The dew point of a furnace atmosphere is a critical parameter in heat treatment processes, as it indicates the temperature at which moisture in the gas mixture begins to condense. Understanding and controlling the dew point is essential for maintaining the desired chemical reactions, preventing oxidation, and ensuring the quality of the treated materials. The dew point is influenced by the composition and purity of the furnace atmosphere, as well as the temperature and humidity of the environment. By carefully monitoring and adjusting the dew point, operators can optimize the furnace atmosphere to achieve consistent and reliable results in heat treatment applications.
Key Points Explained:
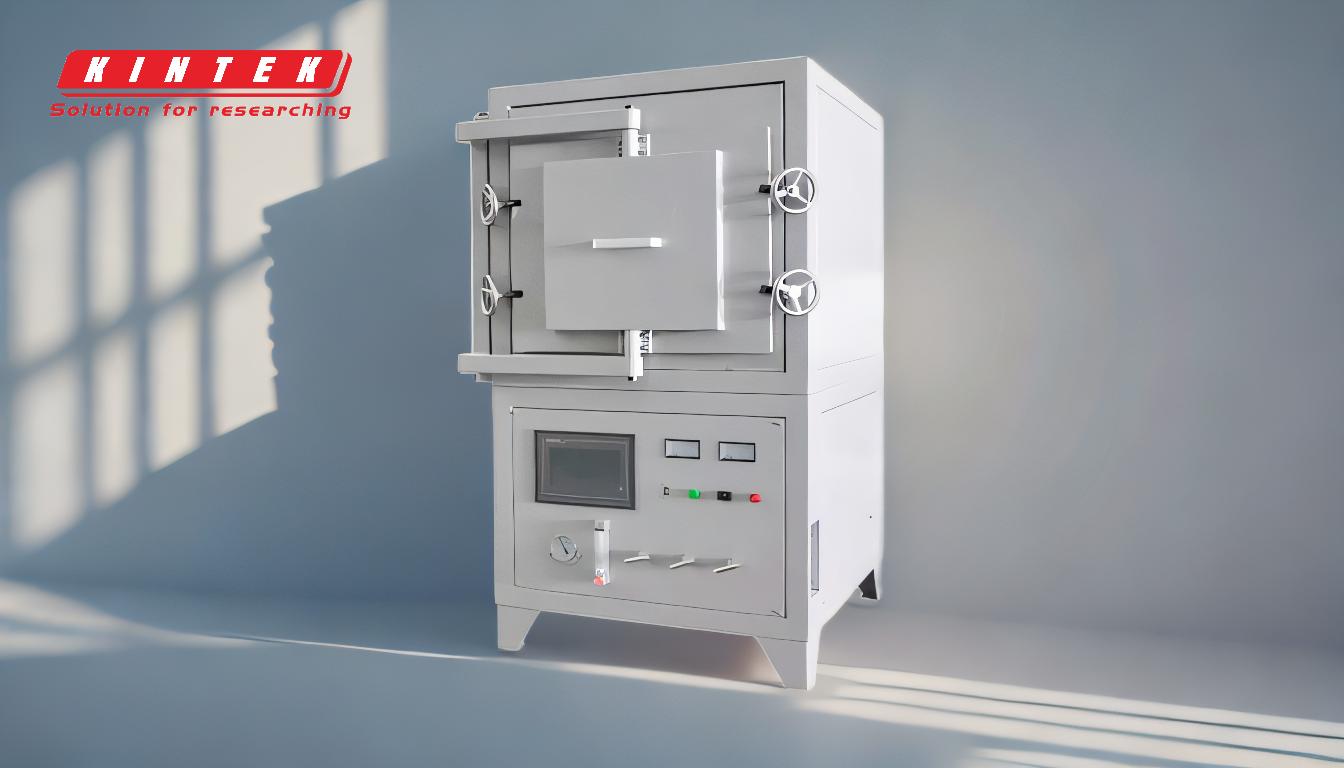
-
Definition of Dew Point in a Furnace Atmosphere:
- The dew point is the temperature at which the water vapor in the furnace atmosphere starts to condense into liquid water. This is a critical parameter because excessive moisture can lead to oxidation, decarburization, or other undesirable chemical reactions during heat treatment.
- For example, in carburizing processes, maintaining a low dew point ensures that the carbon potential of the atmosphere remains stable, preventing inconsistencies in the surface hardness of the treated material.
-
Importance of Controlling the Dew Point:
- Controlling the dew point is essential for achieving the desired metallurgical properties in heat-treated materials. For instance, in annealing processes, a high dew point can cause surface oxidation, leading to poor surface finish and reduced mechanical properties.
- In processes like nitriding or brazing, maintaining a specific dew point ensures that the atmosphere remains inert and free from contaminants that could interfere with the treatment.
-
Factors Influencing the Dew Point:
- Gas Composition: The type of gas used in the furnace atmosphere (e.g., nitrogen, argon, hydrogen) and its purity level significantly affect the dew point. For example, hydrogen has a strong affinity for moisture, so even small impurities can raise the dew point.
- Temperature and Humidity: The ambient temperature and humidity of the environment where the furnace operates can influence the dew point. Higher humidity levels increase the likelihood of moisture entering the furnace atmosphere.
- Material Being Processed: The reactivity of the material with moisture also plays a role. For instance, materials like titanium or aluminum are highly sensitive to moisture, requiring a very low dew point to prevent oxidation.
-
Measurement and Control of Dew Point:
- Dew point sensors or hygrometers are commonly used to measure the moisture content in the furnace atmosphere. These devices provide real-time data, allowing operators to adjust the gas flow or introduce drying agents to maintain the desired dew point.
- Advanced furnace systems often integrate automated controls that adjust the atmosphere composition based on dew point readings, ensuring consistent results.
-
Practical Applications and Examples:
- In carburizing, a low dew point (e.g., -40°C to -60°C) is maintained to ensure a high carbon potential, which is necessary for achieving a hard surface layer on steel components.
- In annealing, a slightly higher dew point (e.g., -10°C to 0°C) might be acceptable, depending on the material and desired outcome. However, exceeding this range can lead to surface defects.
- For sensitive materials like titanium, a dew point as low as -70°C may be required to prevent oxidation and ensure optimal mechanical properties.
By understanding and controlling the dew point of a furnace atmosphere, operators can optimize heat treatment processes, improve product quality, and reduce waste. This parameter is particularly important in industries where precision and consistency are critical, such as aerospace, automotive, and tool manufacturing.
Summary Table:
Aspect | Details |
---|---|
Definition | Temperature at which moisture condenses in the furnace atmosphere. |
Importance | Prevents oxidation, decarburization, and ensures material quality. |
Influencing Factors | Gas composition, temperature, humidity, and material reactivity. |
Measurement Tools | Dew point sensors or hygrometers for real-time monitoring. |
Applications | Carburizing (-40°C to -60°C), annealing (-10°C to 0°C), titanium (-70°C). |
Optimize your heat treatment processes with precise dew point control—contact our experts today!