Heat in a hydraulic system can lead to several negative effects, including reduced efficiency, increased wear and tear on components, and potential system failure. Excessive heat can degrade hydraulic fluid, cause seals and hoses to deteriorate, and lead to thermal expansion, which can misalign components. Additionally, high temperatures can reduce the viscosity of the hydraulic fluid, leading to inadequate lubrication and increased friction. Overheating can also cause the system to operate outside its designed parameters, resulting in reduced performance and potential safety hazards. Proper thermal management and regular maintenance are essential to mitigate these issues.
Key Points Explained:
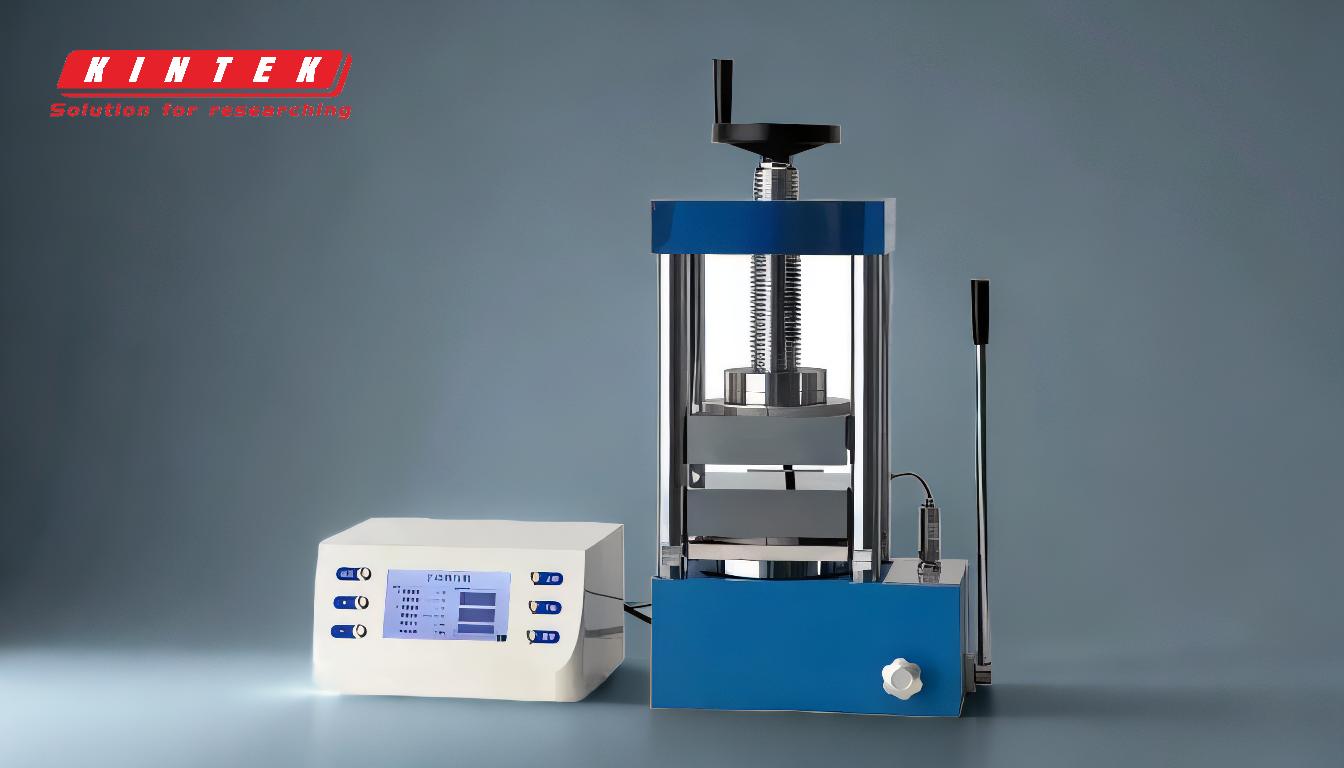
-
Reduced Efficiency:
- Excessive heat in a hydraulic system can lead to a decrease in overall efficiency. As the temperature rises, the hydraulic fluid's viscosity decreases, making it less effective at transferring power. This results in the system requiring more energy to perform the same tasks, leading to higher operational costs and reduced performance.
-
Increased Wear and Tear:
- High temperatures accelerate the wear and tear of hydraulic components. Seals, hoses, and other elastomeric materials can degrade more quickly when exposed to excessive heat, leading to leaks and potential system failures. Metal components can also suffer from thermal fatigue, reducing their lifespan and reliability.
-
Degradation of Hydraulic Fluid:
- Heat causes hydraulic fluid to break down more rapidly, leading to the formation of sludge and varnish. These contaminants can clog filters, valves, and other critical components, reducing the system's efficiency and increasing the risk of failure. The degradation of hydraulic fluid also reduces its ability to lubricate and protect components, further exacerbating wear and tear.
-
Thermal Expansion:
- Components in a hydraulic system can expand when exposed to high temperatures, leading to misalignment and increased stress on the system. This can cause parts to warp or become damaged, resulting in leaks, reduced performance, and potential system failure. Thermal expansion can also lead to increased clearances between moving parts, reducing the system's efficiency and increasing the risk of component failure.
-
Inadequate Lubrication:
- As the temperature of the hydraulic fluid increases, its viscosity decreases, reducing its ability to provide adequate lubrication to moving parts. This can lead to increased friction, wear, and heat generation, creating a vicious cycle that further exacerbates the problem. Inadequate lubrication can also cause components to seize or fail prematurely.
-
Safety Hazards:
- Overheating in a hydraulic system can pose significant safety risks. High temperatures can cause hydraulic fluid to ignite, leading to fires or explosions. Additionally, the failure of critical components due to overheating can result in uncontrolled movements or releases of pressure, posing a danger to operators and equipment.
-
Reduced Performance:
- When a hydraulic system operates at elevated temperatures, it may not perform as intended. Components may not function correctly, and the system may not be able to generate the required pressure or flow rates. This can lead to reduced productivity, increased downtime, and higher maintenance costs.
-
Thermal Management and Maintenance:
- Proper thermal management is essential to prevent the negative effects of heat in a hydraulic system. This includes using heat exchangers, coolers, and proper ventilation to maintain optimal operating temperatures. Regular maintenance, such as checking fluid levels, replacing worn components, and monitoring system temperature, is also crucial to ensure the system operates efficiently and safely.
In summary, excessive heat in a hydraulic system can lead to a range of negative effects, including reduced efficiency, increased wear and tear, fluid degradation, thermal expansion, inadequate lubrication, safety hazards, and reduced performance. Implementing effective thermal management strategies and conducting regular maintenance are essential to mitigate these issues and ensure the system operates reliably and efficiently.
Summary Table:
Effect | Description |
---|---|
Reduced Efficiency | Decreased hydraulic fluid viscosity reduces power transfer, increasing energy costs. |
Increased Wear and Tear | High temperatures degrade seals, hoses, and metal components, leading to failures. |
Fluid Degradation | Heat breaks down hydraulic fluid, forming sludge and varnish that clogs components. |
Thermal Expansion | Components expand, causing misalignment, leaks, and reduced system performance. |
Inadequate Lubrication | Reduced fluid viscosity leads to increased friction, wear, and potential failures. |
Safety Hazards | Overheating can cause fires, explosions, or uncontrolled pressure releases. |
Reduced Performance | Elevated temperatures cause components to malfunction, reducing productivity. |
Thermal Management | Use heat exchangers, coolers, and regular maintenance to mitigate overheating risks. |
Ensure your hydraulic system operates safely and efficiently—contact our experts today for thermal management solutions!