Sintering is a critical process in materials science and manufacturing, where heat and pressure are applied to a powdered material to form a solid mass without melting it completely. This process is essential for creating high-density, durable products with precise mechanical properties. Sintering is widely used in industries such as 3D printing, metallurgy, ceramics, and dentistry. It involves stages like powder compaction, controlled heating in a sintering furnace, particle diffusion, and cooling, resulting in a cohesive and dense final product. The process is tailored to specific applications, such as achieving optimal density in 3D-printed parts or ensuring the durability of dental restorations.
Key Points Explained:
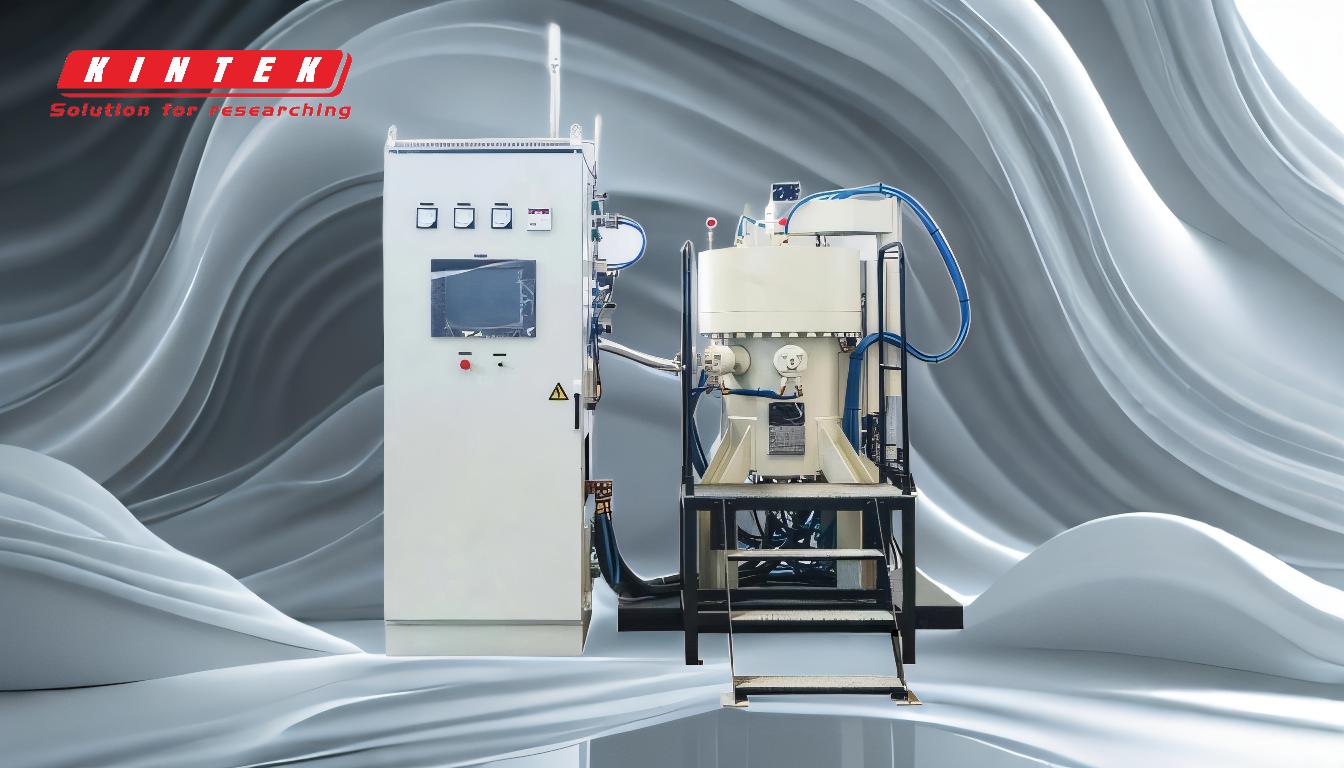
-
Definition and Purpose of Sintering:
- Sintering, also known as 'frittage,' involves heating and compacting powdered materials to form a solid mass without liquefaction.
- The primary purpose is to enhance material density, improve mechanical properties, and create durable, high-performance products.
- It is widely used in industries like 3D printing, metallurgy, ceramics, and dentistry.
-
Stages of the Sintering Process:
- Powder Compaction: The raw material, usually in powder form, is compacted under pressure to ensure uniformity and eliminate voids.
- Controlled Heating: The compacted material is heated in a sintering furnace at controlled temperatures to facilitate particle bonding without complete melting.
- Particle Diffusion and Neck Formation: During heating, atoms diffuse across particle boundaries, forming necks and leading to densification.
- Cooling: The sintered product is cooled to solidify into a rigid and cohesive structure.
-
Applications of Sintering:
- 3D Printing: Sintering is used to achieve high-density (up to 99.5%) and desired mechanical properties in 3D-printed ceramic and metal parts.
- Metallurgy: In ore sintering, heat from burning fuel melts minerals, which then cool and crystallize to form a mesh structure of sintered ore.
- Dentistry: Dental sintering furnaces are used to process restorations like crowns and bridges, ensuring high density and durability.
-
Role of Sintering Furnaces:
- Sintering furnaces are essential for precise temperature control, ensuring optimal particle bonding and material densification.
- In 3D printing, they are used for sintering and debinding to extract carrier materials and achieve final product properties.
- In dentistry, they sinter zirconia to its final hardness, reducing porosity and improving the quality of dental restorations.
-
Temperature Control in Sintering:
- Fine-tuning temperature is crucial to achieving the optimal sintering state.
- Overheating can cause issues like bulging, which can be corrected by lowering the temperature.
- Precise control of temperature, pressure, and atmosphere ensures the quality and stability of the final product.
-
Materials and Preparation:
- The sintering process begins with the preparation of sintering feed, including ingredients and mixing.
- Bottom materials, such as small pieces of sintering ore, are used to protect equipment and improve process efficiency.
-
Benefits of Sintering:
- Enhances material density and mechanical properties.
- Reduces porosity and improves product durability.
- Enables the production of complex shapes and high-performance components.
By understanding the principles and applications of sintering, manufacturers can optimize their processes to produce high-quality, durable products tailored to specific industrial needs.
Summary Table:
Key Aspect | Details |
---|---|
Definition | Heating and compacting powdered materials to form a solid mass without melting. |
Purpose | Enhances density, improves mechanical properties, and creates durable products. |
Stages | Powder compaction, controlled heating, particle diffusion, cooling. |
Applications | 3D printing, metallurgy, ceramics, dentistry. |
Role of Sintering Furnaces | Precise temperature control for optimal particle bonding and densification. |
Benefits | Reduces porosity, improves durability, and enables complex shapes. |
Optimize your sintering process for high-quality results—contact our experts today!