Tempering is a critical heat treatment process used to enhance the mechanical properties of metals, particularly steel, after they have been hardened. It involves reheating the metal to a temperature below its critical point and then cooling it, which reduces brittleness and internal stresses caused by rapid cooling during quenching. This process improves the material's toughness, ductility, and overall durability, making it more suitable for applications requiring high strength and resistance to cracking. A common example of tempering is the quench and temper process, which is widely used in industries like steel manufacturing to produce parts with a balanced combination of hardness and toughness.
Key Points Explained:
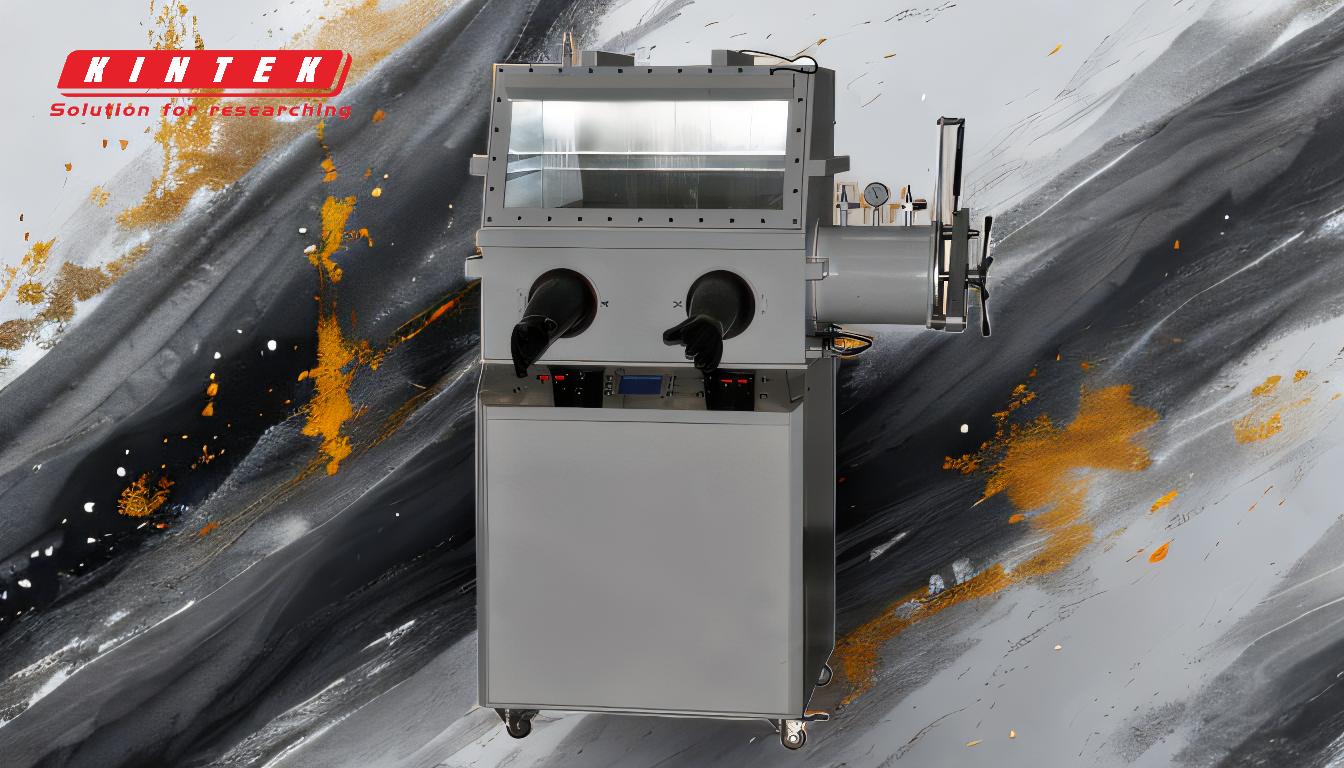
-
Definition and Purpose of Tempering:
- Tempering is a heat treatment process performed after hardening (quenching) to reduce brittleness and internal stresses in metals, particularly steel.
- It improves toughness, ductility, and overall durability while maintaining a balance between hardness and strength.
- The process involves reheating the metal to a specific temperature below its critical point and then cooling it.
-
Quench and Temper Process:
- A common example of tempering is the quench and temper process, which is used for medium carbon alloy steels.
-
Steps involved:
- Heating: The steel is heated above its transformation range (typically over 900°C).
- Quenching: The steel is rapidly cooled using a quenching medium like oil, water, or gas to achieve maximum hardness.
- Tempering: The quenched steel is reheated to a lower temperature (below the critical point) to reduce brittleness and achieve the desired final hardness and toughness.
-
Benefits of Tempering:
- Improved Toughness: Tempering introduces ductility, making the material less prone to cracking under stress.
- Stress Relief: It removes internal strains caused by rapid cooling during quenching.
- Balanced Properties: The process allows for precise control over the ratio of hardness to toughness, depending on the application requirements.
-
Applications of Tempering:
- Tempering is widely used in industries such as steel pipe manufacturing, automotive, aerospace, and toolmaking.
- It is essential for producing components that require high strength, wear resistance, and durability, such as gears, shafts, and cutting tools.
-
Microstructural Changes During Tempering:
- Tempering causes the formation of specific microstructures like troostite (soft and tough) or sorbite (weaker but more ductile).
- These structures contribute to the material's improved mechanical properties.
-
Comparison with Other Heat Treatment Processes:
- Unlike hardening, which focuses on increasing hardness and strength, tempering emphasizes toughness and ductility.
- Other heat treatment processes, such as case hardening or induction hardening, target specific sections of a material, whereas tempering is applied uniformly.
-
Importance in Manufacturing:
- Tempering is a crucial step in the production of high-performance steel components.
- It ensures that parts can withstand high stress and harsh operating conditions without failing.
By understanding the tempering process and its applications, manufacturers can produce materials with tailored properties to meet specific industrial needs. This process is a cornerstone of modern metallurgy, enabling the creation of durable and reliable components for a wide range of industries.
Summary Table:
Aspect | Details |
---|---|
Purpose | Reduces brittleness and internal stresses, improves toughness and ductility. |
Process Steps | 1. Heating, 2. Quenching, 3. Tempering. |
Key Benefits | Improved toughness, stress relief, balanced hardness and toughness. |
Applications | Steel manufacturing, automotive, aerospace, toolmaking. |
Microstructural Changes | Formation of troostite or sorbite for enhanced mechanical properties. |
Discover how tempering can optimize your metal components—contact our experts today!