Hot isostatic pressing (HIP) is a manufacturing process that combines high temperature and high pressure to improve the properties of materials, particularly metals and ceramics. The process involves placing materials in a pressurized vessel filled with an inert gas, such as argon, and applying uniform pressure from all directions while simultaneously heating the material. This simultaneous application of heat and pressure helps eliminate internal porosity, increase material density, and enhance mechanical properties such as fatigue life, ductility, and toughness. HIP is widely used in industries like aerospace, automotive, and medical devices to produce components with superior strength and uniformity.
Key Points Explained:
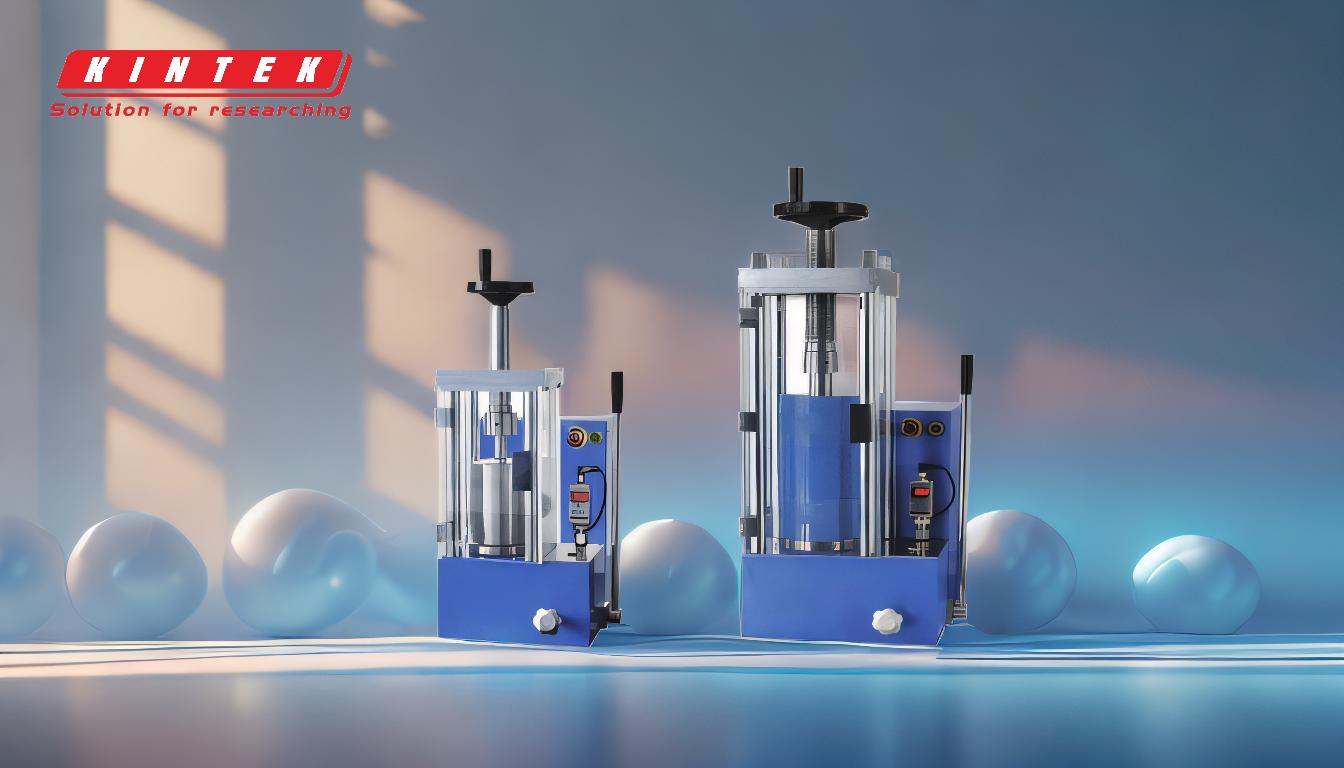
-
Process Overview:
- Hot isostatic pressing (HIP) involves placing materials in a pressurized vessel and applying uniform pressure from all directions using an inert gas like argon.
- Heat is simultaneously applied to the material, typically below its melting point, to enhance densification and eliminate internal porosity.
-
Steps in the HIP Process:
- Loading: The material or powder is loaded into a flexible mold or directly into the HIP chamber.
- Sealing: The mold or chamber is sealed to ensure no gas leakage during the process.
- Pressurization: The chamber is pressurized with an inert gas, and heat is applied to increase the pressure over time.
- Densification: The combination of heat and pressure eliminates pores and increases the material's density.
- Depressurization and Cooling: After the process, the chamber is depressurized and cooled to safely remove the processed material.
-
Benefits of HIP:
- Improved Mechanical Properties: HIP enhances properties like fatigue life, ductility, impact strength, and toughness by eliminating internal defects.
- Uniform Grain Structure: The process creates materials with fine, uniform grain sizes and isotropic structures, ensuring consistent performance in all directions.
- Densification of Powders: HIP is particularly effective for densifying powders in the solid state, making it ideal for producing complex 3D shapes.
-
Applications of HIP:
- HIP is widely used in industries requiring high-performance materials, such as aerospace (for turbine blades and engine components), automotive (for lightweight and durable parts), and medical devices (for biocompatible implants).
- It is also used in the production of ceramics and advanced materials where uniform density and mechanical strength are critical.
-
Equipment and Control:
- HIP equipment typically includes a pressurized chamber, heating elements, and computer-controlled systems to regulate temperature, pressure, and process time.
- Operators can program the equipment to achieve specific results based on the material and final product requirements.
-
Comparison with Other Processes:
- Unlike traditional sintering, which relies solely on heat, HIP combines heat and pressure to achieve densification, resulting in superior material properties.
- HIP is particularly effective for materials that are difficult to process using conventional methods, such as refractory metals and ceramics.
By understanding the principles and steps of the hot isostatic pressing process, manufacturers can leverage its benefits to produce high-quality, defect-free materials with enhanced mechanical properties. This makes HIP an invaluable tool in modern manufacturing and materials engineering.
Summary Table:
Aspect | Details |
---|---|
Process Overview | Combines high temperature and pressure using inert gas (e.g., argon). |
Key Steps | Loading, sealing, pressurization, densification, depressurization, cooling. |
Benefits | Eliminates porosity, enhances mechanical properties, and ensures uniformity. |
Applications | Aerospace, automotive, medical devices, ceramics, and advanced materials. |
Equipment | Pressurized chamber, heating elements, and computer-controlled systems. |
Comparison | Superior to sintering; ideal for refractory metals and ceramics. |
Learn how hot isostatic pressing can revolutionize your manufacturing process—contact our experts today!