Heat treatment furnaces, while essential for various industrial processes, come with several disadvantages that can impact their efficiency, cost, and operational effectiveness. These include challenges related to temperature control, labor intensity, energy consumption, and specific operational constraints depending on the type of furnace. Understanding these drawbacks is crucial for making informed decisions when selecting and operating heat treatment furnaces.
Key Points Explained:
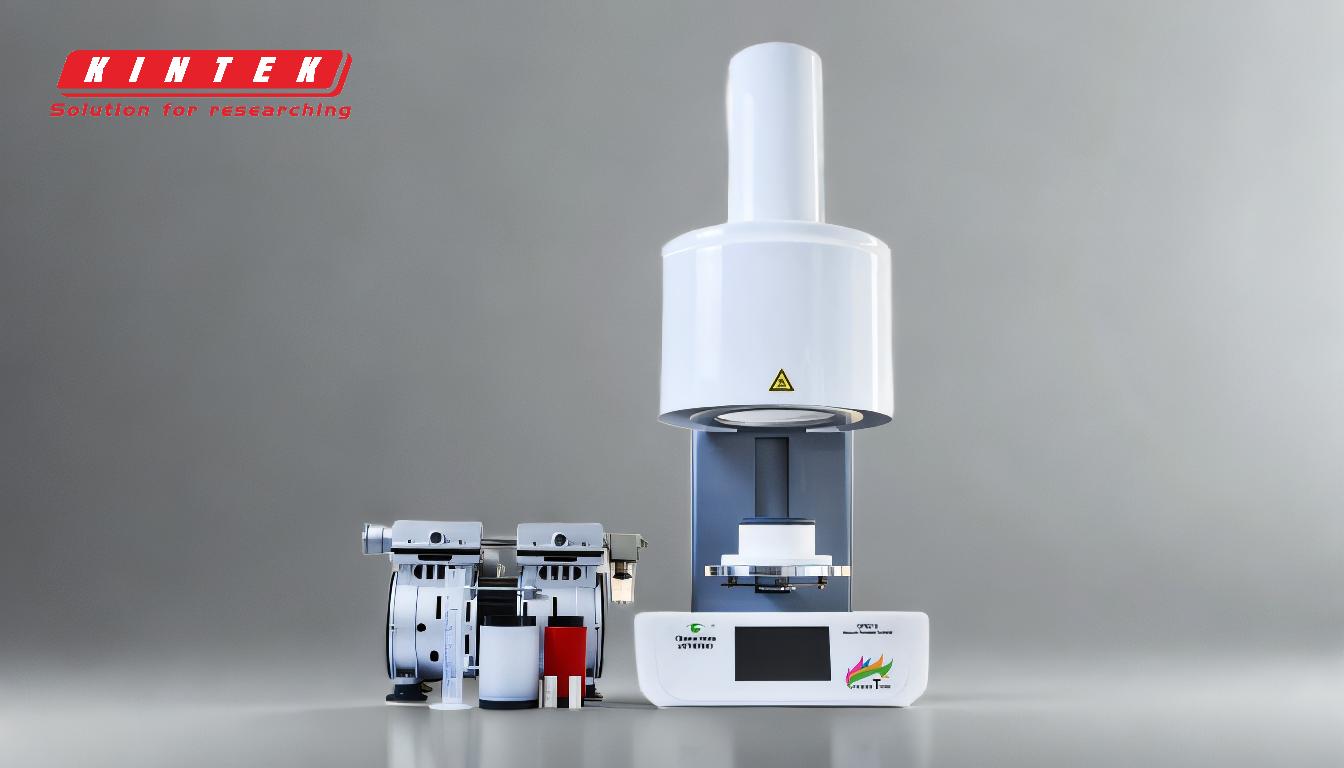
-
Poor Temperature Control:
- Many heat treatment furnaces, especially those using coal or liquid fuels, struggle with maintaining uniform temperature distribution within the chamber. This can lead to inconsistent heat treatment results, affecting the quality of the final product. For example, coal-based furnaces often have poor temperature control, which can result in uneven heating and potential defects in the treated materials.
-
Labor-Intensive Operation:
- Certain types of furnaces, such as batch furnaces, require significant manual labor for loading and unloading materials. This not only increases operational costs but also reduces overall productivity. Batch furnaces, for instance, need fixtures like baskets or racks to group parts together, and the parts closest to the heat source will heat faster, leading to uneven heating of the entire load.
-
High Energy Consumption:
- The energy efficiency of heat treatment furnaces can be a concern. For example, batch furnaces require heating not only the parts but also the carts or baskets used to hold them, which increases the overall heat load and energy consumption. Similarly, muffle furnaces take longer to reach the desired temperature compared to open-flame methods, making them less energy-efficient for projects requiring quick warm-ups.
-
Operational Constraints:
- Different types of furnaces come with specific operational challenges. Induction furnaces, for instance, lack refining capacity, requiring charge materials to be free of oxides and of a known composition. Some alloying elements may be lost due to oxidation, necessitating their re-addition to the melt. Controlled atmosphere heat treatment furnaces have high sealing requirements and need specialized components like anti-carburizing bricks and large-section resistor boards, adding to the complexity and cost of operation.
-
Maintenance and Equipment Costs:
- The maintenance and initial equipment costs for some furnaces can be prohibitively high. Hot press sintering furnaces, for example, require professional operation and maintenance, and ensuring uniformity and stability of pressure during the process is crucial to avoid product defects. Additionally, the high sealing requirements and specialized components of controlled atmosphere furnaces contribute to their higher costs.
-
Storage and Handling Issues:
- The storage and handling of materials used in heat treatment furnaces can pose challenges. Coal-based furnaces, for instance, require proper grade coal for effective use, and storing coal can be problematic due to its bulk and potential for smoke issues. Liquid fuels, on the other hand, thicken in winter, requiring special warming of pipelines to ensure smooth operation.
-
Design Limitations:
- The design of certain furnaces can limit their accessibility and ease of use. Muffle furnaces, for example, have a design that makes it harder to access the interior, requiring careful material placement during use. This can slow down the process and make it less ideal for projects requiring quick warm-ups.
In summary, while heat treatment furnaces are indispensable for various industrial applications, they come with several disadvantages that need to be carefully considered. These include issues related to temperature control, labor intensity, energy consumption, operational constraints, maintenance costs, storage and handling, and design limitations. Understanding these drawbacks can help in selecting the right furnace for specific applications and in optimizing their operation to mitigate these challenges.
Summary Table:
Disadvantage | Description |
---|---|
Poor Temperature Control | Uneven heating and inconsistent results, especially in coal or liquid fuel-based furnaces. |
Labor-Intensive Operation | Manual loading/unloading in batch furnaces increases costs and reduces productivity. |
High Energy Consumption | Increased heat load and energy use, particularly in batch and muffle furnaces. |
Operational Constraints | Specific challenges like refining capacity, oxidation, and sealing requirements. |
Maintenance and Equipment Costs | High costs for professional operation, maintenance, and specialized components. |
Storage and Handling Issues | Challenges with coal storage, liquid fuel thickening, and material handling. |
Design Limitations | Limited accessibility and slower processes, especially in muffle furnaces. |
Need help selecting the right heat treatment furnace? Contact our experts today for tailored solutions!