Corrosion control is essential to prolong the lifespan of metals and prevent structural failures. Two primary methods of controlling corrosion include protective coatings and plating and cathodic protection. Protective coatings and plating involve applying a barrier layer to the metal surface to prevent exposure to corrosive elements. Cathodic protection, on the other hand, uses electrochemical principles to make the metal the cathode of an electrochemical cell, thereby preventing oxidation. Both methods are highly effective in mitigating corrosion, depending on the environment and the type of metal involved.
Key Points Explained:
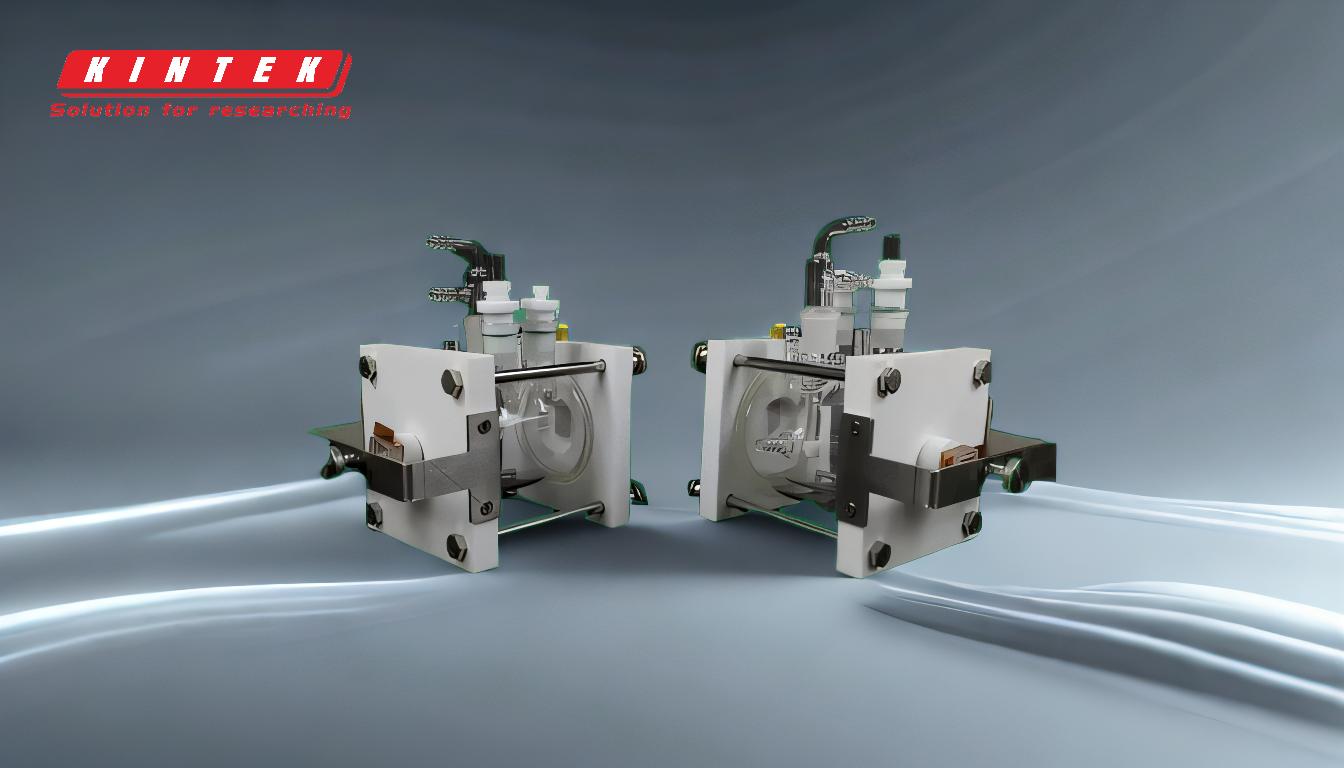
-
Protective Coatings and Plating
- Purpose: To create a physical barrier between the metal and its corrosive environment.
-
Types of Coatings:
- Paints and Polymers: Applied as a thin layer to shield the metal from moisture, oxygen, and other corrosive agents.
- Metallic Plating: Involves depositing a layer of a more corrosion-resistant metal (e.g., zinc, chromium, or nickel) onto the surface of the base metal.
- Anodizing: Commonly used for aluminum, where an oxide layer is formed on the surface to enhance corrosion resistance.
-
Advantages:
- Cost-effective and versatile for a wide range of applications.
- Can be tailored to specific environmental conditions.
-
Limitations:
- Coatings can degrade over time due to wear, UV exposure, or chemical attack.
- Requires regular maintenance and reapplication.
-
Cathodic Protection
- Purpose: To prevent corrosion by making the metal the cathode in an electrochemical cell, thereby suppressing oxidation.
-
Types of Cathodic Protection:
- Sacrificial Anode Method: Uses a more reactive metal (e.g., zinc or magnesium) as an anode, which corrodes preferentially, protecting the base metal.
- Impressed Current Method: Uses an external power source to supply a continuous current, forcing the metal to act as the cathode.
-
Advantages:
- Highly effective for large structures like pipelines, ships, and offshore platforms.
- Long-lasting protection with minimal maintenance.
-
Limitations:
- Requires careful design and monitoring to ensure effectiveness.
- Sacrificial anodes need periodic replacement.
-
Environmental Modification
- While not explicitly mentioned in the question, modifying the environment is another indirect method of corrosion control.
-
Examples:
- Reducing humidity or controlling temperature in storage areas.
- Using corrosion inhibitors in liquids that come into contact with the metal.
-
Advantages:
- Can complement other corrosion control methods.
-
Limitations:
- Often impractical for large or outdoor structures.
-
Selection Criteria for Corrosion Control Methods
- Type of Metal: Some metals (e.g., steel) are more prone to corrosion and may require more robust protection.
- Environmental Conditions: Harsh environments (e.g., marine or industrial settings) may necessitate combined methods.
- Cost and Maintenance: Protective coatings are generally cheaper but require more frequent upkeep, while cathodic protection is costlier upfront but offers long-term benefits.
By understanding these methods and their applications, equipment and consumable purchasers can make informed decisions to effectively combat corrosion in their specific use cases.
Summary Table:
Method | Purpose | Advantages | Limitations |
---|---|---|---|
Protective Coatings | Create a barrier to prevent exposure to corrosive elements. | Cost-effective, versatile, and customizable. | Requires maintenance; can degrade over time. |
Cathodic Protection | Make the metal the cathode to prevent oxidation. | Long-lasting; ideal for large structures. | Requires design expertise; sacrificial anodes need replacement. |
Environmental Mods | Indirectly reduce corrosion by altering the environment. | Complements other methods. | Often impractical for large or outdoor structures. |
Need help choosing the right corrosion control method for your metals? Contact us today for expert advice!