The MOCVD (Metal-Organic Chemical Vapor Deposition) process is a specialized technique used for growing high-quality thin films and epitaxial layers, particularly in semiconductor manufacturing. It involves a series of well-defined steps, including precursor selection, gas delivery, deposition, and by-product removal. The process is highly reproducible and allows for precise control over layer composition and thickness, making it ideal for applications in optoelectronics and advanced materials. Below is a detailed breakdown of the MOCVD process steps.
Key Points Explained:
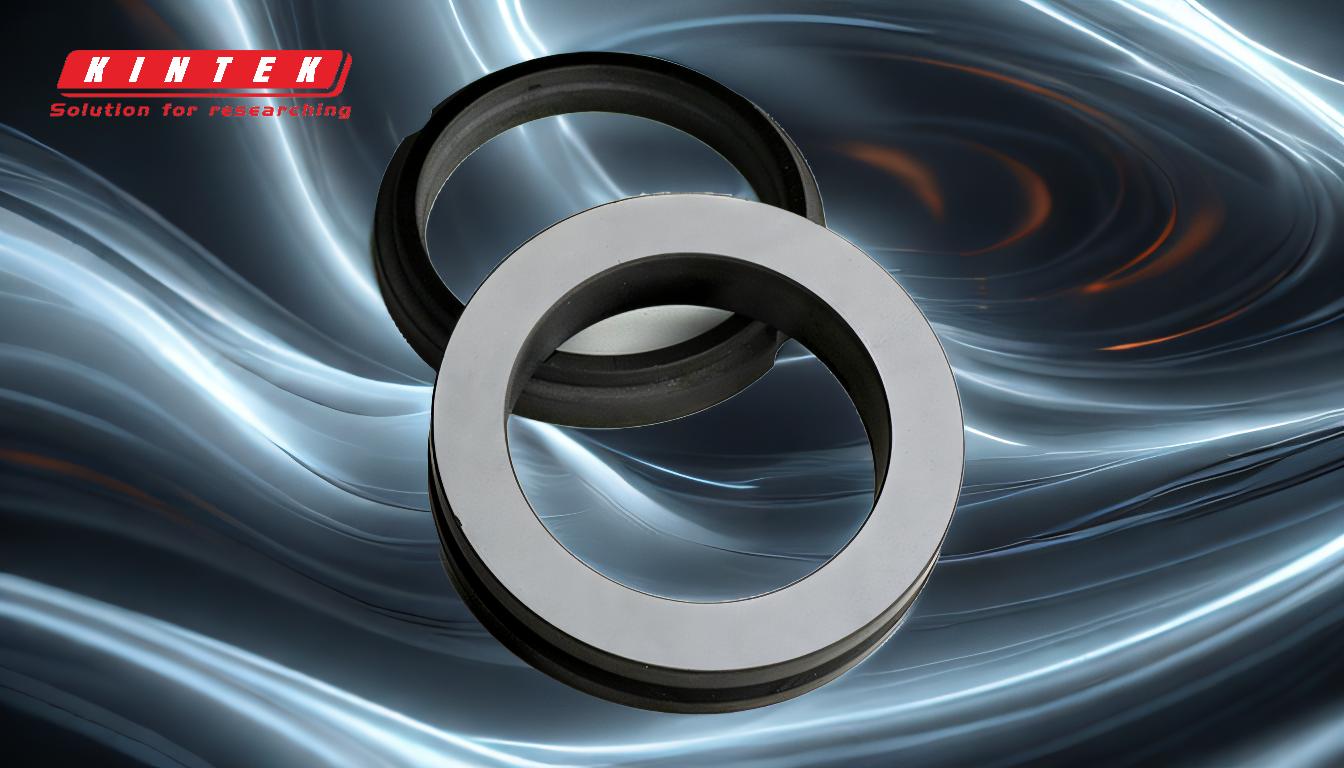
-
Precursor Selection and Input
- The process begins with selecting appropriate metal-organic (MO) precursors and reaction gases. These precursors are typically volatile organometallic compounds, such as trimethylgallium (TMGa) or trimethylaluminum (TMAl), which provide the necessary metal atoms for the deposition.
- The selection of precursors is critical as they determine the composition and properties of the final deposited material. Precursors must be chosen based on their reactivity, volatility, and compatibility with the desired material system.
-
Gas Delivery and Mixing
- The selected precursors and reactive gases are introduced into the reaction chamber through a gas delivery system. This system ensures precise control over the flow rates and concentrations of the gases.
- The gases are mixed at the inlet of the reaction chamber to create a homogeneous mixture. Proper mixing is essential to achieve uniform deposition across the substrate.
-
Deposition Reaction
- The mixed gases flow onto a heated substrate, which is typically maintained at high temperatures (600°C to 800°C). The heat causes the precursors to decompose and react chemically, forming the desired solid material on the substrate surface.
- The deposition reaction is highly dependent on temperature, pressure, and gas flow rates. These parameters must be carefully controlled to ensure the desired material properties and growth rates.
-
Emission of By-products and Unreacted Precursors
- During the deposition process, volatile by-products and unreacted precursors are generated. These by-products are carried away by the gas flow and removed from the reaction chamber.
- Efficient removal of by-products is crucial to prevent contamination and ensure the quality of the deposited material.
-
Bubbler Vaporization and Concentration Control
- In some MOCVD systems, bubbler vaporization is used to control the concentration of MO sources. A portion of the MO source is carried out of the source vial with a carrier gas stream and flows into the reaction chamber.
- Precise control of the MO source concentration is essential for reproducibility and process efficiency. This requires accurate regulation of gas flow, temperature, and pressure.
-
Substrate Preparation and Temperature Control
- Before deposition, the substrate is prepared by thermal dehydration to remove moisture and oxygen impurities. The substrate is then heated to high temperatures (1000°C to 1100°C) to prepare the surface chemistry and etch passivation.
- Substrate temperature control is critical during both the deposition and cooling phases. Proper cooling, which typically takes 20-30 minutes, ensures the stability and quality of the deposited layer.
-
Purging Residual Gas
- After the deposition process, residual gases are purged from the reaction chamber to prevent contamination and prepare the system for the next cycle.
- Purging is an essential step to maintain the cleanliness and efficiency of the MOCVD system.
By following these steps, the MOCVD process enables the growth of high-quality thin films with precise control over composition, thickness, and uniformity. This makes it a cornerstone technology in the fabrication of advanced semiconductor devices, LEDs, and other optoelectronic components.
Summary Table:
Step | Description |
---|---|
1. Precursor Selection | Choose metal-organic precursors (e.g., TMGa, TMAl) based on reactivity and compatibility. |
2. Gas Delivery and Mixing | Introduce and mix precursors and gases in the reaction chamber for uniform deposition. |
3. Deposition Reaction | Heat substrate to 600°C–800°C for chemical decomposition and material formation. |
4. By-product Removal | Remove volatile by-products and unreacted precursors to ensure material quality. |
5. Bubbler Vaporization | Control MO source concentration using bubbler vaporization for reproducibility. |
6. Substrate Preparation | Dehydrate and heat substrate to 1000°C–1100°C for surface chemistry preparation. |
7. Purging Residual Gas | Purge residual gases post-deposition to maintain system cleanliness. |
Ready to optimize your MOCVD process? Contact our experts today for tailored solutions!