Refractory ceramics are specialized engineered materials designed to withstand extreme temperatures and harsh conditions, making them essential in industrial processes such as furnace linings, manufacturing, and high-temperature applications. These materials are composed of compounds like alumina, silicon carbide, and zirconium oxide, which provide high thermal stability, mechanical strength, and chemical resistance. Refractory ceramics are often used in multi-layer insulation designs to minimize heat loss and energy consumption. Their unique properties, including high melting points, wear resistance, and low oxidation rates, make them indispensable in industries requiring precise and uniform process conditions.
Key Points Explained:
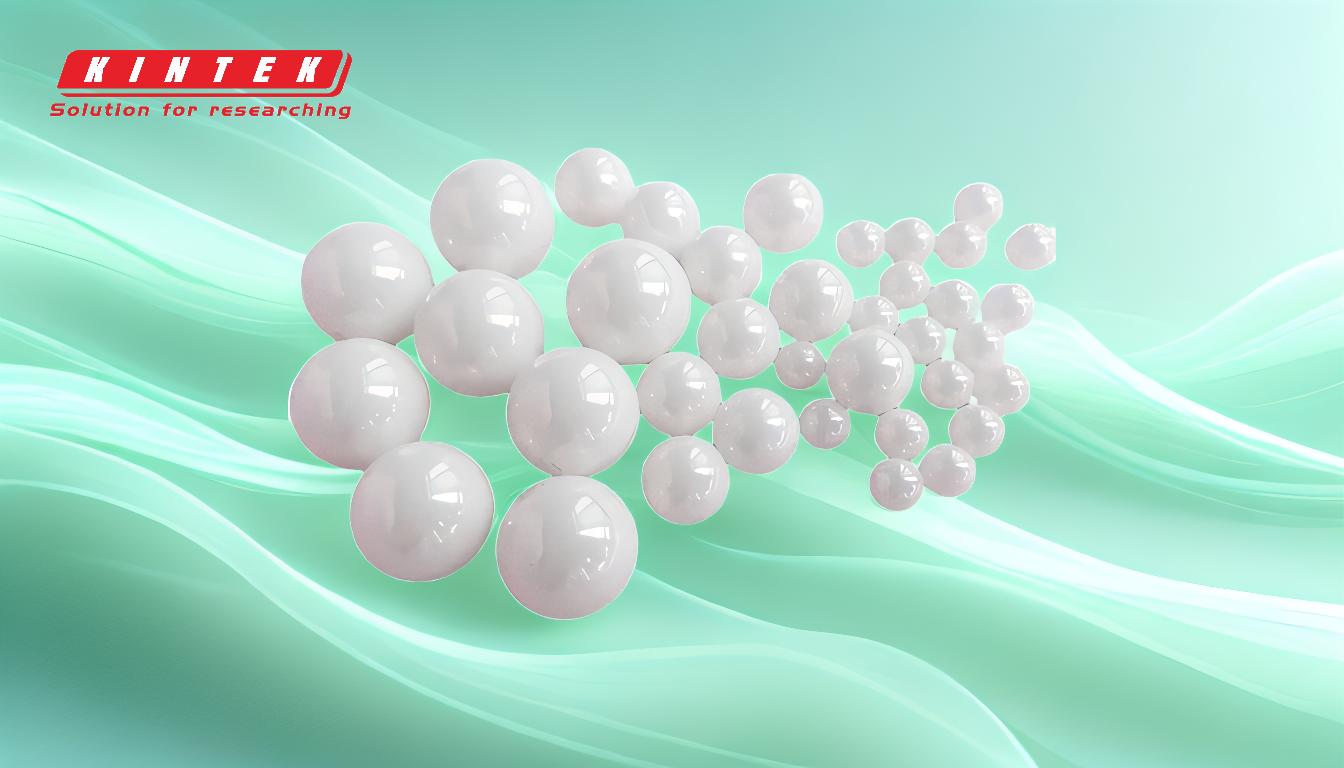
-
Definition and Purpose of Refractory Ceramics:
- Refractory ceramics are engineered materials specifically designed to endure extreme temperatures and harsh environments.
- They are used in industrial processes such as furnace linings, manufacturing, and other high-temperature applications where standard materials would fail.
-
Composition of Refractory Ceramics:
- These materials are typically made from compounds like alumina (Al₂O₃), silicon carbide (SiC), zirconium oxide (ZrO₂), magnesium oxide (MgO), and other ceramic raw materials.
- Some refractory ceramics may include organic additives during the pre-sintering stage to improve their properties.
-
Key Properties:
- High Thermal Stability: Refractory ceramics can withstand extreme temperatures without degrading, making them ideal for furnace linings and high-temperature processes.
- Mechanical Strength: They exhibit high strength and hardness, ensuring durability under mechanical stress.
- Chemical Resistance: These materials are resistant to corrosion and chemical reactions, even in harsh environments.
- Low Oxidation Rates: Refractory ceramics have slow diffusion rates and low oxidation resistance, which is crucial for maintaining performance at high temperatures.
-
Applications in Industry:
- Furnace Linings: Refractory ceramics are commonly used in muffle furnaces and other high-temperature furnaces. They ensure accurate and uniform process conditions by maintaining thermal stability.
- Insulation: Multi-layer designs using lightweight alumina ceramic fiber and insulation boards minimize heat loss and energy consumption.
- High-Temperature Manufacturing: These materials are essential in processes like metal smelting, glass production, and chemical manufacturing, where extreme temperatures are required.
-
Advantages Over Traditional Materials:
- Refractory ceramics outperform traditional materials like metals and standard ceramics in high-temperature applications due to their superior thermal, mechanical, and chemical properties.
- They are more durable and resistant to wear, making them cost-effective in the long run despite their higher initial cost.
-
Environmental and Safety Considerations:
- Modern refractory ceramics are designed to be free of harmful components like asbestos, ensuring safety and environmental compliance.
- Their low heat loss properties contribute to energy efficiency, reducing the environmental impact of industrial processes.
-
Comparison with Refractory Metals:
- Refractory metals (e.g., tungsten, molybdenum) also have high melting points and wear resistance but are more prone to oxidation at high temperatures.
- Refractory ceramics, on the other hand, offer better oxidation resistance and are more suitable for applications requiring long-term stability in extreme conditions.
-
Future Trends and Innovations:
- Advances in ceramic technology are leading to the development of even more durable and efficient refractory materials.
- Research is focused on improving the thermal conductivity, strength, and environmental sustainability of these materials to meet the growing demands of modern industry.
In summary, refractory ceramics are critical materials in high-temperature industrial applications due to their exceptional thermal stability, mechanical strength, and chemical resistance. Their unique properties and versatility make them indispensable in ensuring efficient and reliable industrial processes.
Summary Table:
Aspect | Details |
---|---|
Definition | Engineered materials for extreme temperatures and harsh environments. |
Composition | Alumina, silicon carbide, zirconium oxide, magnesium oxide, and more. |
Key Properties | High thermal stability, mechanical strength, chemical resistance, low oxidation rates. |
Applications | Furnace linings, insulation, metal smelting, glass production, and more. |
Advantages | Superior thermal, mechanical, and chemical properties; durable and cost-effective. |
Environmental Impact | Free of harmful components; energy-efficient with low heat loss. |
Future Trends | Advances in durability, efficiency, and sustainability. |
Learn how refractory ceramics can enhance your industrial processes—contact our experts today!