The core-type induction furnace and coreless induction furnace are two distinct types of induction furnaces used in metal melting, each with unique designs, operational principles, and applications. The core-type furnace operates on a transformer principle with high power efficiency (up to 98%) and is ideal for high-throughput operations with minimal alloy changes. However, it requires continuous maintenance and cannot be easily shut down. In contrast, the coreless furnace operates without a core or secondary coil, inducing currents directly into the metal charge. It offers flexibility in alloy changes and can be started cold but has lower power efficiency (around 75%) and may experience reduced refractory lining life due to frequent alloy changes.
Key Points Explained:
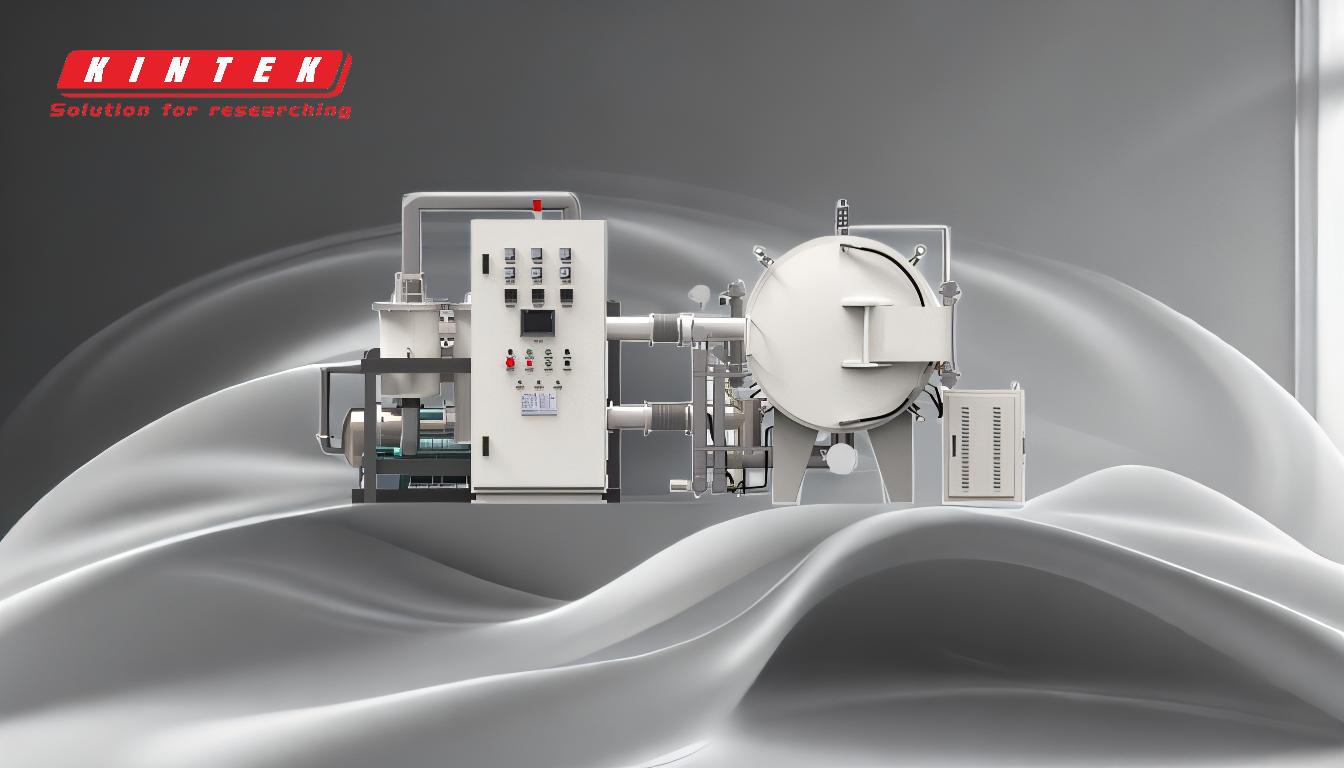
-
Design and Construction:
-
Core-Type Furnace:
- Features a primary coil surrounding an iron core and a secondary coil formed by a loop of molten metal.
- Operates on the principle of a transformer, with high power efficiency (up to 98%).
- Requires continuous maintenance of the metal loop and is rarely allowed to cool.
-
Coreless Furnace:
- Lacks a core or secondary coil; the primary coil directly surrounds the metal charge.
- Operates by inducing currents directly into the metal charge.
- Can be shut down and started cold, making it suitable for frequent alloy changes.
-
Core-Type Furnace:
-
Operational Principles:
-
Core-Type Furnace:
- Uses an alternating current in the primary coil to induce a larger current in the molten metal loop, generating heat via the Joule Effect.
- Ideal for high-throughput, high-production operations with few alloy changes.
-
Coreless Furnace:
- Induces eddy currents directly in the metal charge, simplifying the melting process.
- Operates across a wide frequency range (50 Hz to 10 kHz), providing flexibility in melting different metals.
-
Core-Type Furnace:
-
Efficiency and Power Consumption:
-
Core-Type Furnace:
- Highly efficient, with power efficiency up to 98%.
- Suitable for continuous operations with minimal downtime.
-
Coreless Furnace:
- Lower power efficiency (approximately 75%).
- More suitable for operations requiring frequent alloy changes or batch processing.
-
Core-Type Furnace:
-
Applications and Suitability:
-
Core-Type Furnace:
- Best for long-run operations with consistent metal types, such as in foundries or large-scale production facilities.
- Not ideal for operations requiring frequent alloy changes due to maintenance challenges.
-
Coreless Furnace:
- Ideal for operations requiring flexibility, such as small-scale production or frequent alloy changes.
- Commonly used in foundries and workshops where versatility is prioritized over efficiency.
-
Core-Type Furnace:
-
Maintenance and Lifespan:
-
Core-Type Furnace:
- Requires continuous maintenance of the molten metal loop.
- Refractory lining and components have a longer lifespan in stable operations.
-
Coreless Furnace:
- Easier to maintain due to its simpler design.
- Frequent alloy changes may reduce the lifespan of the refractory lining.
-
Core-Type Furnace:
-
Flexibility and Operational Control:
-
Core-Type Furnace:
- Less flexible due to the need for continuous operation and maintenance.
- Better suited for consistent, high-volume production.
-
Coreless Furnace:
- Offers greater flexibility with the ability to start cold and change alloys easily.
- Suitable for smaller-scale or variable production needs.
-
Core-Type Furnace:
In summary, the choice between a core-type and coreless induction furnace depends on the specific operational requirements, such as production volume, alloy flexibility, and efficiency needs. Core-type furnaces excel in high-efficiency, continuous operations, while coreless furnaces provide greater flexibility for operations requiring frequent alloy changes or batch processing.
Summary Table:
Feature | Core-Type Furnace | Coreless Furnace |
---|---|---|
Design | Primary coil with iron core; secondary coil formed by molten metal loop. | No core or secondary coil; primary coil directly surrounds metal charge. |
Efficiency | High (up to 98%). | Lower (around 75%). |
Operational Flexibility | Limited; requires continuous operation and maintenance. | High; can start cold and handle frequent alloy changes. |
Applications | Ideal for high-throughput, consistent metal types (e.g., foundries). | Suitable for small-scale production or frequent alloy changes. |
Maintenance | Continuous maintenance required; longer refractory lifespan in stable operations. | Easier maintenance; refractory lining may wear faster due to frequent alloy changes. |
Best For | High-efficiency, continuous operations. | Flexible, batch-processing operations. |
Still unsure which induction furnace is right for your needs? Contact our experts today for personalized advice!