When the sintering temperature is too high, it can lead to a range of issues that negatively impact the quality and performance of the final product. These issues include over-sintering, which results in increased crystallization enthalpy, reduced molecular weight, and degraded material properties such as strength, durability, and translucency. High temperatures can also cause defects like warping, sagging, cracking, and surface imperfections. Additionally, excessive sintering temperatures may lead to uncontrolled phase transformations and reduced stability in materials like zirconia. Adhering to the recommended sintering temperature and time is crucial to achieving optimal mechanical, physical, and aesthetic properties.
Key Points Explained:
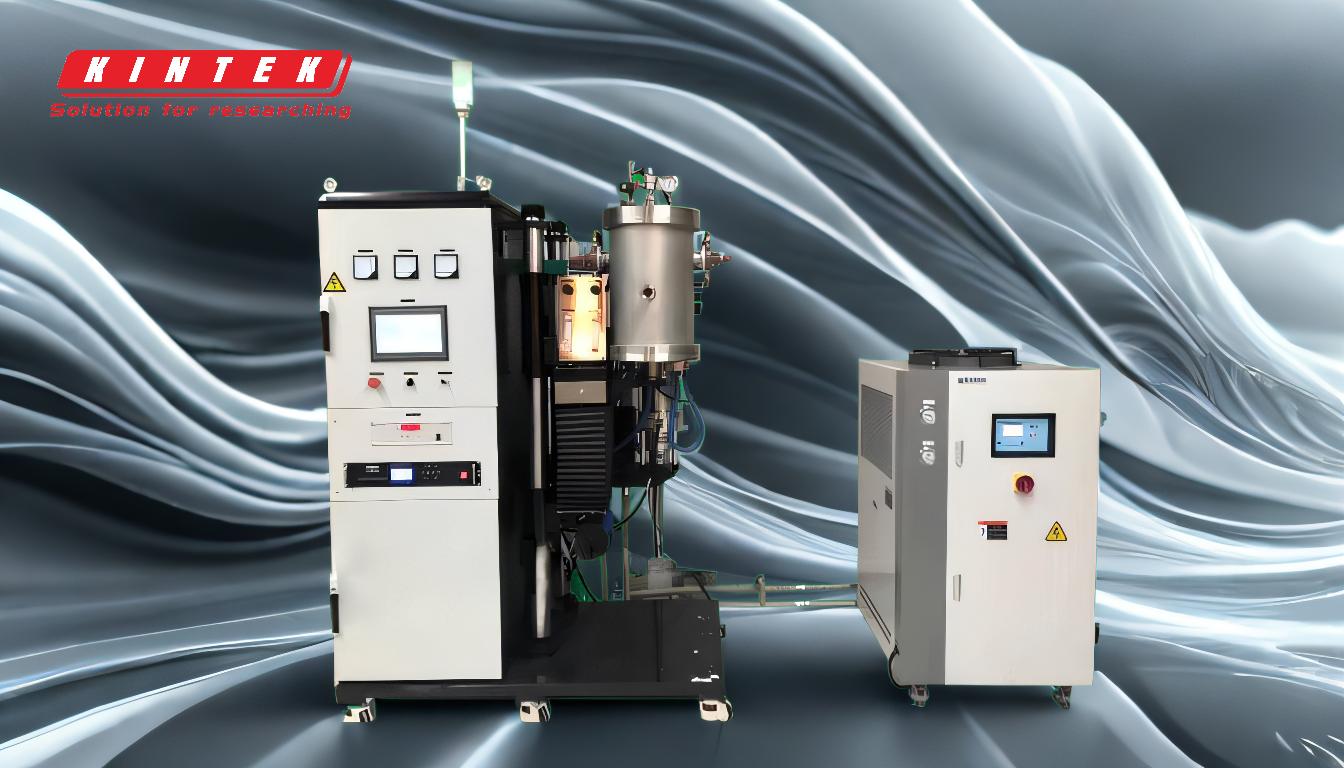
-
Over-Sintering and Material Degradation:
- When the sintering temperature is too high, the material can become over-sintered. This leads to:
- Increased Crystallization Enthalpy: Excessive energy causes the material to crystallize more than intended, altering its microstructure.
- Reduced Molecular Weight: High temperatures can break down molecular chains, weakening the material.
- Degraded Properties: Over-sintering reduces the material's strength, hardness, and durability, making it less suitable for its intended application.
- When the sintering temperature is too high, the material can become over-sintered. This leads to:
-
Defects in the Final Product:
- High sintering temperatures can cause physical defects in the material, including:
- Warping and Sagging: Gravity and friction can deform the material during sintering, leading to uneven shapes or dimensions.
- Cracking: Excessive heat can induce stress within the material, causing it to crack or fracture.
- Surface Imperfections: Issues like blistering (surface defects due to gas discharge) and sweating (liquid phase seeping out) can occur, compromising the material's appearance and functionality.
- High sintering temperatures can cause physical defects in the material, including:
-
Impact on Microstructure:
- The sintering temperature directly influences the material's microstructure, affecting:
- Grain Size: High temperatures can cause grains to grow excessively, reducing the material's strength.
- Pore Size and Distribution: Over-sintering can lead to the collapse or enlargement of pores, impacting density and porosity.
- Grain Boundary Shape: Excessive heat can alter grain boundaries, affecting the material's mechanical properties.
- The sintering temperature directly influences the material's microstructure, affecting:
-
Phase Transformations and Stability:
- In materials like zirconia, high sintering temperatures can lead to:
- Uncontrolled Phase Transformations: Excessive heat can cause uncontrolled changes in the material's crystalline structure, reducing its stability.
- Reduced Translucency: High temperatures can diminish the material's aesthetic properties, such as translucency, which is critical for applications like dental ceramics.
- In materials like zirconia, high sintering temperatures can lead to:
-
Adherence to Manufacturer Recommendations:
- To avoid the negative effects of high sintering temperatures, it is essential to:
- Follow the manufacturer’s recommended sintering schedule, which includes specific temperature and time parameters.
- Ensure that the sintering process is carefully controlled to achieve the desired physical, mechanical, and aesthetic properties.
- To avoid the negative effects of high sintering temperatures, it is essential to:
By understanding these key points, equipment and consumable purchasers can make informed decisions about sintering processes and materials, ensuring high-quality outcomes and minimizing defects.
Summary Table:
Issue | Impact |
---|---|
Over-Sintering | Increased crystallization enthalpy, reduced molecular weight, degraded properties |
Defects | Warping, sagging, cracking, surface imperfections (blistering, sweating) |
Microstructure Changes | Excessive grain growth, pore collapse, altered grain boundaries |
Phase Transformations | Uncontrolled changes, reduced stability, and translucency in zirconia |
Adherence to Recommendations | Ensures optimal mechanical, physical, and aesthetic properties |
Need help optimizing your sintering process? Contact our experts today for tailored solutions!