Hot-pressing is a manufacturing process that combines heat and pressure to shape, densify, or bond materials, often used in industries like ceramics, composites, and metallurgy. It involves placing materials in a mold or between plates and applying high temperature and pressure simultaneously to achieve desired properties such as improved strength, density, or structural integrity. This method is particularly effective for creating complex shapes, reducing porosity, and enhancing material performance. A hot press machine is the primary equipment used for this process, offering precise control over temperature, pressure, and time to ensure consistent and high-quality results.
Key Points Explained:
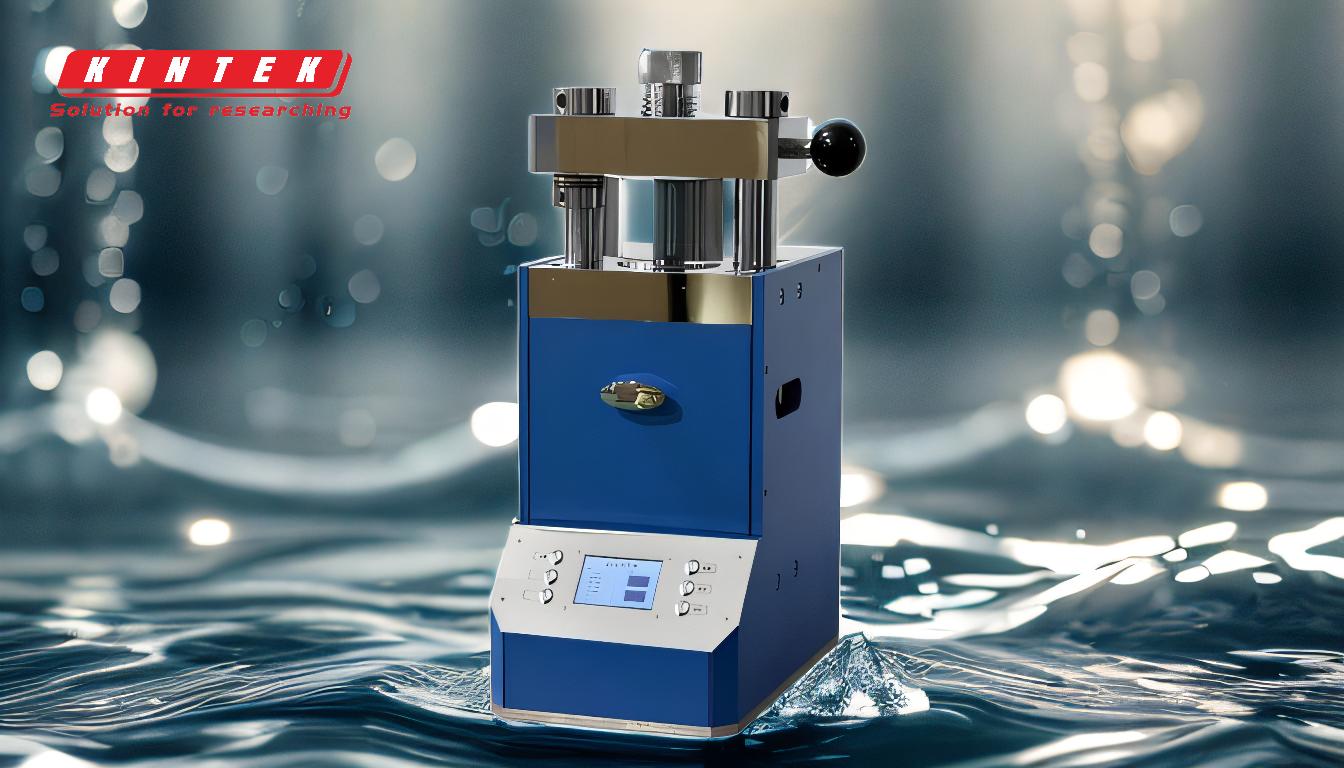
-
Definition and Purpose of Hot-Pressing:
- Hot-pressing is a technique that applies both heat and pressure to materials to achieve specific outcomes like densification, bonding, or shaping.
- It is commonly used to produce materials with high strength, low porosity, and enhanced mechanical properties.
- This process is particularly useful for materials that are difficult to shape or densify using conventional methods.
-
How Hot-Pressing Works:
- Materials are placed in a mold or between heated plates.
- A hot press machine applies controlled heat and pressure simultaneously.
- The combination of heat and pressure causes the material to soften, flow, and bond, resulting in a dense and uniform structure.
- The process parameters (temperature, pressure, and time) are carefully controlled to achieve the desired material properties.
-
Applications of Hot-Pressing:
- Ceramics: Used to produce dense ceramic components with high strength and wear resistance.
- Composites: Helps in bonding layers of different materials to create lightweight, high-strength composites.
- Metallurgy: Used for powder metallurgy to create dense metal parts with minimal porosity.
- Polymers: Enhances the properties of polymer-based materials by improving their density and structural integrity.
-
Advantages of Hot-Pressing:
- Improved Material Properties: Results in materials with higher density, strength, and uniformity.
- Complex Shapes: Enables the production of intricate shapes that are difficult to achieve with other methods.
- Reduced Porosity: Minimizes voids and defects in the final product.
- Efficiency: Combines heating and pressing into a single step, reducing processing time.
-
Equipment: Hot Press Machine:
- A hot press machine is essential for the hot-pressing process.
- It consists of heated plates or molds, a hydraulic or mechanical press, and controls for temperature, pressure, and time.
- Modern machines offer precise control over process parameters, ensuring consistent and high-quality results.
-
Challenges and Considerations:
- Material Selection: Not all materials are suitable for hot-pressing; some may degrade under high temperatures or pressures.
- Process Optimization: Achieving the right balance of temperature, pressure, and time is critical for success.
- Cost: The equipment and energy requirements can be significant, making it less suitable for low-volume production.
-
Future Trends in Hot-Pressing:
- Advanced Materials: Increasing use of hot-pressing for new materials like graphene and advanced ceramics.
- Automation: Integration of automation and AI for better process control and efficiency.
- Sustainability: Development of energy-efficient hot press machines and processes to reduce environmental impact.
By understanding the principles and applications of hot-pressing, manufacturers can leverage this technique to produce high-performance materials and components for various industries. The hot press machine plays a central role in this process, making it a critical investment for businesses aiming to achieve superior material properties and product quality.
Summary Table:
Aspect | Details |
---|---|
Process | Combines heat and pressure to shape, densify, or bond materials. |
Applications | Ceramics, composites, metallurgy, polymers. |
Advantages | Improved strength, reduced porosity, complex shapes, efficiency. |
Equipment | Hot press machine with precise temperature, pressure, and time controls. |
Challenges | Material selection, process optimization, cost considerations. |
Future Trends | Advanced materials, automation, sustainability. |
Ready to enhance your material production? Contact us today to explore hot-pressing solutions!