Temperature sensors are critical components in furnaces, ensuring precise temperature control and monitoring for optimal performance. The primary types of temperature sensors used in furnaces include thermocouples, Resistance Temperature Detectors (RTDs), and Infrared (IR) sensors. Thermocouples are favored for their durability and ability to withstand high temperatures, while RTDs are chosen for their high accuracy and stability. IR sensors, on the other hand, offer fast response times and non-contact temperature measurement. Each type of sensor has specific applications and advantages, making them suitable for different furnace environments and requirements.
Key Points Explained:
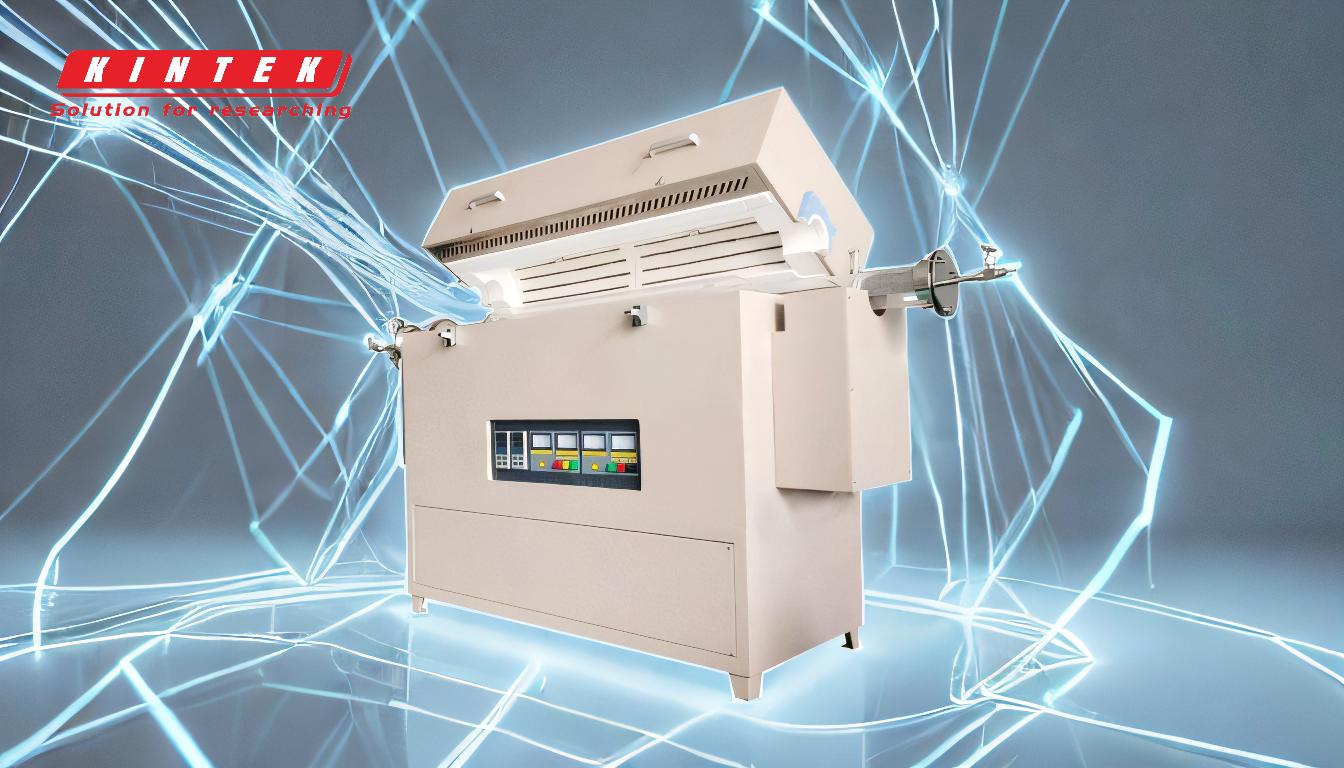
-
Thermocouples
- Description: Thermocouples are widely used in furnaces due to their durability and ability to operate at high temperatures. They consist of two dissimilar metal wires joined at one end, generating a voltage proportional to the temperature difference between the junction and the other end.
