Cold Isostatic Pressing (CIP) is a critical process in powder metallurgy, primarily used for compacting metal powders into a desired shape before sintering. This method applies uniform pressure from all directions, ensuring even density and microstructure throughout the workpiece. CIP is especially beneficial for creating complex shapes and dimensions that are difficult to achieve with traditional pressing methods. The process offers numerous advantages, including uniform strength, reduced warpage, shape flexibility, and cost efficiency, making it a preferred technique for producing high-quality, near-net-shape components.
Key Points Explained:
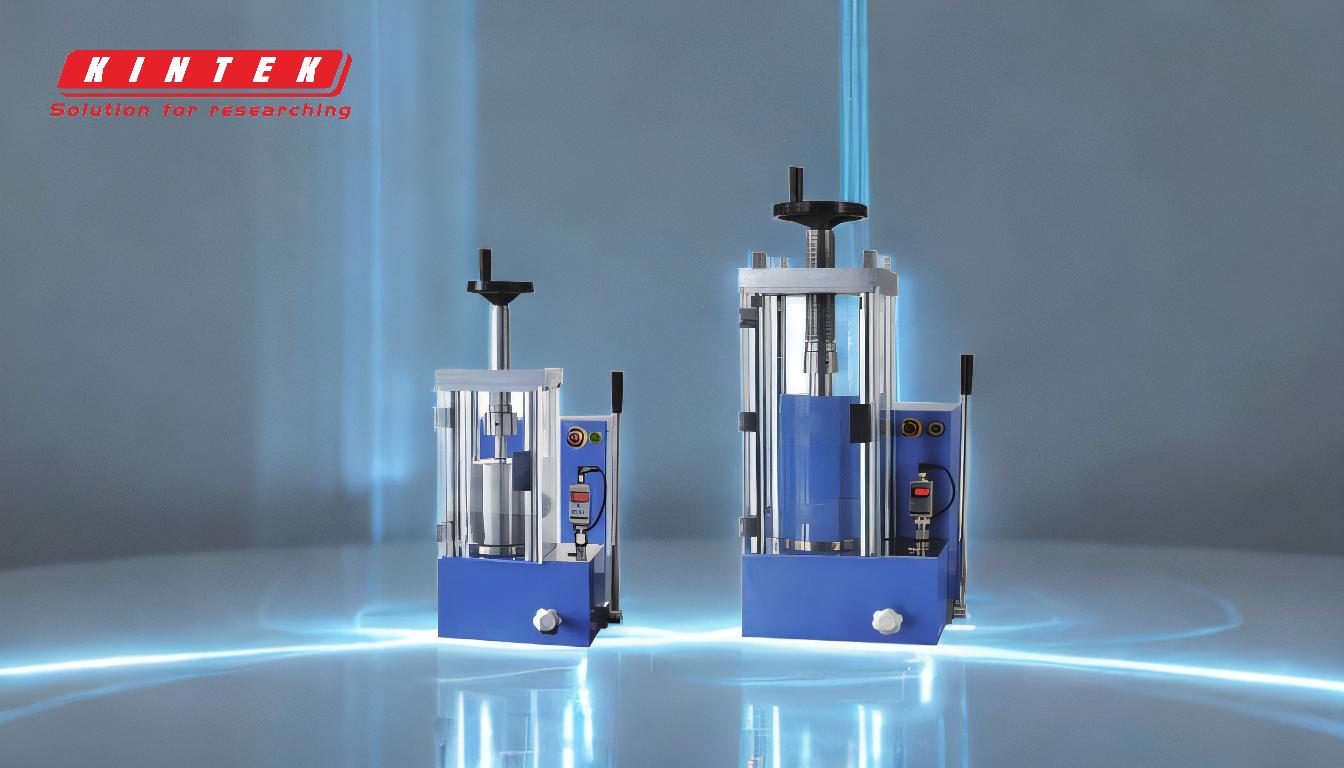
-
Definition and Purpose of CIP in Powder Metallurgy:
- Cold Isostatic Pressing (CIP) is a powder compaction process where equal pressure is applied uniformly to the entire surface of the workpiece. This ensures consistent density and microstructure, which are crucial for the final product's performance.
- CIP is typically used before sintering, a thermal process that bonds the powder particles into a solid mass. The uniform pressure application in CIP helps achieve a higher initial density, which accelerates consolidation during sintering.
-
Advantages of CIP:
- Uniform Strength and Density: Since pressure is applied equally from all directions, the resulting product has uniform strength and density, reducing the risk of weak spots or warpage.
- Shape Flexibility: CIP is particularly useful for producing complex shapes and dimensions that are difficult to achieve with traditional pressing methods.
- Cost Efficiency: The process allows for low tooling costs, especially beneficial for short production runs, and reduces material and machining costs by producing near-net-shape parts.
- Enhanced Alloying Possibilities: CIP enables the use of advanced alloys without segregation, enhancing the material properties of the final product.
-
Applications and Benefits in Powder Metallurgy:
- CIP is integral to powder metallurgy, enabling the production of components with precise dimensional control and desirable microstructures.
- The process is particularly advantageous for creating massive to small parts, offering flexibility in component size.
- The higher initial density achieved through CIP significantly speeds up the consolidation process during the thermal cycle, reducing lead times for complex shapes.
-
Comparison with Other Pressing Methods:
- Unlike uniaxial pressing, where pressure is applied from one or two directions, CIP applies pressure uniformly from all directions. This results in a more uniform density and microstructure, which is critical for high-performance applications.
- The isostatic press method is especially beneficial for materials that are difficult to compact using traditional methods, such as ceramics and certain metal powders.
-
Future Trends and Advancements:
- Advances in powder metallurgy, such as improved powder fragmentation, alloy development, and binder systems, are enhancing the capabilities of CIP.
- These advancements are enabling the production of even more complex-shaped components with precise dimensional control and desirable microstructures, further expanding the applications of CIP in various industries.
In summary, Cold Isostatic Pressing (CIP) is a versatile and efficient method in powder metallurgy, offering numerous advantages such as uniform density, shape flexibility, and cost efficiency. Its ability to produce complex shapes with precise dimensional control makes it an essential process in the production of high-quality, near-net-shape components. For more detailed information on isostatic pressing, you can refer to isostatic press.
Summary Table:
Aspect | Details |
---|---|
Definition | Uniform pressure applied from all directions to compact metal powders. |
Purpose | Ensures consistent density and microstructure for high-performance parts. |
Advantages | - Uniform strength and density - Shape flexibility - Cost efficiency |
Applications | Produces complex shapes with precise dimensional control. |
Comparison | Superior to uniaxial pressing for uniform density and microstructure. |
Future Trends | Enhanced alloy development and binder systems for advanced applications. |
Learn how CIP can optimize your powder metallurgy process—contact our experts today!