An ethylene cracking furnace is a critical piece of equipment in the petrochemical industry, primarily used to produce ethylene, a key building block for plastics and other chemicals. It operates by thermally cracking hydrocarbons, such as ethane or naphtha, at high temperatures (typically 750–900°C) in the presence of steam. This process breaks down larger hydrocarbon molecules into smaller ones, with ethylene being the primary product. The furnace consists of a radiant section where cracking occurs and a convection section for heat recovery. The design and operation of these furnaces are optimized for efficiency, safety, and product yield. Advanced technologies, such as IGBT furnaces, are sometimes integrated to improve energy efficiency and control.
Key Points Explained:
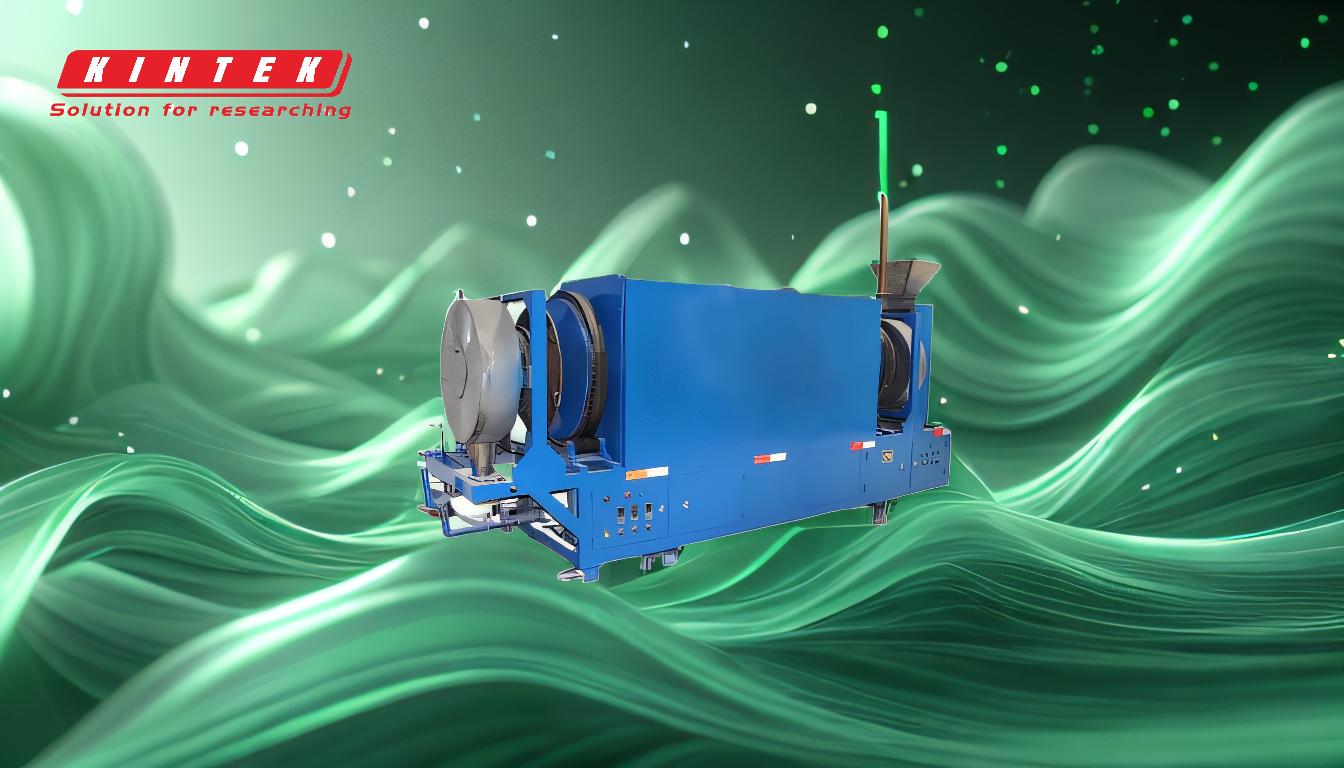
-
Purpose and Importance of Ethylene Cracking Furnaces:
- Ethylene cracking furnaces are essential for producing ethylene, a fundamental chemical used in manufacturing plastics, resins, and other petrochemical products.
- The process of thermal cracking transforms heavier hydrocarbons into lighter, more valuable products like ethylene, propylene, and butadiene.
-
Operating Principles:
- The furnace operates by heating hydrocarbons (e.g., ethane, propane, or naphtha) in the presence of steam to very high temperatures (750–900°C).
- This thermal cracking process breaks the chemical bonds in the hydrocarbon molecules, producing smaller molecules, primarily ethylene.
- The process is endothermic, requiring significant energy input, which is why heat recovery systems are integral to the design.
-
Components of an Ethylene Cracking Furnace:
- Radiant Section: This is where the cracking reaction takes place. Tubes in this section are exposed to high temperatures from burners, facilitating the breakdown of hydrocarbons.
- Convection Section: Located above the radiant section, it recovers heat from the flue gases to preheat the feedstock and generate steam, improving overall energy efficiency.
- Burners: Provide the necessary heat for the cracking process, often using fuels like natural gas or refinery gas.
- Quench System: Rapidly cools the cracked gases to stop further reactions and prevent degradation of the desired products.
-
Types of Feedstocks:
- Ethylene cracking furnaces can process various feedstocks, including ethane, propane, butane, naphtha, and gas oils.
- The choice of feedstock depends on availability, cost, and the desired product slate. For example, ethane cracking primarily produces ethylene, while naphtha cracking yields a broader range of products.
-
Energy Efficiency and Advanced Technologies:
- Modern ethylene cracking furnaces incorporate advanced technologies to improve energy efficiency and reduce emissions.
- For instance, IGBT furnaces use insulated gate bipolar transistors to enhance control over heating processes, leading to better energy utilization and reduced operational costs.
- Heat integration techniques, such as using waste heat to generate steam or preheat feedstocks, are also employed to maximize efficiency.
-
Challenges and Considerations:
- High operating temperatures and pressures pose challenges related to material durability and safety.
- Coke formation inside the tubes is a common issue, requiring periodic decoking operations to maintain efficiency.
- Environmental regulations demand stringent control of emissions, driving the adoption of cleaner technologies and more efficient designs.
-
Applications of Ethylene:
- The ethylene produced in these furnaces is a key raw material for manufacturing polyethylene, ethylene oxide, ethylene glycol, and other chemicals.
- These products are used in a wide range of industries, including packaging, automotive, construction, and textiles.
-
Future Trends:
- There is a growing focus on developing more sustainable and energy-efficient cracking processes, such as electrification of furnaces and the use of renewable feedstocks.
- Innovations like IGBT furnaces and advanced process control systems are expected to play a significant role in the future of ethylene production.
By understanding the design, operation, and advancements in ethylene cracking furnaces, stakeholders in the petrochemical industry can make informed decisions to optimize production, reduce costs, and meet environmental goals.
Summary Table:
Aspect | Details |
---|---|
Purpose | Produces ethylene, a key raw material for plastics and petrochemicals. |
Operating Temperature | 750–900°C, using steam to thermally crack hydrocarbons. |
Key Components | Radiant section, convection section, burners, and quench system. |
Feedstocks | Ethane, propane, naphtha, and gas oils. |
Advanced Technologies | IGBT furnaces for energy efficiency and precise control. |
Applications | Used in packaging, automotive, construction, and textiles industries. |
Future Trends | Electrification, renewable feedstocks, and advanced process control systems. |
Discover how ethylene cracking furnaces can optimize your production—contact our experts today!