on the substrate surface to form a solid coating.
- Types: Includes atmospheric pressure CVD, low-pressure CVD, and plasma-enhanced CVD.
- Applications: Used in semiconductor manufacturing, optics, and protective coatings for high-temperature applications.
- Advantages: Can produce uniform coatings over complex geometries and large areas.
- Limitations: Often requires high temperatures and can produce hazardous by-products.
-
Electroplating
- Process: Electroplating uses an electric current to reduce dissolved metal cations, forming a coherent metal coating on the substrate.
- Applications: Common in automotive, electronics, and jewelry industries for decorative finishes and corrosion protection.
- Advantages: Relatively low cost and ability to coat a wide range of metals.
- Limitations: Environmental concerns due to the use of toxic chemicals and waste disposal issues.
-
Thermal Spray Coating
- Process: Involves melting or heating coating material and spraying it onto the substrate.
- Types: Includes flame spraying, arc spraying, plasma spraying, and high-velocity oxy-fuel (HVOF) spraying.
- Applications: Used in aerospace, energy, and heavy machinery for coatings that provide thermal insulation, wear resistance, and corrosion protection.
- Advantages: Can apply thick coatings and repair worn-out parts.
- Limitations: Coating adhesion can be variable, and the process may introduce porosity.
-
Atomic Layer Deposition (ALD)
- Process: ALD is a vapor-phase technique that creates thin films by sequentially exposing the substrate to different precursors.
- Applications: Primarily used in microelectronics, photovoltaics, and nanotechnology for ultra-thin, uniform coatings.
- Advantages: Excellent control over film thickness and composition at the atomic level.
- Limitations: Slow deposition rates and high costs, limiting its use to high-value applications.
Understanding these deposition coating methods allows for informed decision-making in selecting the appropriate technique based on the specific requirements of the application, such as the type of substrate, desired coating properties, and operational conditions. Each method offers distinct advantages and challenges, making them suitable for different industrial needs.
Summary Table:
Type | Process | Applications | Advantages | Limitations |
---|---|---|---|---|
Physical Vapor Deposition (PVD) | Vaporization of solid material in a vacuum, condensing on substrate. | Aerospace, automotive, tooling for hardness, wear resistance, thermal stability. | High-purity, dense coatings; excellent adhesion; minimal environmental impact. | High vacuum conditions; costly and complex setup. |
Chemical Vapor Deposition (CVD) | Chemical reaction of gaseous precursors on substrate. | Semiconductor, optics, high-temperature protective coatings. | Uniform coatings over complex geometries; large-area coverage. | High temperatures; hazardous by-products. |
Electroplating | Electric current reduces metal cations, forming a metal coating. | Automotive, electronics, jewelry for decorative finishes, corrosion protection. | Low cost; wide range of metals. | Toxic chemicals; environmental concerns. |
Thermal Spray Coating | Melting/heating material and spraying onto substrate. | Aerospace, energy, heavy machinery for thermal insulation, wear, corrosion. | Thick coatings; repair capabilities. | Variable adhesion; porosity in coatings. |
Atomic Layer Deposition (ALD) | Sequential exposure to precursors for ultra-thin films. | Microelectronics, photovoltaics, nanotechnology. | Atomic-level control of thickness and composition. | Slow deposition rates; high costs. |
Need help selecting the right deposition coating for your application? Contact our experts today!