The basic lining material for induction furnaces primarily consists of refractory materials designed to withstand extreme temperatures and harsh conditions. These materials include magnesia, dolomite, and alumina, which have high melting points and excellent thermal resistance. Additionally, advanced lining materials such as high-purity alumina fiber, vacuum-formed fiber material, and light hollow aluminum oxide plates are used for their superior thermal insulation, rapid heat and cold resistance, and durability. The lining serves critical functions, including containing molten metal, isolating it from the furnace's outer structure, and protecting the furnace body. The choice of lining material depends on the type of metal being processed and the specific operational requirements of the furnace.
Key Points Explained:
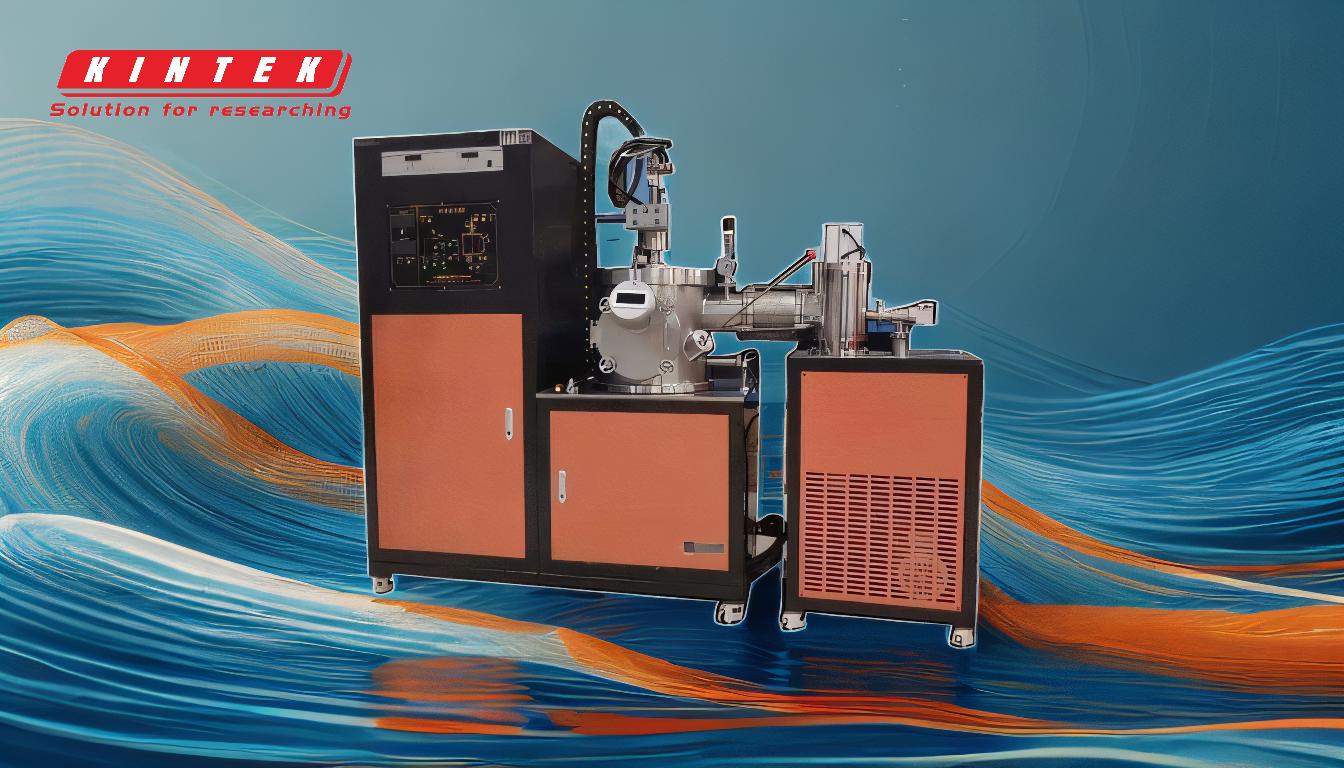
-
Primary Refractory Materials for Induction Furnace Linings:
- Magnesia (MgO): A widely used refractory material due to its high melting point (approximately 2,800°C) and excellent resistance to basic slags. It is particularly suitable for melting ferrous metals.
- Dolomite (CaMg(CO₃)₂): A natural mineral that, when calcined, provides good thermal stability and resistance to thermal shock. It is often used in furnaces processing steel and iron.
- Alumina (Al₂O₃): Known for its high melting point (around 2,072°C) and excellent thermal insulation properties. It is ideal for melting non-ferrous metals like aluminum and copper.
-
Advanced Lining Materials:
- High-Purity Alumina Fiber: Offers high service temperatures, low heat storage capacity, and rapid heat and cold resistance. It is lightweight and provides excellent thermal insulation.
- Vacuum-Formed Fiber Material: Combines high thermal resistance with structural integrity, ensuring no cracking or slag falling during operation.
- Light Hollow Aluminum Oxide Plate: Provides superior thermal insulation and durability, making it suitable for high-temperature applications.
-
Functions of the Induction Furnace Lining:
- Containment of Molten Metal: The lining must securely hold the molten metal without leakage or contamination.
- Isolation from Outer Structure: It prevents contact between the molten metal and the furnace's outer components, such as the induction coil, ensuring safety and operational efficiency.
- Protection of Furnace Body: The lining shields the furnace from thermal and mechanical stresses, extending its lifespan.
-
Material Selection Based on Application:
- For melting ferrous metals (e.g., steel, iron), magnesia and dolomite are preferred due to their resistance to basic slags.
- For non-ferrous metals (e.g., aluminum, copper), alumina-based materials are ideal because of their thermal insulation and chemical stability.
- Advanced materials like high-purity alumina fiber are used in specialized applications requiring rapid temperature changes and minimal heat loss.
-
Operational Considerations:
- Thermal Shock Resistance: The lining must withstand rapid heating and cooling cycles without cracking.
- Chemical Stability: It should resist chemical reactions with molten metals and slags.
- Durability: The lining must maintain its structural integrity over prolonged use to minimize downtime and maintenance costs.
-
Comparison with Other Furnace Types:
- Unlike rotary furnaces, which use refractory castables for lining, induction furnaces rely on pre-formed refractory materials or advanced fiber-based linings for better thermal efficiency and performance.
In summary, the choice of lining material for an induction furnace depends on the specific application, the type of metal being melted, and the operational conditions. The materials must provide high thermal resistance, durability, and chemical stability to ensure efficient and safe furnace operation.
Summary Table:
Material | Key Properties | Applications |
---|---|---|
Magnesia (MgO) | High melting point (~2,800°C), resistance to basic slags | Melting ferrous metals (steel, iron) |
Dolomite (CaMg(CO₃)₂) | Thermal stability, resistance to thermal shock | Processing steel and iron |
Alumina (Al₂O₃) | High melting point (~2,072°C), excellent thermal insulation | Melting non-ferrous metals (aluminum, copper) |
High-Purity Alumina Fiber | High service temperature, rapid heat/cold resistance, lightweight | Specialized high-temperature applications |
Vacuum-Formed Fiber | High thermal resistance, structural integrity | High-performance applications |
Light Hollow Al₂O₃ Plate | Superior thermal insulation, durability | High-temperature, rapid heating/cooling |
Need help selecting the right lining material for your induction furnace? Contact our experts today for tailored solutions!