Furnaces are categorized based on their application, heating method, and design, making it essential to understand the distinctions between them. Broadly, furnaces can be classified into three main types: household furnaces, industrial furnaces, and laboratory furnaces. Each type serves a specific purpose and operates under different conditions. Household furnaces are designed for residential heating, industrial furnaces are used in manufacturing and processing, and laboratory furnaces are tailored for scientific research and experimentation. Within these categories, further subdivisions exist based on the heating method, such as gas, electric, oil, or specialized designs like tube, box, or muffle furnaces.
Key Points Explained:
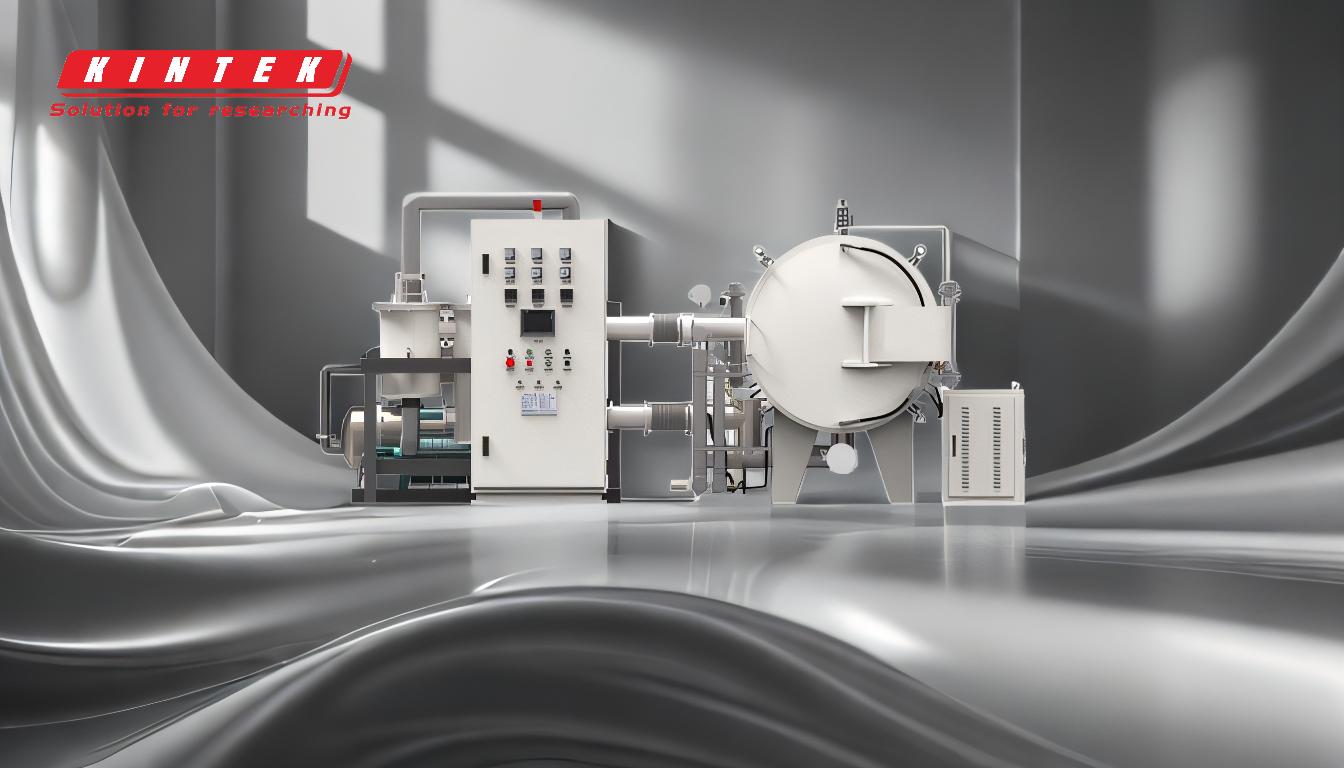
-
Household Furnaces
- Purpose: Designed for residential heating, household furnaces are the most common type used in homes.
-
Heating Methods:
- Natural Gas Furnaces: These are cost-effective and widely used due to the availability of natural gas. They are efficient and provide consistent heating.
- Oil Furnaces: These are used in areas where natural gas is not available. They require an oil storage tank and are less efficient than gas furnaces.
- Electric Furnaces: These are cleaner and easier to install but are less energy-efficient and more expensive to operate compared to gas or oil furnaces.
- Key Considerations: When choosing a household furnace, factors like energy efficiency, fuel availability, and installation costs are critical.
-
Industrial Furnaces
- Purpose: Used in manufacturing, processing, and large-scale production, industrial furnaces are designed to handle high temperatures and heavy workloads.
-
Heating Methods:
- Gas Furnaces: Commonly used in industries due to their high efficiency and ability to reach extremely high temperatures.
- Electric Furnaces: Include arc furnaces (used in steel production) and induction furnaces (used for melting metals). These are preferred for their precision and cleanliness.
- Oil Furnaces: Less common in modern industries but still used in specific applications where gas or electricity is not feasible.
-
Specialized Designs:
- Rotary Furnaces: Used for continuous processing of materials.
- Pusher Furnaces: Ideal for heat treatment of metal parts.
- Vacuum Furnaces: Used in processes requiring a controlled atmosphere.
- Key Considerations: Industrial furnaces are chosen based on the specific application, required temperature range, and production scale.
-
Laboratory Furnaces
- Purpose: Designed for scientific research, testing, and experimentation, laboratory furnaces operate under precise conditions.
-
Heating Methods:
- Tube Furnaces: Used for heating small samples in a controlled environment. They are ideal for materials testing and chemical reactions.
- Box Furnaces: Provide uniform heating for larger samples and are commonly used in material science and metallurgy.
- Muffle Furnaces: Designed to isolate samples from combustion gases, making them suitable for high-temperature applications like ashing or sintering.
- Key Considerations: Laboratory furnaces are selected based on temperature range, sample size, and the need for precise control over the heating environment.
Additional Insights:
- Overlap in Categories: Some furnaces, like electric arc furnaces, can be used in both industrial and laboratory settings, depending on the scale and purpose.
- Emerging Technologies: Modern advancements, such as induction and resistance furnaces, are expanding the capabilities of both industrial and laboratory furnaces.
- Environmental Impact: Electric and gas furnaces are generally more environmentally friendly compared to oil furnaces, which produce more emissions.
By understanding these categories and their specific applications, purchasers can make informed decisions based on their needs, whether for residential heating, industrial production, or scientific research.
Summary Table:
Furnace Type | Purpose | Heating Methods | Key Considerations |
---|---|---|---|
Household Furnaces | Residential heating | Natural Gas, Oil, Electric | Energy efficiency, fuel availability, installation costs |
Industrial Furnaces | Manufacturing & large-scale production | Gas, Electric (Arc, Induction), Oil | Application, temperature range, production scale |
Laboratory Furnaces | Scientific research & experimentation | Tube, Box, Muffle | Temperature range, sample size, precise control |
Need help choosing the right furnace for your needs? Contact our experts today for personalized advice!