-
Types: Common types include Type K, Type S, Type R, and Type B, each suited for specific temperature ranges and environmental conditions.
- Type K: Suitable for a wide temperature range (-200°C to 1260°C) and commonly used in oxidizing or inert atmospheres.
- Type S, R, and B: Ideal for high-temperature applications (up to 1700°C) and often used in controlled atmospheres.
- Applications: Thermocouples are used in electric melting furnaces, atmosphere-controlled furnaces, and for monitoring specific furnace zones (e.g., hottest and coldest spots).
- Advantages: High-temperature resistance, durability, and cost-effectiveness.
-
Resistance Temperature Detectors (RTDs)
- Description: RTDs measure temperature by correlating the resistance of a metal (usually platinum) with temperature. They are known for their high accuracy and stability over time.
- Temperature Range: Typically used for lower to moderate temperature ranges (-200°C to 600°C).
- Applications: RTDs are ideal for applications requiring precise temperature control, such as laboratory furnaces or processes where stability is critical.
- Advantages: High accuracy, stability, and repeatability.
-
Infrared (IR) Sensors
- Description: IR sensors measure temperature by detecting the infrared energy emitted by an object. They are non-contact sensors, making them suitable for measuring temperature from a distance.
- Temperature Range: Can measure a wide range of temperatures, depending on the specific sensor.
- Applications: IR sensors are used in furnaces where fast response times are required or where physical contact with the object is not feasible.
- Advantages: Fast response times, non-contact measurement, and ability to measure moving or hazardous objects.
-
Monitoring and Control Systems
- Control Thermocouples: These are the primary sensors used to monitor and regulate furnace temperature. They provide real-time feedback to the control system, which adjusts heating power to maintain the desired temperature.
- Load Thermocouples: Used to simulate the temperature of the parts being heated, ensuring accurate temperature control for the load.
- Temperature Uniformity Surveys: Conducted to identify the hottest and coldest spots in the furnace, ensuring consistent temperature distribution.
- System Accuracy Tests: Regularly performed to verify the accuracy of temperature readings and overall furnace performance.
-
Selection Criteria for Temperature Sensors
- Temperature Range: Choose a sensor that can operate within the required temperature range of the furnace.
- Accuracy and Stability: For precise control, RTDs are preferred, while thermocouples are better for high-temperature applications.
- Response Time: IR sensors are ideal for fast response requirements.
- Environmental Conditions: Consider factors such as oxidizing or reducing atmospheres, vibration, and physical space constraints.
- Cost and Durability: Thermocouples are cost-effective and durable, while RTDs and IR sensors may have higher upfront costs but offer specific advantages.
-
Integration with Furnace Control Systems
- Real-Time Monitoring: Temperature sensors provide real-time data to the furnace control system, enabling precise adjustments to heating power.
- Feedback Loop: The control circuit uses temperature and atmosphere control signals to calculate the required heating power, ensuring optimal furnace performance.
- Automation: Modern furnaces often integrate temperature sensors with automated control systems for improved efficiency and consistency.
By understanding the different types of temperature sensors and their applications, furnace operators can select the most suitable sensor for their specific needs, ensuring accurate temperature control and optimal furnace performance.
Summary Table:
Sensor Type | Key Features | Applications | Advantages |
---|---|---|---|
Thermocouples | Durable, high-temperature resistance, cost-effective | Electric melting furnaces, atmosphere-controlled furnaces, zone monitoring | High-temperature resistance, durability, cost-effectiveness |
RTDs | High accuracy, stability, repeatability | Laboratory furnaces, processes requiring precise control | High accuracy, stability, repeatability |
IR Sensors | Fast response, non-contact measurement | Fast response requirements, hazardous or moving objects | Fast response times, non-contact measurement |
Need help selecting the right temperature sensor for your furnace? Contact our experts today for tailored solutions!